Polycarbonate (PC) is a high temperature plastic that is widely used for its strength and other mechanical properties. Each manufacturer has its own blend that may result in different printing temperatures and strength so you must be aware that you may get very different results from different brands. Some even have blends with other thermoplastics but usually the requirements are similar and must be printed from 260°C up to 315°C.
The stock Ender 3 isn’t prepared to handle the temperatures needed to successfully print PC. Attempting to do so may damage the machine permanently and pose serious health risks.
It is possible to print Polycarbonate on an Ender 3 but not without some upgrades. Hotend must be all-metal, the temperature sensor must be prepared for high temperatures and some firmware maximum temperatures must be modified. You should consider also adding an enclosure and a drybox.
If you don’t want to have to go through all the trial and error that we did in order to find the Ideal Settings for creating high-quality prints on your Ender 3, then definitely check out our own Cura Profiles tailored specifically for the Ender 3 Printer Series.
What upgrades are needed to print Polycarbonate on an Ender 3?
It’s worth noting that all the upgrades I’m listing here are also necessary for printing Nylon, since these are fairly similar filaments, at least as far as printing goes. Basically, upgrading the printer to be able to print with one means that you will be able to print with both.
Here’s a list with all the upgrades and where you can get them (you also need to do some tuning, etc., and you will be able to find all of this later in the post):
- All-Metal Hot End (I recommend MicroSwiss): Amazon.
- High-Temperature Thermistor: Amazon.
- Garolite Print Surface: 3Dmakerengineering.com
- Improved Bed Adhesion: Gluesticks and Harspray.
- Enclosure (Prevents warping): Amazon.
- Filament Dryer Box (you can make your own): Amazon.
All-Metal Hot End
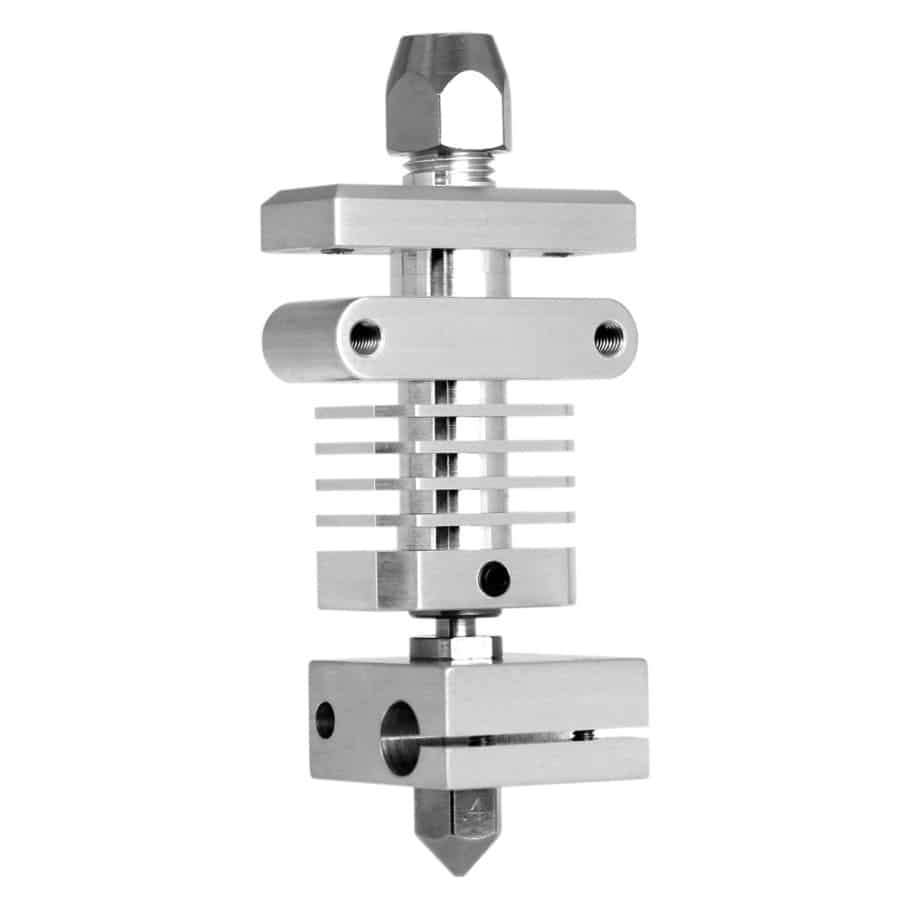
The stock setup comes with a PTFE Bowden tube that extends far into the hotend touching the nozzle. As PTFE has a low friction coefficient, this is a cheap way to prevent molten plastic from sticking to the walls and prevent clogging of the hotend. The downside is that the tube can sometimes leave a gap where the plastic can create a plug and jam the filament.
