If you read the news at least once in the last decade, you may be aware of the so-called 3d printing revolution. Although additive manufacturing has been used in the industry since the 1980s, it was not widely available to hobbyist users up until recently.
The creation of the RepRap project, in addition to the expiration of several patents, allowed for an accelerated decrease in the cost of hobby-grade 3d printers.
Now that almost everyone can get their hands on a 3d printer, a lot of people wonder about the limits of this technology, and especially if it is going to eventually replace traditional methods of production like Injection Molding.
Although 3D printing definitely has its own place in the industrial space, it is not going to replace traditional Injection-Molding production, at least in the following years to come. Both technologies have their advantages and disadvantages and can outperform the other in specific areas. While 3d printing is excellent for small production batches and for the creation of prototypes, Injection Molding is still the most cost-efficient for large productions.
Due to the lower cost of the materials and the power-efficiency of Injection Molding, it is the recommended production technology when producing more than (approximately) a hundred kilograms of plastic units of the same product.
- Why is 3d printing more expensive than Injection Molding?
- When should I use a 3d printer instead of injection molding?
- Is 3d printing slower than injection molding?
- Is 3d printing plastic the same as Injection-Molding plastic?
- Advantages and disadvantages of 3d printing and injection molding
- Conclusion
- Check out our recommended products section
Why is 3d printing more expensive than Injection Molding?
Assuming that you already have a mold to start your production, Injection Molding production is much cheaper than 3d printing on a per-unit basis. This is both due to the actual cost of the plastic used for both techniques and the energy efficiency of each technology.
Energy efficiency of 3d printing and injection molding
The average draw of a working 3d printer when printing at 200°C with a heated bed set at 60°C is approximately 125W/h. This means that 3d printing consumes on average 9.61kW per kilogram of plastic, whereas we would only require an average of 1.5kW for producing the same amount of plastic via Injection Molding.
Using an average rate of 13 cents per kW/h (a reasonable price for the United States), the cost of producing 1 kg of plastic becomes $1.25 for 3d printing and $0.19 for Injection Molding.
Although these numbers are a crude approximation, and the exact cost of each technology depends on the specific machine used and the models being produced, we can still conclude that injection molding is more efficient in terms of power consumption for roughly the same output (by a factor of more than 6).
The electricity consumption estimates used for this calculation are based on our own measurements of an Ender 3 v2 (check out Facundo’s article on the topic). You might have guessed that neither he nor I have an Injection-Molding machine at home, so I based these calculations on an average of multiple reputable sources.
Cost of plastic for 3d Printing and Injection Molding
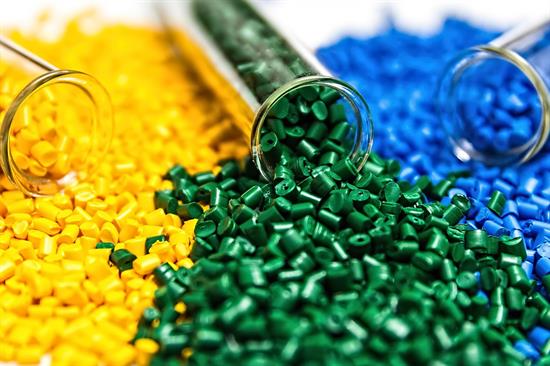
The cost per kilogram of material for 3d printers is roughly 20 times more expensive than the plastic pellets used for Injection Molding.
If you ever bought filament for a 3d printer, you can probably agree that it is not uncommon to pay $20 for a spool of PLA or ABS. Compare that to the average cost of $1 for a kilogram of ABS pellets and now we definitely know why most of our everyday life appliances are not 3d printed.
Is injection molding always cheaper than 3d printing?
Although we already determined that Injection Molding is way more cost-efficient for producing larger quantities of a given product, 3d printers also have their place in the industry.
Oftentimes, it is only necessary to produce a small to medium batch of a given product. This can be the case of a prototype or a product that only serves a niche market and will thus have limited demand.
For smaller quantities, the cost of the mold itself is very important. Roughly speaking, a single cavity mold (a simple one) can set you back between $1000 and $2000, whereas large and complex ones can cost up to $75.000.
