Both novice and experienced 3D printing enthusiasts have to deal with printing issues on a regular basis in order to finally achieve rewarding and good-looking prints. The main difference between both type of users is that the experienced ones typically can look at a print and quickly troubleshoot and determine what went wrong and what should be changed in order to solve it. As we will find out in this article, knowing the root cause of an issue is the hardest and most important step.
Let cut right to the chase and find out how we can solve over extrusion (curling) on the corners!
In order to fix over extrusion or curling on the corners, it is recommended to lower the extrusion temperature, turn on the layer fan to its maximum capacity and increase the time minimum time per layer to around 15 seconds, thus reducing movement speed on smaller layers. Curling on the corners is commonly mistaken with over extrusion, but in contrast to that problem, the issue only occurs on the corners of the object instead and not on the entirety of the outer shell.
By differentiating both issues, it is possible to isolate the problem and determine that the cause of curling on the corners is not caused by over extrusion but by slow cooling down of the deposited thermoplastic.
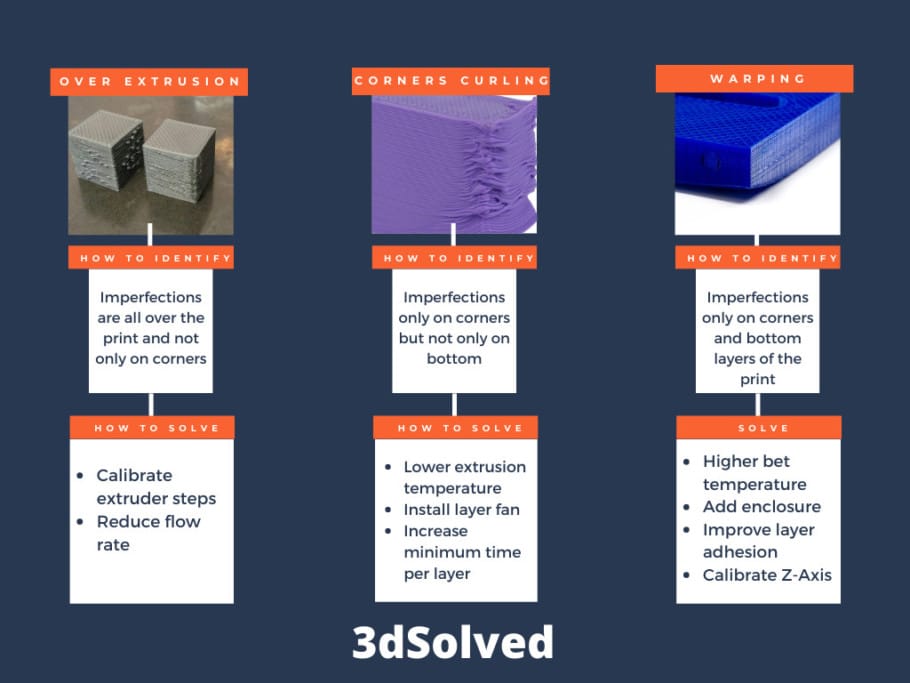
Due to the nature of this problem, it is very easy to wrongly determine the cause of the issue. This is why I will try to help you differentiate curling on the corners from general over extrusion, and also from warping on the first few layers. Let’s get started!
Curling only on corners versus over extrusion everywhere
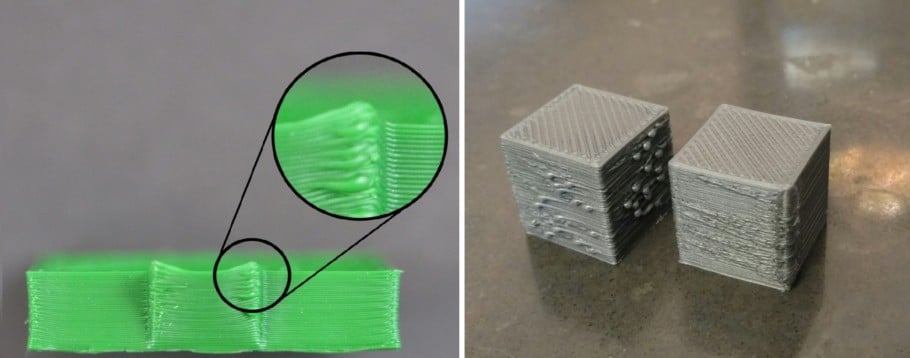
On the right: Overextrusion (Source)
The problem of curling in the corners is often associated with over extrusion, although this is not always the cause. Many people try to fix this by modifying the flow parameters, making the printer extrude less material, but while this can sometimes help, it doesn’t eliminate curling entirely.
