Most makers in the 3D printing community are aware of the importance of choosing a correct infill pattern and percentage when it comes to creating working parts for both prototypes and production purposes.
In recent years, many new patterns have emerged in order to address specific technical issues. Some patterns found their place in the maker’s toolbox, while others were tossed away and are remembered as an interesting experiment.
You may be aware of the existence of the Gyroid Infill, which is interesting because of multiple factors. Let’s find out what the gyroid pattern is and how it is useful.
The Gyroid Infill is a pattern whose most important feature is its cubic symmetry, which in contrast to all other patterns is an almost isotropic structure, which means that it is equally resistant to forces coming from all directions. Its main advantage is its sheer resistance and overall strength, even at lower infill percentages.
What is a Gyroid Infill?
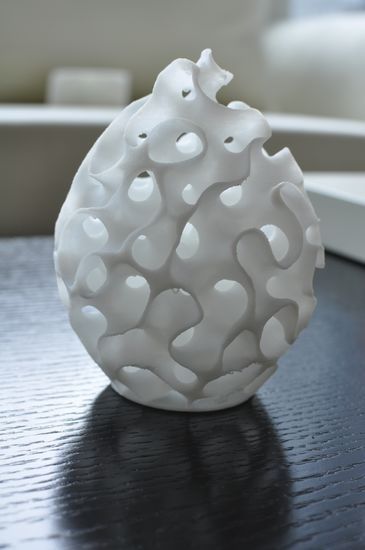
Most 3d printed objects need an internal structure that links perimeters and top/bottom layers. That’s why we set an infill pattern and percentage during slicing. Any type of structure can handle this, but each one has its own advantages and disadvantages. For example, the Lines Infill is faster but relatively weaker than the other patterns unless the forces applied to it are following the infill lines.
As the maker community tried out special designs, new ways to fill 3d printed parts were incorporated. In 2017, studies carried out on gyroid-type graphene structures revealed that this shape gave the pieces an exceptional resistance. When applied to 3d printing, this results in a structure that combines both stiffness and printing speed.
The Gyroid Infill is made with continuous curvilinear movements of the extruder. That results on a smooth movement and a highly constant filament deposition.
Its resistance is often compared to honeycomb’s, another infill pattern inspired by nature. The main difference between them is how they are built. Honeycomb, like most infills, repeats its shape in every layer. That forces you to set a higher infill percentage if you need to increase compression resistance on the Z-axis. When using gyroid, you distribute equally the object’s resistance for each axis, so the infill percentage is more efficient. In technical terms, the Gyroid Infill is close to being isotropic, which is one of its biggest advantages.
Another pattern that varies on each layer is the cubic infill. It forms small cubes as the extruder ascends during printing. This makes the object very resistant to compression forces coming from all directions. Regardless, the Gyroid Infill is also better in cases where your print requires shear resistance.
What is a gyroid
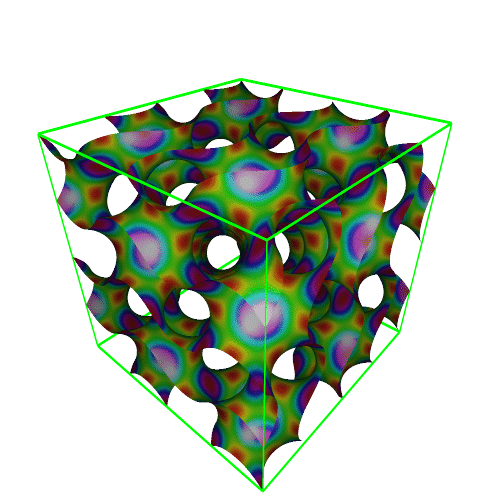
A gyroid is technically a Triply Periodic Minimal Surface (TPMS). These surfaces do not self-intersect, and because of this they form a “maze.” They can be subdivided up to a unit cell in three dimensions, so they can be replicated in a 3d printer.
In addition to its use in graphene structures, this pattern has applications in supercapacitors, solar cells, and nanoporous membranes. Similar patterns are seen on butterflies’ wings, which explains their lightweight and high resistance.
The most important property of the gyroid in relation to 3d printing is its cubic symmetry. This means that, although it is not totally true in the mathematical sense, we can consider it an isotropic structure. An isotropic object has the same resistance in any direction. Among the different infill patterns, gyroid is the most suitable for pieces that require sheer strength. It’s weight/strength ratio is much lower than most known patterns, so a piece with this infill can withstand greater loads using less material.
Properties of Gyroid infill
Since the Gyroid Infill began to be used, many users have put this structure to the test, to show if it really has superior properties to the honeycomb pattern, a structure based on hexagons.