Asking for the price of a mold is like asking for the price of a car, in that the range is huge. The valuation of my car is probably lower than the price of a Ferrari. Nonetheless, for the sake of comparing both technologies, I’ll compare both technologies assuming a mold cost of $10.000
As you can see from the chart below, injection-molding becomes more cost-efficient than 3d printing at roughly 500kg of produced items.
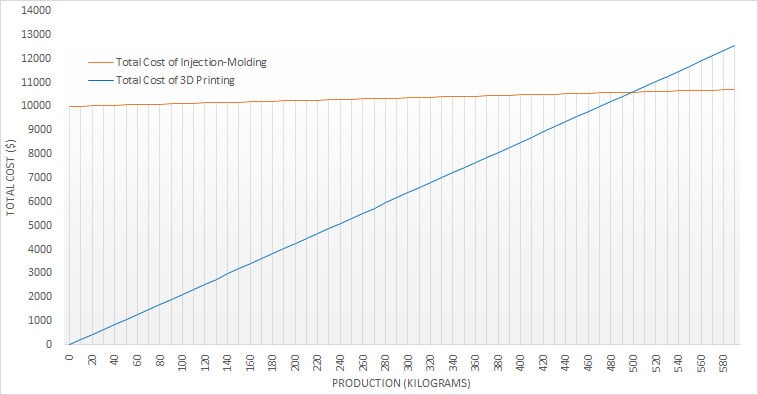
This inflection point (500kg) greatly depends on the cost of the mold itself. If we perform the same calculations again but assume a mold price of only $2.000 (for a simple single cavity mold), we should decide to switch from 3d printing to Injection Molding at approximately 100 kilograms.
When should I use a 3d printer instead of injection molding?
Additive manufacturing is more convenient in cases where the required production is of only a few dozens of kilograms. It is also recommended for quickly prototyping new models, because of the fact that it allows designers to iterate and optimize their models without incurring in significant costs.
3D printing technology also enables designers to design shapes that could not be produced with traditional manufacturing methods. The following Eiffel Tower that I printed with my Ender 3 v2 is impossible to produce with injection molding.
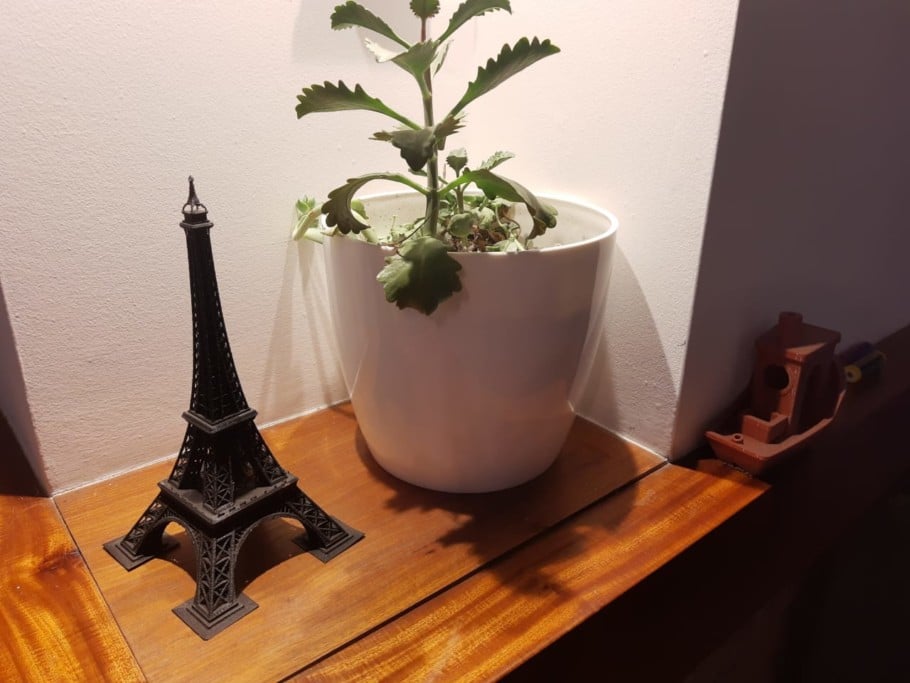
Is 3d printing slower than injection molding?
A 3d printer is definitely slower than an injection-molding machine. For example, it is not uncommon for such machines to produce up to 3.000 bottle caps per hour. A 3d printer would output one unit of the same item in approximately 15 minutes, which means that we would need 750 printers to match the same production rate. Conversely, we can also wait 750 hours to print the same amount of units.