At 260°C PTFE starts to breakdown and outgas nasty chemicals that pose serious health risks. A solution to this problem is to use an all-metal hotend. This means that now the Bowden tube only goes up to the heatsink of the hotend where temperatures are safely within the PTFE’s working range.
There is a wide variety of all-metal hotends to choose from, but you should consider a few things when buying one. You will probably find some really cheap ones, but they usually come with no documentation or instructions for assembly and mounting and you may encounter many problems if you don’t know what you are doing. Build quality is really important, especially interior surface finish. Poor machining can lead to clogs and a difficult printing experience. Big brands are usually more expensive, but they focus on quality and making better products, some even have special coatings that reduce friction inside that improve reliability and ease of use.
Things to watch out for:
- Mounting should be compatible with your setup.
- Make sure you are really buying an all-metal hotend because some sellers will market their products as “all-metal” but will use PTFE liners inside to cut costs.
- If you can spend a little more, I usually recommend buying hotends from known brands such as E3d, Microswiss or Slice Engineering. Better surface finish will let you print with less clogging.
Temperature sensor
The stock thermistor isn’t able to accurately measure the high temperatures needed for printing polycarbonate.
There are three main options; a high temperature thermistor (simplest and cheapest solution), a K-type thermocouple with a breakout board, and a PT1000 thermal resistance. Connecting the thermocouple to the stock motherboard is not possible so if you want to go down that route you should upgrade to a board with more IO pins.
The easiest way is to upgrade the thermistor. The new one will have the same two wires to route and hook up so only a firmware change will be necessary apart from the physical installation.
Firmware Update
Updates in hotend and temperature sensors need a few changes in firmware in order to work properly. First you will need to change the maximum temperature limit of the hotend to above 315°C depending on the setup you have. Stock firmware caps the temperature to prevent the PTFE tube from burning. After eliminating this risk by upgrading to an all-metal hotend, the limit can be changed to a higher number.
Be aware of the limitations of the temperature sensor or other components when choosing the new maximum temperature limit.
Another change you must make is to adjust the temperature sensor setting. Each temperature sensor has its own constants that determine the correct reading. You may need some experience and knowledge to do this depending on the board and firmware you are running. Configuration files usually have presets for the most common sensors.
Picking one from the preset list on your firmware sill save you a lot of trouble especially if you are new to the subject.
PID tuning
The printer controls the temperature of the hotend with an algorithm that is called PID or Proportional-Integral-Derivative control. Three values must be chosen, each of them makes the system respond in a different way. Luckily most firmware can calibrate these values with automatic PID tuning.
The system runs a series of heating and cooling cycles at a set temperature to determine Kp, Ki and Kd. The temperature in which the automatic PID tuning runs will be the one for which the machine will have the most accurate control.
This should be performed whenever there is a hardware change in the system such as a change in hotend or an enclosure. The stock firmware is calibrated around 210°C for the stock hotend, so the printer won’t be able to truly control the temperature for the new hotend at 300°C until you run the cycle and set the parameters.
