Working on some 3D printed pieces, you could face the challenge of having to reinforce them totally or locally in order to improve their strength and durability. It could be a whole part or a specific area subjected to some kind of load, such as compression, tension, shear, torsion, or bending.
In this article, we will be exploring many methods with which you will obtain stronger prints, such as improving the strength in the designing phase, controlling printing temperature, and speed, or choosing the most suitable material for your print. But before doing so, lets do a quick summary of the things you can do in order to make your 3d prints stronger.
In order to make 3d printed parts stronger, it’s important to decide the proper print orientation, increase the wall thickness, and infill density. Additionally, it is also possible to increase the resistance by adjusting the flow rate, reducing the printing speed, increasing the line width, increasing the printing temperature, and even turning off the cooling fans. Last but not least, consider printing with Nylon and annealing the object.
Let’s get started!
Start with the Design
In this section, we are going to point out the importance of the design prior to printing and how it can be used in our favor.
By performing stress analysis on the part, we will be able to identify high-stress areas. Thus reinforcing the part locally and making modifications to those areas will provide maximum strength to weight ratio, will reduce filament consumption, and minimize print times.
The first thing you can do is to modify the infill density by increasing it just in high-stress areas.
Working on these specific areas, you can also modify the perimeters by increasing the number of them to the desired thickness.
Internal strengthening of the piece is also possible. If you model an internal hole in a high-stress area, the slicing software will treat the hole as a part feature. Therefore, it will print it with perimeters, creating an internal structure in the form of a small tube resulting in a better distribution of the loads in that area.
Slicer Settings that affect a print’s strength
A slicer is computer software, which plays an important part in the 3D printing process since it’s the one in charge of converting a model in STL format into printer commands in g-code format.
Within these commands, you can set features such as printing orientation and temperature or infill pattern and density, which can affect print quality and strength.
Print Orientation
Layer orientation determines how strong the print is by a lot.
It is important to know that the interface between layers is a weak point, which means, that if you apply a force at this point directly in the direction where the layers are orientated then you will probably break the piece with almost no effort. Then when positioning your design within the slicer you should take into account the loads to which the part will be subjected, and ensure that the printing plane is not located parallel to those forces.
If you want to see an example of this, you will find more information in this article.
Wall Thickness (number of shells/perimeters)
Shells or perimeters (the name depends on the slicer software you are using), makes up the exterior of 3D printed parts. As we know, the machine prints it in a completely different way than the interior of the piece.
Many different settings affect how shells/perimeters are printed and some of them are directly related to the strength of the piece. An example of this is wall thickness.
Slicer setting for shell thickness is commonly divided into wall thickness and top and bottom layer thickness. You can set either the wall width (in mm), which determines the width of the set of walls on a print or the desired number of passes the nozzle should take for the walls. These parameters are correlated: adjusting one will automatically adjust the other.
Settings are almost the same for the top and bottom layers. The thickness refers to the height of the layers. For stronger parts, you should use larger values such as a wall thickness between 2 and 3 mm and a top and bottom thickness between 1.6 and 2 mm.
Infill Pattern
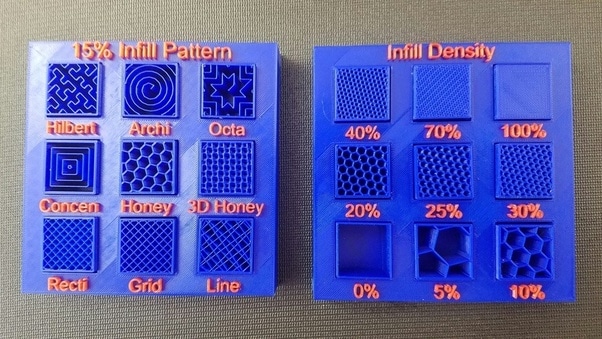
Many different infill patterns are available in the settings.
If the goal is to get a stronger piece, infill patterns like cubic, cubic subdivision, octet, quarter cubic, and gyroid, will be preferable over patterns like Lines or Zig-Zag which represent lower strength infill.
However, when choosing one or another you might take into account the type of load the part will be subjected to, the direction in which they are applied, and the amount of material and printing time each pattern spends.
Despite each piece involving a separate analysis, in general, a honeycomb with an infill of about 50% density is the strongest option.
For an extensive article about infill click here
Infill Density
Besides the pattern, density is another infill feature that will affect the strength of your pieces. The denser de infill, the stronger the piece. This is because there is more material bearing the loads and you get a better distribution of them.
However, not always a 100% density is the best option. Depending on the features you want for the parts, you should consider that this will increase as well printing time, filament consumption, and you will obtain heavier pieces too.
What is a good infill density?
In general, setting infill density above 75% will not increase significantly parts strength. An infill percentage of 50% may already give you the same strength as 100%, or very close to it, in some cases.