One way to differentiate in which cases the curling is produced by over extrusion is verifying the size and shape of the vertical walls of the object. When the extruder provides more material than necessary, this defect can be observed throughout the part, not only in the corners.
Now that we know how to differentiate both issues, let’s focus on curling. The biggest difference is that overextrusion occurs throughout the piece, while curling occurs in areas where the object needs a greater supply of material, such as a sharp corner.
Curling consists of a lifting of the last printed layer, which occurs in certain sharp areas. It happens because the material contracts when it cools down, and the areas where there is more material drag the corners in, causing them to rise.
The problem gradually increases on each layer when the extruder passes through the raised area again, since the contact of the hotend with the bent corner produces undesirable deformations in the perimeters of the part.
Worst of all, if the plastic curled and cooled down before the next layer, the nozzle could hit that corner and unstick the entire part. Also, the stepper motor could lose steps and displace the next layers of the print. There is no way to fix this problem since 3d printers don’t have a closed-loop control system.
Curling on corners vs warping
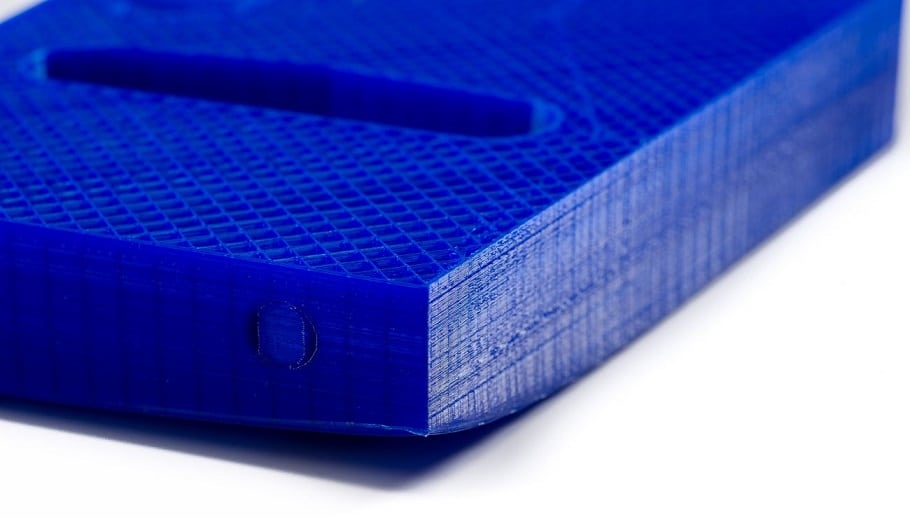
It is easy to confuse curling with warping, and although they have points in common, their causes and ways of solving them are different.
Warping only occurs at the base of the part, because it is a problem of adhesion to the heated bed. It is similar to curling because both happen in corners, and the sharper they are, the more noticeable this defect will be.
The chances of the part coming off the bed are much higher when warping occurs and starts lifting one of the object’s corners. The solution to warping is rather straightforward: raise the temperature of the heated bed, or enclose your 3d printer. Cold air currents are also very harmful and lead to warping issues.
Curling, on the other hand, also occurs in the upper layers, so the temperature of the heated bed has little or no influence on this problem. In order to fix it, you’ll have to consider other things, such as lowering nozzle temperature, installing a layer fan, or reducing printing speed.
How to fix curling on corners
We could say that curling is mainly produced by excessive extrusion temperatures of the filament. As the material comes out of the nozzle very hot, it stays limp for a longer time. This excessive time, combined with the shrinkage of the material, causes the corners to lift up.
For this reason, we will focus on the temperature parameters of the hotend in order to solve it definitively. To prevent curling, we are going to modify the following parameters on our slicer software:
Nozzle temperature
Many times, when we have problems with jams or underextrusion, some people recommend raising the printing temperature. This action sometimes improves our prints but does not solve the original problem. Although the filament flows better, the extruder may have another problem and we´re only hiding the problem under a rug by raising the temperature.