Printing surface and glues
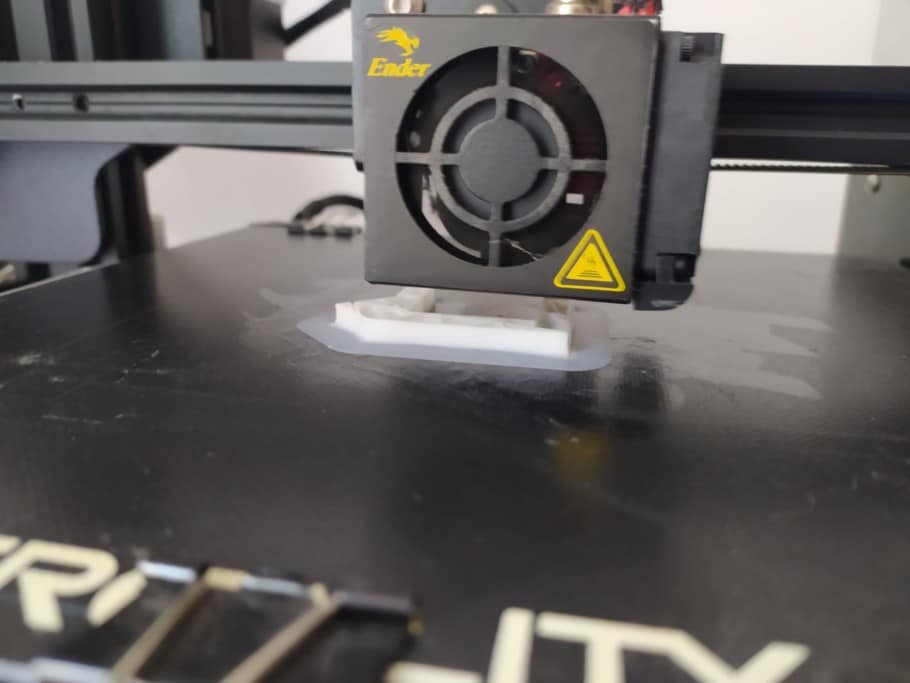
Bed adhesion is especially important when printing with PC. Using PVA glue, hairspray and other glues designed specifically for bed adhesion are a must not only to get a good adhesion but to use as a separation layer to release the part after printing. PEI sheets can be damaged if no separation layer is used.
A good recommendation is to use Garolite as a print surface. It is composed by a series of layers of fiberglass cloth in resin. You can attach a sheet with clips over the stock bed. While the surface will degrade a little with each print, you get two sides per sheet. Others have reported to have succeeded with polycarbonate sheets as a print bed. Be sure to use some kind of separation layer because otherwise you will end up with the piece solidly fused to the bed.
First layer calibration must be perfect to print with PC. Make sure you master other simple filaments such as PLA before getting into printing with polycarbonate.
It is also advisable to use an automatic bed leveling system, such as a BLTouch, to ensure that the first layer always comes out perfect!