Reduce the Layer Height
Layer height is the height of each layer of extruded plastic on a 3D print. This parameter is related to the level of detail or resolution we will obtain in the final result.
A study was conducted to determine how different layer heights and nozzle diameters would affect print strength. They tested 0.4mm, 0.6mm, and 0.8mm nozzles and varying layer heights and got to the conclusion that the more you increase the layer height the weaker the part becomes, in fact, from minimum to maximum layer height there was a strength difference of about 3.5 times.
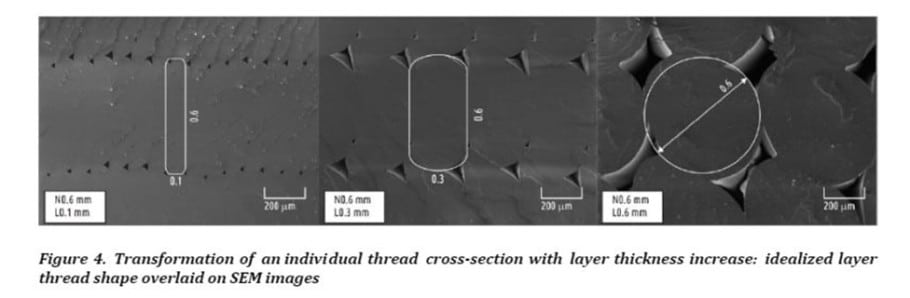
As you can see in this image, nozzle diameter plays a major role since printing with a larger-diameter nozzle but at a low layer height will provide a wider contact surface area for each layer to adhere to the previous one, resulting in an overall stronger bond and therefore, a stronger 3D print.
Increase the Line Width
The line width is how wide the line of the material that is printed is. With higher extrusion widths, the pressure inside of the nozzle needs to be higher as well to squeeze the material to the sides after it leaves the nozzle.
This pressure will not only squeeze the material to de sides but will also press the layers together causing a better adhesion between them. Line width values can be expressed in terms of the percentage of a 0.4mm nozzle.
It can be observed that layer adhesion and strength reach their maximum at 150%. After this value, they start to decrease because it is obtained on very rough and stressed surfaces.
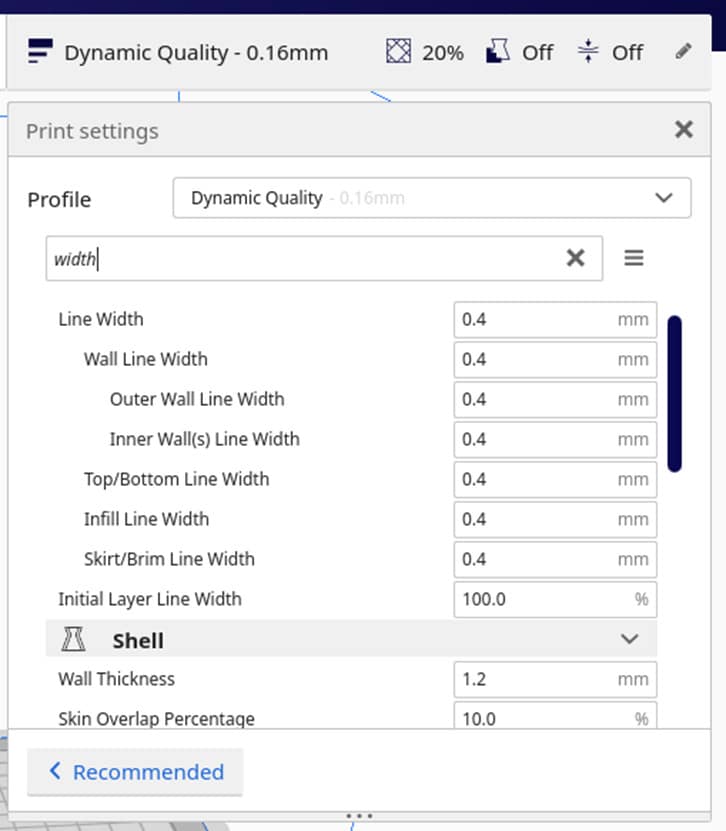
Adjust the Flow Rate
A cause of weak pieces can be under-extrusion because of the gaps, missing layers, or little holes it may appear in a print. This issue can be related to an inadequate flow rate. To increase gradually this setting until seeing some improvement might solve the problem.
You could face the opposite problem too; it means over-extrusion. In this case, the solution could be to decrease flow gradually until you see some improvement. Layer delamination is another way of losing strength in a piece. Same as before increasing flow might be the solution.
Reduce the Printing Speed
Depending on the ability of the machine to handle a given speed, the quality of the piece will be affected to a greater or lesser extent.