In the long run, raising the printing temperature too much comes along with other defects such as curling or burning the inner PTFE tube. To avoid this, we will try to use the lowest possible temperature, and thus give less time for the material to shrink. This test will help assist us in determining the optimal temperature of our printer for a specific filament type.
Another way to know if you are setting too high of a temperature when printing with PLA is paying attention to your prints’ brightness. The object gets brighter as the temperature is higher. Reduce it if the piece looks too shiny.
Cooling
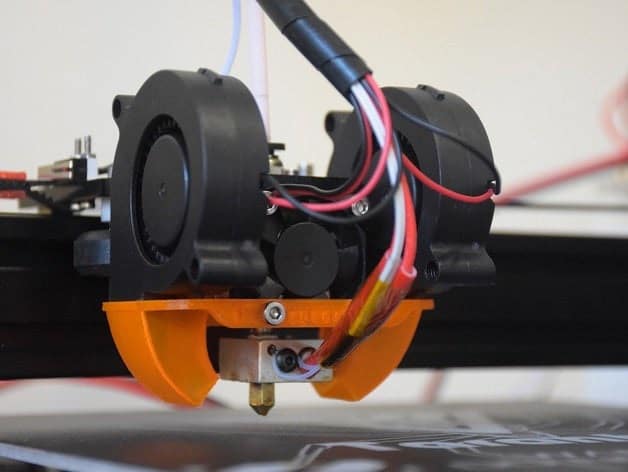
If your printer doesn’t have a layer fan installed, it’s time to install one. This fan dramatically decreases material cooldown times, preventing corners from having time to bend up. You just have to be careful not to activate it during the first layers, as it could lead to warping.
These fans can change their speed during printing, as they are controlled by PWM (pulse with modulation). This feature allows you to turn them on whenever you need, and at a precise speed.
One of the things to keep in mind when using a layer fan is its orientation. It may be incorrectly positioned, which would cool down the nozzle, causing temperature errors and printing stops.
It may also happen that, due to the orientation of the object, the layer fan only cools down one side of the object. You can tell if this is the case when the curling always occurs on the opposite side of the layer fan. There are radial ducts that blow air evenly in all directions. On the off chance that you own a GeeTech i3 Pro B, you should definitely print and install this Air Duct. Here is another one that is compatible with the Tevo Tarantula
Printing speed
In some small pieces, a new layer might start printing on top of one that is still hot, so it never fully solidifies. To help prevent this, slicers come with an option to determine the minimum time it should take to produce each layer. By doing so, the printing speed is decreased during smaller layers. A typical value is about 15 seconds per layer.
If you still have issues related to curling, lower the printing speed by 10 mm/s until you get better results.
How to fix over extrusion
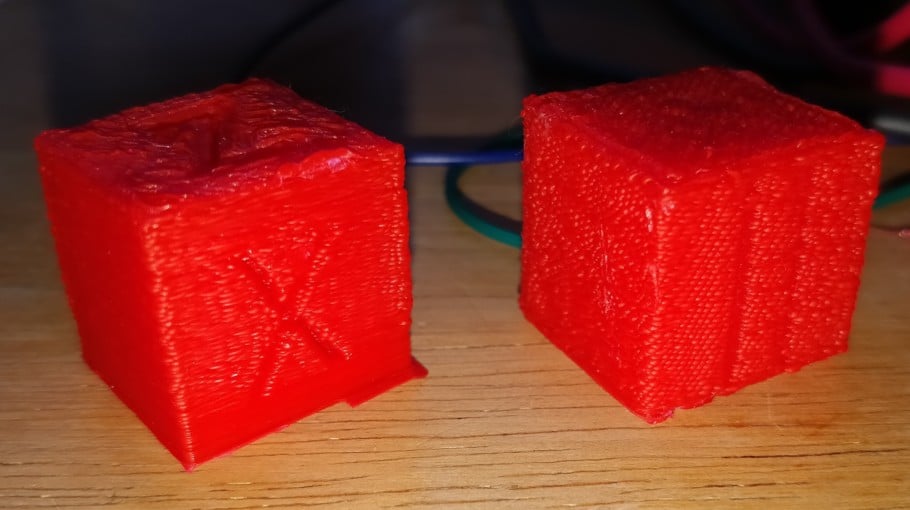
If the walls look “squirted”, as if the material is falling out of the object, then you will most likely have to set the extrusion parameters correctly.
