Silicone is a versatile polymer with many practical applications. Advancements in 3D technology have made 3D printing with silicone possible through a variety of techniques. However, the practice remains expensive and inaccessible for some.
3D printers can print silicone. The process involves one of a few advanced printing techniques developed to work with Silicone. The Process differs from common 3D printing methods in a few key ways.
Keep reading to see details on how 3D printing with silicone works as well as some information on the pros and cons of 3d printing.
Can All 3D Printers Print Silicone?
Silicones are non-toxic, thermally stable polymers with qualities that make them useful for a wide range of applications. However, since they are resistant to heat, they cannot be printed through common 3D printing methods such as fused deposition modeling.
Not all 3D printers can print silicone. To print silicone, you need a specialized 3D printer that is capable of processing silicone materials. These printers also typically use a special type of silicone tailored to 3D printing.
The Difficulties of 3D Printing Silicone
The main difficulties with 3D printing silicone are availability and cost. Most common methods of 3D printing are not suited to processing silicone, so specialized hardware is required. Liquid silicone prior to being processed is highly viscous and needs to be “cured” before it will solidify. For this purpose, specialized 3D printing silicones are also necessary.
All of these factors make it difficult to access and purchase materials and hardware necessary for 3D printing silicone. However, there are some silicone 3D printing services available to consumers which I’ll talk about later in this article.
How 3D Printing Silicone Works
Processes for 3D printing with silicone have been independently developed by a number of manufacturers. The main processes are deposition and vat photopolymerization. I’ll talk a little more about the different processes in a moment, but for now, let’s focus on the basic process behind deposition printing with silicone.
How Silicon Deposition Printing Works
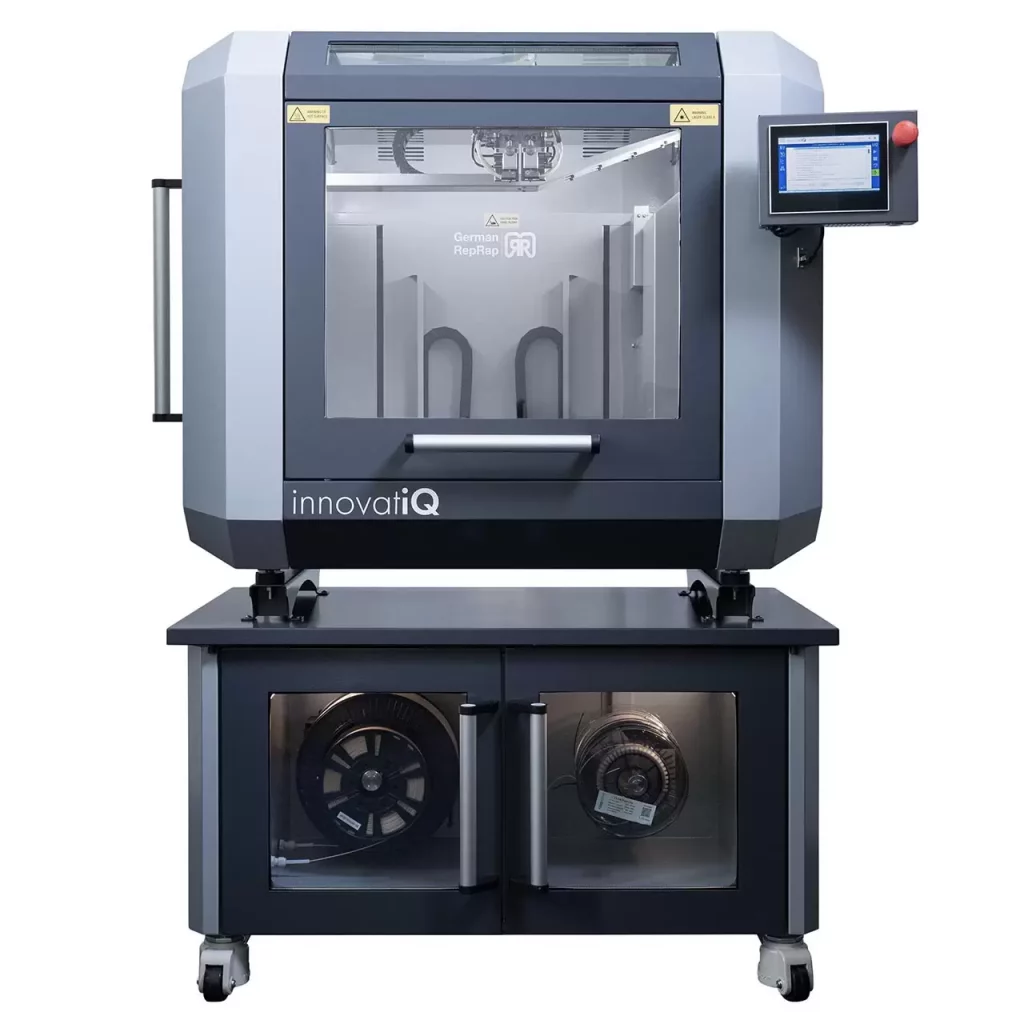
Deposition
Deposition printing with silicone involves the use of a specialized liquid silicone rubber. The liquid silicone rubber is extruded through a nozzle onto a surface and then cured with UV light before moving on to the next layer. Any support structures used are made from a water-soluble material so that they can be easily removed in post-processing.