I found an experiment1 that tested the resistance of different infills by applying a shear force to 3d printed bars. For this, three identical bars were printed, with different infill patterns: lines, honeycomb, and gyroid. The maximum weight supported by each bar was then recorded.
The conclusions of this experiment were as follows:
- The gyroid was the strongest structure overall when using the same infill percentage.
- The weight of the printed gyroid bar was almost 10% lighter than the honeycomb bar.
- The printing time of the gyroid bar was the shortest of the three.
The gyroid pattern is proven to be stronger and faster, and it uses less material than the others. If we don’t take perimeters into consideration, the gyroid’s weight is almost 30% lighter than honeycomb’s. So it saves money and time without major inconveniences.
Advantages of Gyroid Infill
Close to being isotropic:
An isotropic material maintains its properties in any direction. Although technically not true in the purest mathematical definition, the symmetry of the Gyroid Infill in all of the three axes helps to equalize its resistance in any direction.
Some patterns, such as lines, only have good strength if the forces are coming from the same direction as the infill. Others are good when compressed, but weak to shear stresses. The gyroid has very good resistance to any combination and direction of forces.
Overall very strong
The gyroid infill is so strong that it can even be printed without using perimeters. Some objects are designed by locating perimeters only in absolutely necessary parts. The other infill patterns need to “lean” on the perimeters, otherwise, their structure would collapses.
Shorter printing times
Given the same infill percentage, the gyroid prints 2% to 5% faster than the rectilinear pattern. When we talk about mass production, these values are significant.
Less material consumption
Another economic factor: with less filament a more resistant piece can be made. As it can be printed without walls while being functional, you could reduce its weight even more.
Good-looking infill
Although it is a matter of personal taste, the gyroid infill could be considered the most attractive of all currently available patterns. Many designers have modeled vases, glasses, or pots without perimeters, exposing the filling. The results are amazing as we will see later.
Dos not overlap on the same layer
The structure has no weak points since its lines are continuous along with the entire layer. This also reduces extrusion problems or nozzle clogging.
It is orientation independent
Sometimes you need to print the object with a specific orientation. That orientation might not be the same as the required to get the best resistance. With a gyroid infill, you can solve this issue, since it has the same resistance in any direction. This property might help reducing filament consumption, as you need fewer supports with a proper orientation of the object.
Allows you to consider using weaker materials
When we need a strong 3d printed object, we often think of ABS or Nylon as the obvious choice, as they are strong and resistant. But we could improve PLA resistance by using a gyroid infill, making the object cheaper and easier to print.
It does not need supports
Every TPMS is self-supporting in nature, making them perfect for FDM manufacturing.
It allows fluids trough itself
You could use this pattern for applications which require air or water flow, like electronic packaging or heat sinks.
Disadvantages of Gyroid Infill
Higher slicing times
Although this factor gets underestimated often, the slicing time can be excessive if we have to rely on a low-performance computer. The G-codes generated are usually bigger when using the gyroid. This can cause prints to fail when the printer is connected to the computer via USB.
Printer vibration can be quite high on higher infill percentages
Since the gyroid is formed by curves, the extruder has to move a lot in every direction. This produces unwanted vibrations that are transmitted to the object, especially at high speed. The solution is to reduce the infill percentage to achieve wider extruder movements and slow down infill speed. Remember that this pattern doesn’t need much infill to work well.
Gyroid infill slicer settings
The main advantage of the gyroid pattern is that it does not need a lot of infill percentage in order to be resistant: a small piece with 2 perimeters and 10% infill supports almost 10 kg. If you raise the percentage, the resistance will increase in a non-linear fashion. You can start with a 5% infill and increase it in cases where more resistance is needed.
Print speed may be slightly higher. Anyway, I recommend you continue using the same speed you have been using. Rest assured that by lowering the infill percentage and maintaining the movement speed, the printing time will still be reduced substantially.
If you do not find Gyroid in your slicer settings, download Cura’s latest version. This also applies to PrusaSlicer, Simplify3D, and other popular slicers.