Enclosure
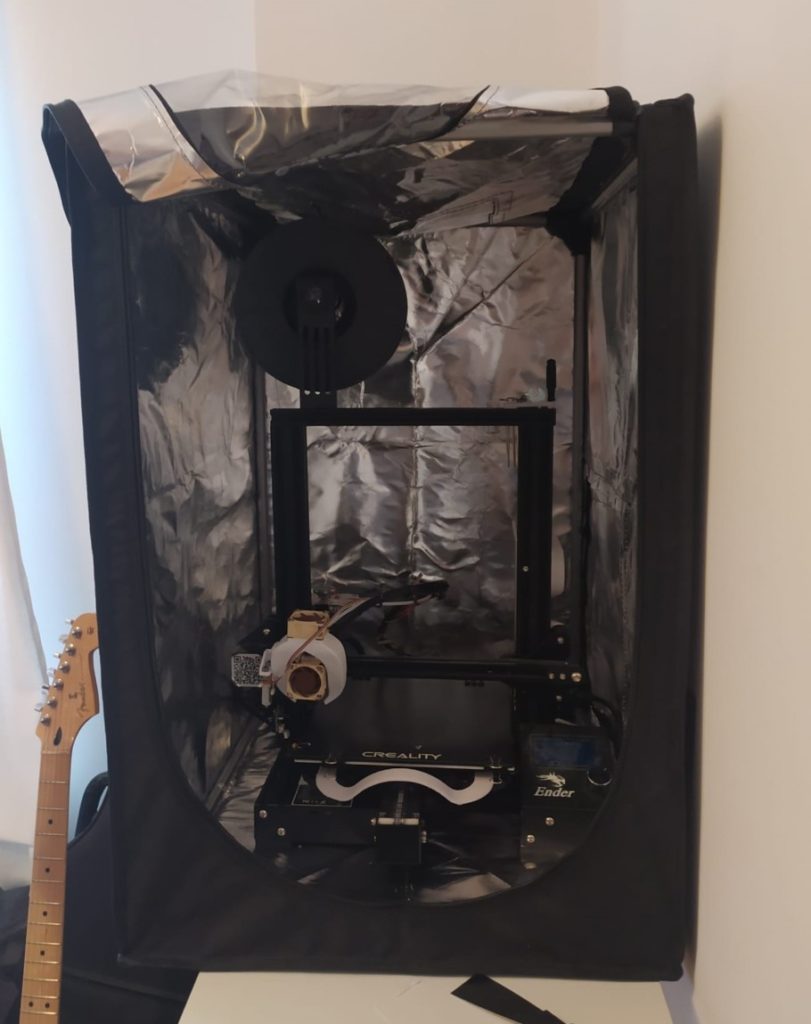
Polycarbonate tends to warp and delaminate when printed in open air so I strongly advice having and enclosure to keep a warm steady ambient temperature around the printer. The most common polymers used for printing such as PLA or PETG are easy to print in open air and require lots of cooling to set the new layer in place. With PC things get a little bit more complicated because tensions appear in the model when the molten plastic solidifies and contracts. Delamination occurs when the layers don’t fully fuse together, and they separate making the print fail.
Having an enclosure won´t eliminate these problems but will reduce them significantly. More professional printers use an active heated chamber to print in and get good results. If you were to actively heat the enclosure, it is not advisable to actively heat the inside beyond 50°C-60°C. As the motors, sliding systems and electronics aren’t prepared to handle such ambient temperatures and will degrade very quickly and get damaged permanently.
Filament dryer and dry box
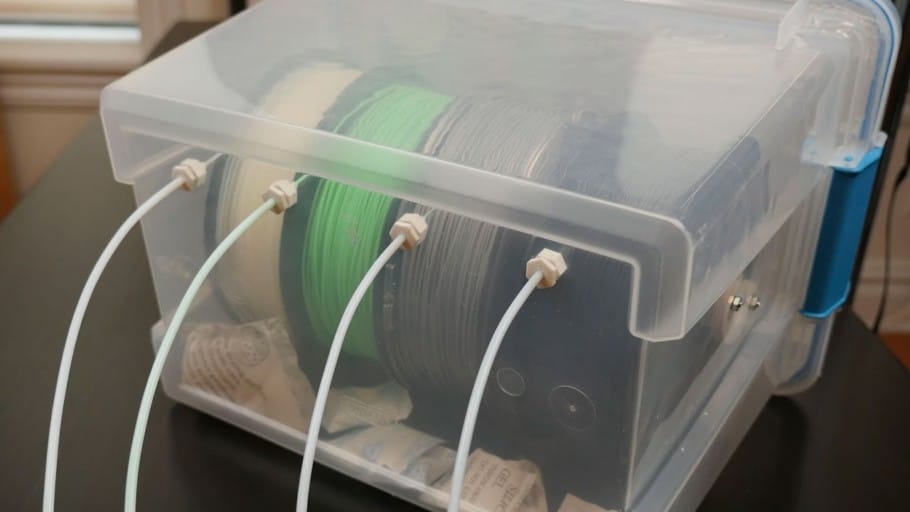
PC is very hygroscopic, which means it absorbs moisture from the air. Exposure to open air for as little as a couple of hours depending on the relative humidity, can result in poor quality prints. Stringing is greatly increased, and strength can be reduced with moist filament. The water inside the filament forms bubbles when it passes through the extruder making a popping sound and leaving noticeable holes in the part. Prints turn out opaque and with poor surface quality. This is very noticeable when trying to print transparent parts or when aiming for good optical properties.