This configuration mainly includes calibrating the extruder steps, so that the exact amount of material required is provided. The procedure is very simple, and there are several tutorials on the web on how to do it.
One easy test you can do consists of drawing marks along the filament before it gets extruded. The hotend is then heated and the 3d printer is commanded to extrude 10 cm of material. If the steps are correct, the next mark drawn on the filament should be located exactly at the entrance of the extruder (at the same point the previous mark was located).
If this mark ends up inside the extruder, it means that the printer thinks it is extruding 10 cm but is actually extruding more material (over extrusion). When this happens, the excess material deposited will squash against the previous layer and drip down to the sides of the object’s outer shell, leaving an unsightly finish.
Another parameter to check, after calibrating the extruder steps, is the flow rate. This allows you to multiply or reduce the volume of filament supplied. It is a more direct way of controlling the flow provided by the extruder, depending on the different densities of each material. Unlike step calibration, this parameter is variable. It is not the same to use ABS, PLA or TPU in your printer, so it is advisable to vary the flow rate according to the material used. You can use this test to quickly adjust the flow rate.
It contains instructions for performing the test using a caliper or micrometer. Be sure to read them before starting the test.
Do these problems affect all filament types equally?
There is a property that is common to all materials used in 3d printing: they expand when heated and contract when cooled. So technically any filament can present warping or curling problems. The difference is that not all materials expand and contract at the same rate or at the same speed.
PLA is the most widely used material nowadays because, in addition to being cheap, its shrinkage ratio is one of the lowest, making it is easier to print in broader conditions than most filaments. PETG also features a low shrinkage ratio, but it needs a heated bed to be printed.
Other plastics (like nylon or ABS) shrink a lot, so the use of an enclosed printer is practically mandatory if you want to get acceptable results.
Why does ABS need a heated bed?
ABS is a thermoplastic that definitely shrinks a lot when it cools down. Without the presence of a heated bed to keep the first layers warm at 90°C, the difference in temperatures along the piece will lead to a contraction that lifts up the corners of the piece.
ABS warping is very common and difficult to eliminate. You can minimize the risk by properly leveling your bed and enclosing your printer. Additionally, when ABS curls and cools down, it becomes harder than PLA, increasing the risk of losing the entire print if the nozzle hits the object.
Keep in mind that, unless there is a technical aspect that requires the print to be produced in ABS, most of your problems can automagically disappear by switching to PLA!
Check out our recommended products section
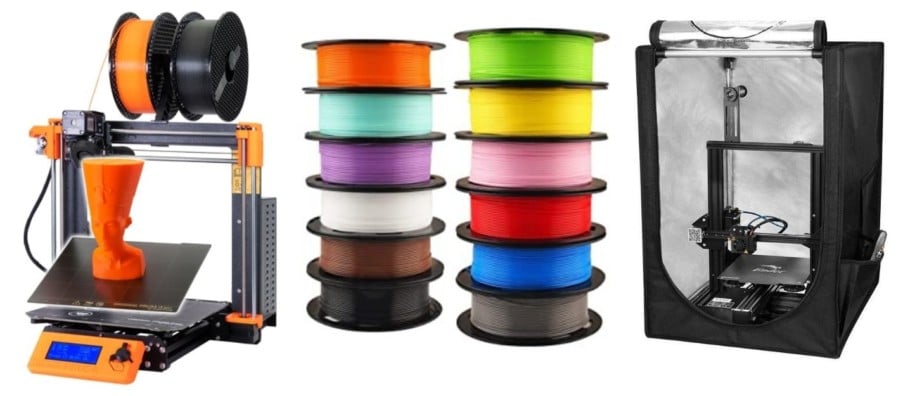
We created a recommended products section that will allow you to remove the guesswork and reduce the time spent researching what printer, filament, or upgrades to get, since we know that this can be a very daunting task and which generally leads to a lot of confusion.
We have selected just a handful of 3D printers that we consider to be good for beginners as well as intermediates, and even experts, making the decision easier, and the filaments, as well as the upgrades listed, were all tested by us and carefully selected, so you know that whichever one you choose will work as intended.
Error processing API data.