Creative uses with Gyroid Infills
Due to the interesting shape of a gyroid, this pattern has caught the attention of both artists and makers. Let’s see how the properties of gyroid can be used to make complex and interesting parts:
3D Printable Gyroid by Dan O’Connell
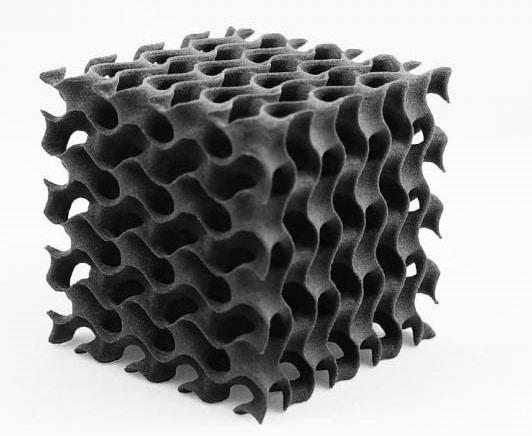
This design is simply a cube with no outer walls. With this piece we can test the resistance of the object, placing heavy objects on any of its faces. It also allows you to see how its “labyrinth” permits the water (or any fluid) to enter and exit completely, without stagnating in some internal nook. It is an ideal piece to show the gyroid structure to those who have never seen one.
3D Printable Gyroid Lamp by Greg
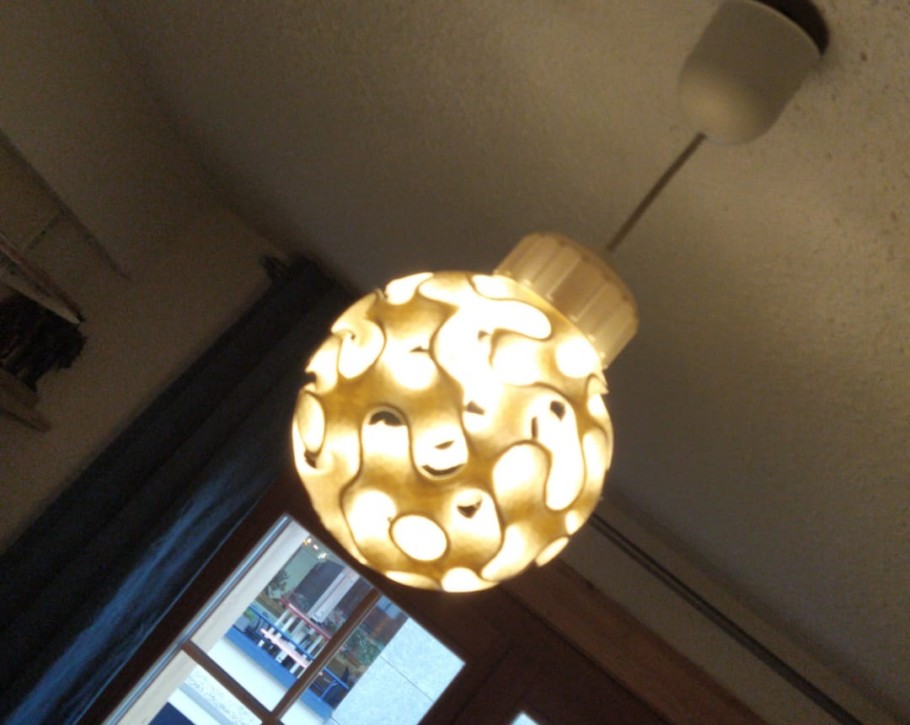
A spherical lamp with a gyroid pattern. As the gyroid is a surface (technically it is not a body) it allows the light of the lamp to pass through. In addition, its structural resistance protects the lamp from direct hits. It looks great when printed with translucent materials, like PETG.
3D Printable Gyroid Bookmark by PlasticPasta 3D
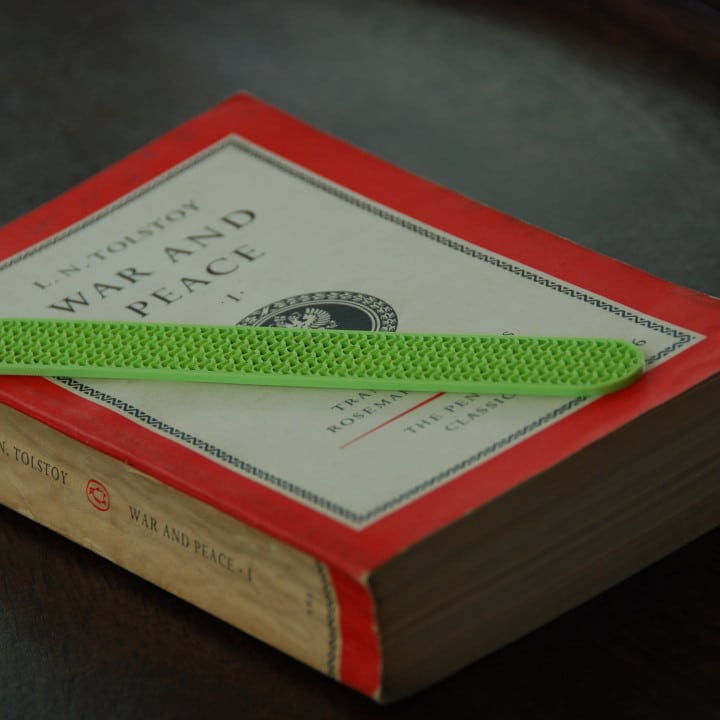
This design (a bookmark) combines the high strength of the gyroid with its structural beauty. It shows that this infill pattern can be used to enhance the aesthetics of familiar objects. On the other hand, books and nerdy things get along very well…
3D Printable Gyroid Shelf Bracket by Alexander
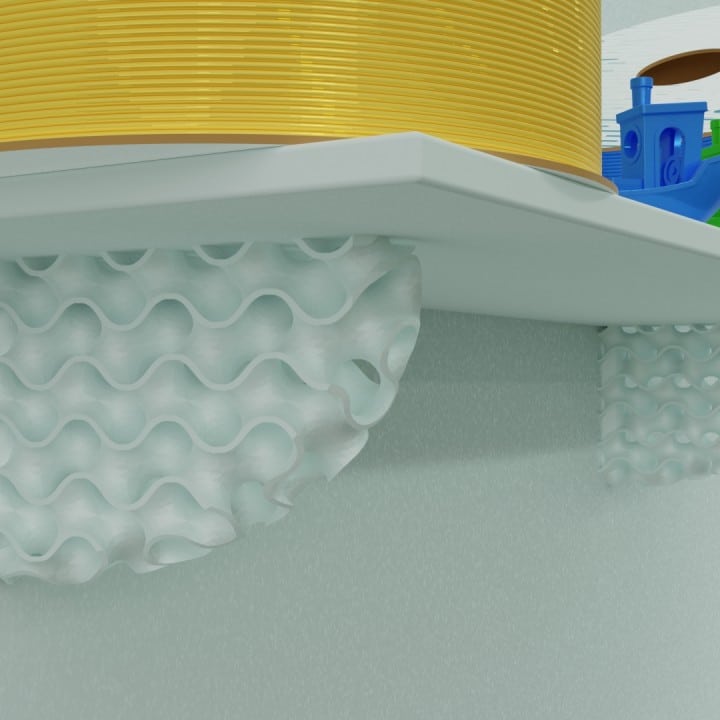