Fast movements from the extruder generate a significant amount of vibrations and the results are poor quality prints. Therefore, in some cases reducing printing speed could be a good solution.
Increase the Printing Temperature
Higher temperatures mean better adhesion between layers.
At the same time, because very low temperatures are likely to cause under-extrusion, pieces printed at higher temperatures tend to be heavier for containing a larger amount of material. More material usually means more strength.
Nevertheless, you should be careful thinking that extremely high temperatures are the best in order to improve strength. You could obtain quite stringy parts even with voids and bubbles in them, and cause degradation of the material making the piece weaker.
Turn off the cooling fan
A cooling fan’s job is to cool the material once it came out so it solidifies quickly and the piece does not get deformed while it’s being printed. But be careful because if you cool it too much you might have problems with the adhesion between layers and they could split apart.
On the other hand, there are some potential issues of doing this such as poor bridging or overheating which leads to the deformation of the final piece.
Ideal Slicer Settings for Stronger Prints
Here goes a table with the ideal settings for PLA filament:
Parameter | Setting |
Printing temperature | 200–210ºC |
Bed temperature | 50 – 65ºC |
Layer height | 0.12 mm (lower is better) |
Retraction | 6 mm |
Infill | 50% or higher |
Speed | 30 – 50 mm/s |
Initial layer speed | 20 mm/s |
Initial layer height | 0.2 mm |
Initial fan speed | 0% |
Fan speed | 0% for stronger prints |
Support overhang angle | 45° |
For other common materials, ideal printing temperatures are:
- ABS: 230 – 240 ºC
- PETG: 220 – 230 ºC
- TPU: 220 – 240 ºC
Ideal Bed temperature:
- ABS: 90 – 110 ºC
- PETG: 70 – 85 ºC
- TPU: 50 – 65 ºC
Use Stronger filament
The material we use has direct consequences in terms of strength and durability. In terms of strength, the winner seems to be polycarbonate, which is rated as the strongest filament type. When printed correctly and at the right temperatures, polycarbonate can produce extremely strong and long-lasting components.
Then we have nylon, which can be compared with polycarbonate. This material is impact, fatigue and heat resistant, and has the advantage of being easier to print than polycarbonate.
PLA and PETG are other common materials, which have the advantage of being easier to print than polycarbonate for example. PLA is often recommended as a starting material for beginners. PLA is stiffer while PETG is more flexible, making it harder to break since it will bend more.
This characteristic makes PETG also more impact-resistant than PLA because it absorbs impact better. On the other hand, PLA is stronger in terms of tensile strength.
The following table shows impact strength for different materials at different orientations (Joules/Meter):
Flat | Horizontal | Vertical | |
Polycarbonate | 354 | 515 | 42 |
Nylon | 325 | 249 | 60 |
PETG | 239 | 178 | 35 |
PLA | 153 | 113 | 77 |
ABS | 129 | 149 | 55 |
For a detailed comparison between PLA and PETG check here.
Which filament resists the outdoors?
There are some desirable features for a material to be resistant to the outdoors, such as UV light, temperature and water resistance.
But, which are the most recommendable materials for outdoor applications?
PETG, has UV light resistance as well as water resistance which makes it a good option to be used outdoors.
ASA, is UV resistant and can withstand all weather conditions. It has a high glass transition temperature, resulting in high-temperature resistance and impact and chemical resistance.
On the other hand, nylon, PLA, and HIPS, are not recommended in outdoors applications since their lack of UV light resistance. They will lose color and get brittle with time.
You can find extensive information about this subject here.
Which filament resists heat the best?
Temperature resistance is the highest temperature that a print can withstand before it melts or crack.
Polycarbonate is known for its strength, and durability, and has high heat resistance. The glass transition temperature of polycarbonate is 150°C, and prints can withstand heat up to about 140°C.
Another popular filament is ABS which has high heat and damage resistance. The glass transition temperature is 105°C and finished prints can withstand temperatures close to 100°C but not for prolonged periods of time.
PETG filament has good qualities relating to heat resistance too and it is very easy to print as well. PETG is able to withstand temperatures of up to 75°C.
More information about filament’s heat resistance here.
Anneal the print
Annealing helps to increase the part’s strength and durability. This process causes an increase in the number of large crystal structures in the plastic. This helps redistribute loads and heat energy more evenly.
The process consists in exposing the part to a very specific temperature: above the glass transition temperature but below its melting temperature, for about 30 to 45 minutes.
For further information, check this article .
Conclusion
As we have seen, there are many things to do in order to get high-quality and strong pieces.
You will usually have to resort to some of them altogether.
Starting at the design phase by performing a stress analysis of the part, following with proper slicer settings, and choosing the most suitable material for the work you will be able to obtain high strength and durable pieces.
Error processing API data.