Curing
Curing involves exposing the printed silicone layers to UV light in order to activate their binding agents. The layers fuse together into a solid surface as they are cured during the printing process. Each layer is cured after being completed and before the printer moves on to the next layer.
Post-Processing
Post-processing of a deposition printed silicone structure involves washing away any of the water-soluble materials used in support structures, as well as curing the surfaces again in order to make sure everything is solid. The finishing process for silicone 3D printing can be very time consuming, which is another reason silicone 3D printing can be inaccessible for general hobbyists.
Can You Use 3D Printing to Make Silicone Parts?
There are many applications for 3D printing with silicone. Silicone is heat resistant, nontoxic, electrically insulating, and has many other qualities that make it perfect for medical, dental, and industrial applications. Making parts for these applications from silicone is one of the main applications for silicone 3D printing.
You can use 3D printing to make parts from silicone. The process requires specialized materials and hardware. However, there are also silicone printing services available for consumers.
Silicone 3D printing has promising applications in medical, dental, electronics, and industrial fields. Components crafted with silicone 3D printing have all the advantages of silicone, along with all the advantages of 3D printing (such as streamlined prototyping and mass production).
Types of Silicone 3D Printers
As mentioned earlier, the main types of silicone 3D printers are deposition printers and vat photopolymerization. Deposition printing, as described above, involves printing liquid silicone rubber onto a flat surface. The printed layers are cured with UV light and then washed and re-cured during post-processing.
Vat photopolymerization involves dipping a printing surface into a vat. The machine then uses targeted UV light to cure silicone selectively, creating the solid layers of the object being printed. The surrounding liquid silicone remains unsolidified during the process.
Before additive manufacturing processes were pioneered for silicone-based printing, silicone was primarily used with injection molding to create silicone components. This process was quite limited compared to 3D printing, in that overly complex parts could not be reliably crafted with injection molding.