Having said that, a 3d printer is definitely faster and more convenient when it comes down to quick iterations and small-batch productions. It is also very convenient during the prototyping process. By means of additive manufacturing technology, we can do sequential design sprints and quickly optimize and improve our models, something we would not be able to do if we choose to use Injection Molding.
Most importantly, the manufacturing of a mold can take up to 10 weeks, which means that we would have to wait at least that long in order to see our first produced unit. On the other hand, if we already have the G-Code of our design loaded on a USB stick, we can expect to have our first item on the same day.
Is 3d printing plastic the same as Injection-Molding plastic?
3d printing machines use spools of filament to produce the desired units, whereas Injection Molding manufacturing usually uses plastics in the shape of small pellets. Having said that, some types of thermoplastics are used in both technologies.
Polystyrene (HIPS), ABS and Nylon are popular materials used in both 3d printing and injection-molding. PLA is the most popular choice of plastic used in the 3d printing community, but it has almost no use cases in injection molding.
Other common plastics used in injection molding are Acrylic, Polypropylene, and Polyethylene, among others. These are not compatible with hobbyist desktop printers, mostly due to the high temperatures required to extrude them.
Industrial grade 3d printers, like the ones you can purchase from Stratasys or 3D Systems, are compatible with most thermoplastics. There is a small caveat: they will set you back a few hundred thousand dollars.
Advantages and disadvantages of 3d printing and injection molding
Both technologies have their applications where they outperform the other, so it is safe to say that both techniques are going to be used in the years (or decades) to come.
Although we already went through most of the advantages and disadvantages of each technology, let us quickly summarize them.
Advantages of 3d Printing over Injection-Molding
- Allows for fast iterations and design improvements
- Perfectly suited for small to medium batches
- Allows for personalized one of items
- Enables shapes and designs that are impossible to produce with other technologies
- Does not require upfront costs (i.e. a mold)
- Suitable for both hobbyists and prosumer alike
Advantages of Injection-Molding over 3d Printing
- Very cost-efficient for large quantities
- Consumes less electricity per kilogram of plastic
- Outputs high-quality products with fine details
- Large quantities of produced units per hour
- Compatible with a large array of thermoplastics
- Stronger and more resistant parts
Conclusion
In summary, it is safe to say that 3d printing will not replace traditional Injection Molding techniques. The fact that today’s 3d printers are unable to achieve the same quality and robustness that one can expect from injected parts poses a huge disadvantage for additive manufacturing. Additionally, the technology itself does not allow for the incredible rates of production that are achievable with the traditional manufacturing methods.
Check out our recommended products section
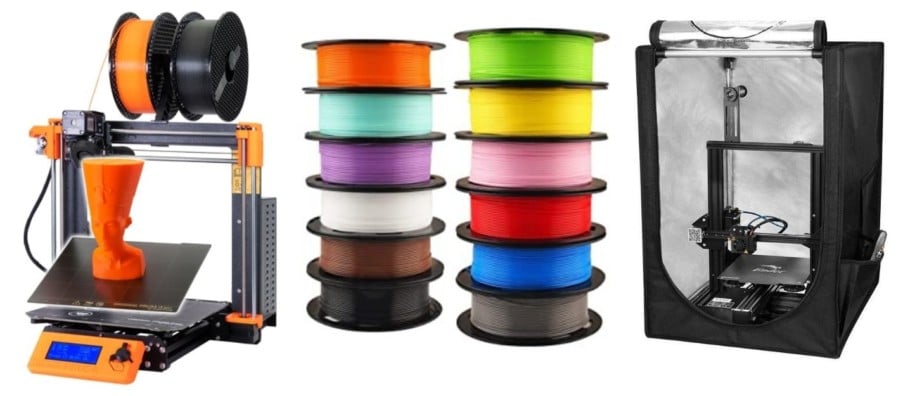
We created a recommended products section that will allow you to remove the guesswork and reduce the time spent researching what printer, filament, or upgrades to get, since we know that this can be a very daunting task and which generally leads to a lot of confusion.
We have selected just a handful of 3D printers that we consider to be good for beginners as well as intermediates, and even experts, making the decision easier, and the filaments, as well as the upgrades listed, were all tested by us and carefully selected, so you know that whichever one you choose will work as intended.
Error processing API data.