This shelf bracket was designed to support weights greater than 20 kg, using only 67 g of material! That is more than 20 books. It demonstrates that 3d printing still has things to say.
In addition, its “bone sponge” look looks great when printed in white…
Once you try the gyroid, there will be no going back. High strength, low weight, and shorter printing times, everything a maker wants!
Conclusion
Having gone through the technical details and the artistic applications of the Gyroid Infill, I hope that I could transmit at least a little bit of the amazement that I have for this pattern. Although I already use this pattern as my default infill, I’m still blown away by the way it looks and the properties it has. You should definitely consider start using it or at least giving it a try!
Check out our recommended products section
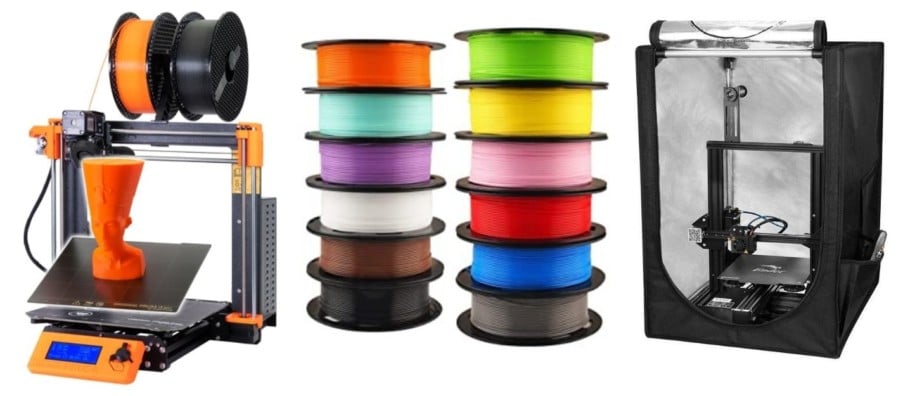
We created a recommended products section that will allow you to remove the guesswork and reduce the time spent researching what printer, filament, or upgrades to get, since we know that this can be a very daunting task and which generally leads to a lot of confusion.
We have selected just a handful of 3D printers that we consider to be good for beginners as well as intermediates, and even experts, making the decision easier, and the filaments, as well as the upgrades listed, were all tested by us and carefully selected, so you know that whichever one you choose will work as intended.
Error processing API data.
A great article. I have used Gyroid for rods printed vertically but as a 100% fill. I can see it is better at a much lower infill percentage. I will experiment.
Thank you.