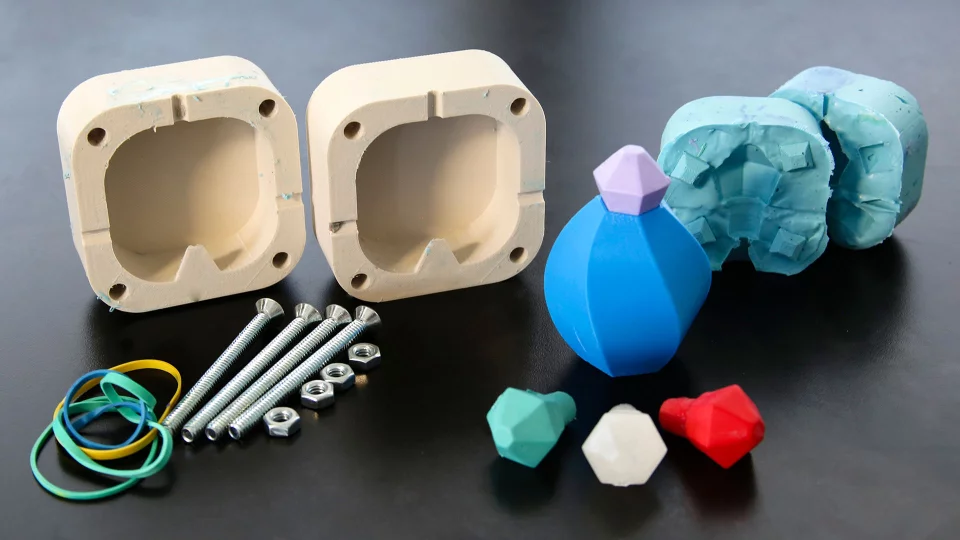
Pros & Cons of 3D Printing Silicone
Like any additive manufacturing process, there are advantages and disadvantages to 3D printing with silicone. Aside from the material advantages of silicone in general, 3D printing offers versatility and enables easy prototyping and development. The main disadvantages involved are availability and cost.
Pros:
- Silicone is non-toxic, heat resistant, electrically insulating, and biocompatible
- 3D printing allows users to easily print out prototyped parts and apply changes to the design as needed
Cons:
- 3D printing silicone requires specialized hardware and materials
- These things may not be available or affordable for everybody
- The process can be long compared to other forms of 3D printing
As 3D printing technology continues to progress, silicone printing should become more viable for consumer markets and hobbyists. As it stands, many of the parts and materials required for silicone printing are too expensive or unavailable to the public. For this reason, it is recommended to use a 3D printing service that deals with silicone.
Uses for Silicone 3D Printing
Silicone has many properties that make it suitable for a wide range of applications. It is heat resistant, highly flexible, electrically insulating, and biocompatible. This makes it quite attractive as a material for healthcare, dentistry, electronics, or industrial applications. 3D printing brings even more advantages to the table, since parts can be easily and quickly prototype, or mass-produced for industrial applications.
Healthcare
Silicone is biocompatible, meaning it is less likely that the human body will reject or react negatively to it. For this reason, it is frequently used for medical implants and other objects that replace or aid biological processes. 3D printing has the potential to streamline the manufacturing and customization of these types of applications.
Dentistry
Silicone is used in dental prosthetics, as well as in the manufacturing process for specialized dental devices like braces. Using silicone 3D printing, dental professionals could make a wide range of customized dental devices and models. The non-toxic and biocompatible nature of silicone makes it well suited to these applications.
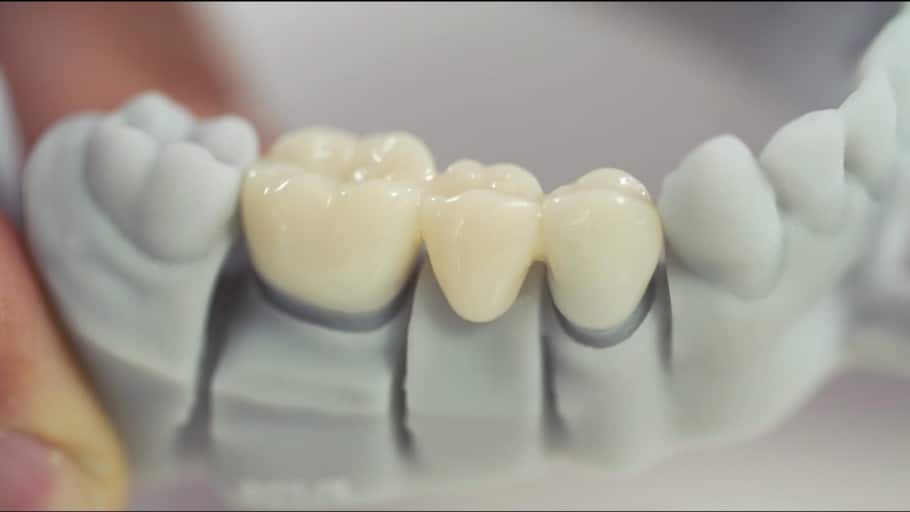
Electronics
Since silicone is electrically insulating, it works as an excellent casing or coating for electronic devices and components. Its heat resistance and resistance to high pressure also make it well suited to protecting electronic components from outside forces. 3D printing with silicone could streamline this process and create silicone components with more complexity than what is possible with injection molding.