Having a filament dryer will increase your chances for success when trying to print with PC. Dryers use low heat and a fan to blow dry air into the spool. Food dehydrators are a good choice too, just use them exclusively for filament. Actually, some commercial filament dryers are rebranded food dehydrators.
If you don’t want to spend on a filament dryer you can also use a conventional oven at low temperature or even create a dehydrator with your print bed and a cardboard box.
You should also consider using dry boxes to print from and to store the filament. Dry boxes are airtight containers that have silica gel and sometimes a heating element to keep its contents dry. Some even include thermohygrometers to give you a reading of the temperature and relative humidity of the inside.
Vacuum chambers are a great way to store filament too. Some commercial dryers use a combination of heat a vacuum to remove the moisture from spools of hygroscopic polymers.
Ideal Slicer Settings when printing Polycarbonate on an Ender 3?
- Extruder Temperature: 260°C – 315°C
- (Extrusion temperature varies between filament brands and blends so refer to the manufacturers’ recommendations and test it in your machine with 5°C increments until you get the best results)
- Bed Temperature: 100-150°C
- Layer Cooling Fan: off
- Retraction settings must be adjusted to the minimum possible
Can the Ender 3 print Nylon?
Most of the recommendations that apply for polycarbonate, apply for nylon too. Nylon is also a high temperature plastic but can print at lower temperatures than PC. All hardware upgrades mentioned in this article are necessary to successfully print Nylon.
Ideal Slicer Settings when printing Nylon on an Ender 3?
- Extruder Temperature: 240°C – 270°C. (Extrusion temperature varies between filament brands and blends so refer to the manufacturers’ recommendations and test it in your machine with 5°C increments until you get the best results)
- Bed Temperature: 50-90°C
- Layer Cooling Fan: off
How to improve bed adhesion
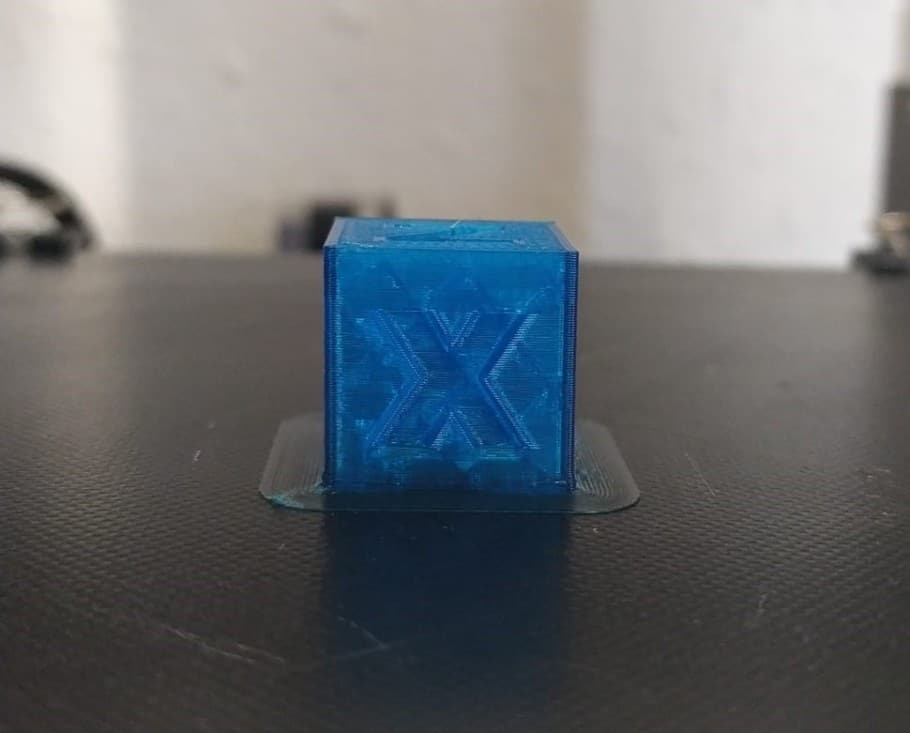
Since both Polycarbonate and Nylon are printed at really high temperatures, they are much more prone to warping if they cool down too quickly than filaments like PLA. Although I already mentioned that you should get an enclosure, here’s one really useful tip that doesn’t require you to go out and purchase additional equipment and that works really well.