Industrial
Being heat resistant, resistant to pressure, and watertight, silicone is well suited to a number of industrial applications. A good example would be gaskets for parts that need to resist water and air pressure. Industrial applications typically require large amounts of standardized parts, which makes 3D printing a good solution to quickly and effectively manufacturing silicone parts for industrial applications.
Silicone 3D Printing Services
As mentioned above, there are a number of services available for people who want to have a silicone object 3D printed, but don’t have the time, money, or expertise to do it themselves. Since the specialized hardware and materials used for silicon 3D printing are quite expensive and hard to find, 3D printing services are a good way to have access to silicone 3D printing.
ACEO
ACEO is a German company that pioneered some of the first 3D printing methods for silicone. They can print silicone objects up to 200cm3, and can provide you with a finished product in as little as ten days. They specialize in creating silicone prototypes and components for many different applications, and use their own patented technologies when printing silicone.
Carbon3D
Carbon3D is a US-based company that creates sporting goods from silicone using their patented Digital Light Synthesis system. They mainly print wearable silicone components such as watchbands. They offer a digital manufacturing process for use by businesses that need parts in a variety of materials, including silicone.
EnvisionTec
EnvisionTec uses printers that are similar to those used by ACEO. They create medical-grade objects used in implants and other medical applications. They also work with a wide range of other proprietary biocompatible materials.
German RepRap
A company based in Germany that uses chemicals developed by Dow in a proprietary deposition printing process. They mostly print parts for aerospace and automotive applications, working with silicone and other materials such as polyurethane.
Spectroplast
Spectroplast is a Swiss company that also specializes in manufacturing biocompatible parts for medical applications. They use a vat polymerization process and can deliver finished products in as little as seven days.
Check out our recommended products section
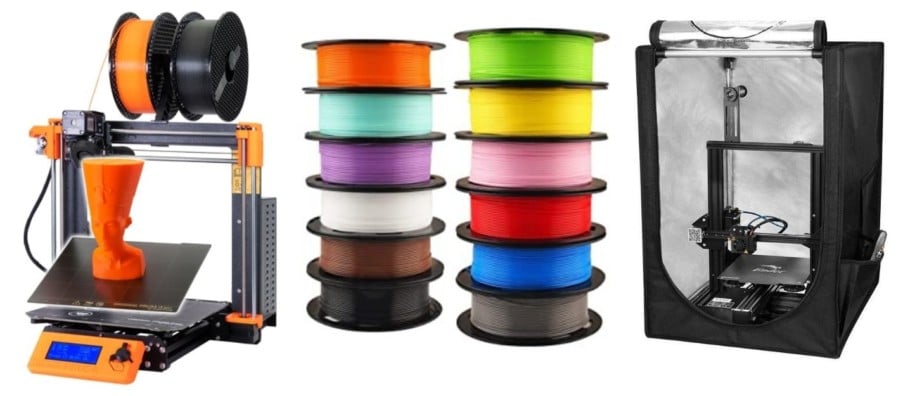
We created a recommended products section that will allow you to remove the guesswork and reduce the time spent researching what printer, filament, or upgrades to get, since we know that this can be a very daunting task and which generally leads to a lot of confusion.
We have selected just a handful of 3D printers that we consider to be good for beginners as well as intermediates, and even experts, making the decision easier, and the filaments, as well as the upgrades listed, were all tested by us and carefully selected, so you know that whichever one you choose will work as intended.
Error processing API data.