There is this study that was conducted about how bed temperature affected adhesion, and the conclusion is this; “This study shows a significant increase in adhesion forces when printing parts at a bed temperature slightly above the glass transition temperature of the printing material”.
What does this mean? Essentially, if your prints are warping or detaching from the bed, then you need to find out what the glass transition temperature of your filament is (PLA is 60°C, PETG 80°C, ABS, 100°C, etc.), and set the bed temperature slightly above it.
If you don’t want to have to go through all the trial and error that we did in order to find the Ideal Settings for creating high-quality prints on your Ender 3, then definitely check out our own Cura Profiles tailored specifically for the Ender 3 Printer Series.
Conclusion
It is possible to print some high temperature plastics in an ender 3 if you make some upgrades. Bear in mind that some technical knowledge is required to make most of the upgrades needed. There is a large community that uses Ender 3 printers and share their experiences so with this guide you can know what to look for.
Check out my other articles on how to upgrade or modify your Ender 3 printer.
Check out our recommended products section
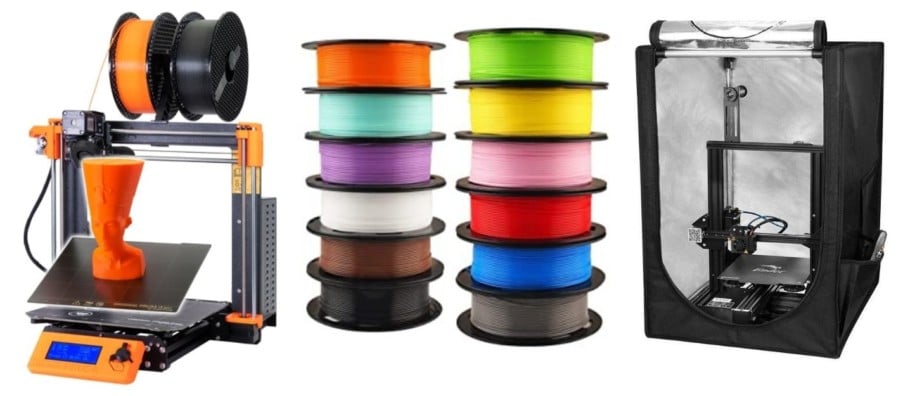
We created a recommended products section that will allow you to remove the guesswork and reduce the time spent researching what printer, filament, or upgrades to get, since we know that this can be a very daunting task and which generally leads to a lot of confusion.
We have selected just a handful of 3D printers that we consider to be good for beginners as well as intermediates, and even experts, making the decision easier, and the filaments, as well as the upgrades listed, were all tested by us and carefully selected, so you know that whichever one you choose will work as intended.
Error processing API data.
Hello I have a question, is it also required to upgrade the stock heat-element of the ender 3 pro to resist temperatures like 300C or is it really just the thermistor and the all metal hotend when it comes to hardware?
Best Regards,
Ricco
I am having trouble figuring out how to fit the new thermistor into the microswiss hotend. Do they actually fit, or do I need to buy another hotend?