When 3D printing, we should always take into consideration the final usage and placement of our print. This will save us a huge amount of printing hours, wasted material, and unexpected negative surprises.
One of the most important things to consider is the temperature that the part will be exposed to. Given the fact that PLA is the most popular thermoplastic used in 3D printing, it comes as no surprise that we may be interested in knowing if PLA is heat resistant or not.
It is not recommended to use PLA for printing models that are going to be exposed to temperatures above 60°C (149°F) for prolonged periods of time due to the fact that this is its glass transition temperature and it will start to deform once it reaches this temperature, making it not a suitable thermoplastic for this kind of environment. ABS, Polycarbonate, or PETG should be used instead.
Having said that, if PLA is the only option available, it is possible to increase its resistance by annealing the object.
Will PLA melt in the sun
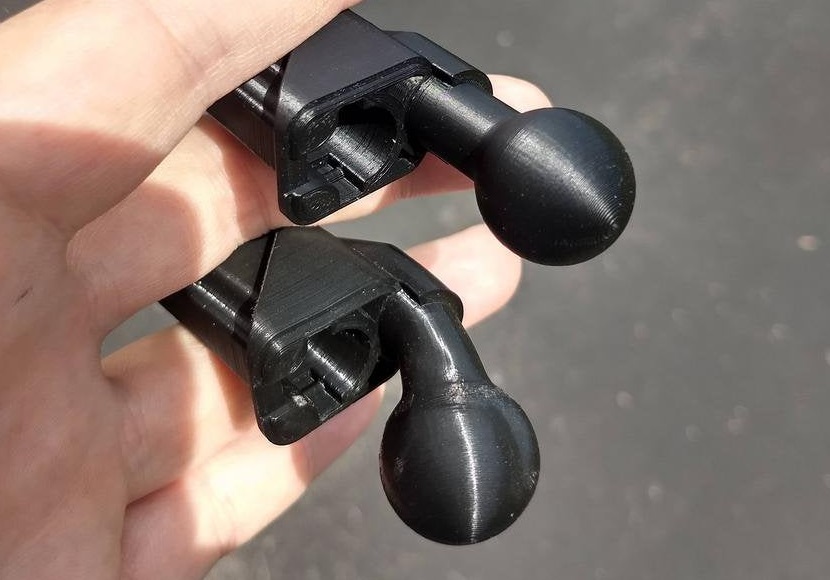
PLA’s melting temperature is at around 160°C to 180°C, meaning that it will never melt in the sun, regardless of where you live. Nonetheless PLA is less resistant to heat than other filaments like ABS, PET or PETG, and is usually not recommended for uses that require prolonged exposure to the outdoors and the sun.
In a nutshell, as a rule of thumb: never use PLA to 3D print functional parts or objects meant to be used outdoors. If you don’t like ABS, use PET or PETG for these two usecases.
As I mentioned before, depending upon the raw materials, additives, colors, and manufacturing process used by a particular brand to make a PLA filament, its melting point can be somewhere between 160-180C. Even on a crazy hot summer day, it never gets nearly as hot as 160C. So the answer is: NO, PLA will not melt in the sun. Although it won’t melt, it will become brittle and lose its tensile strength and impact resistance.
Additionally, due to the fact that the glass transition temperature (Tg) of PLA is only 60°C-65°C, your PLA prints will also tend to deform, bend, twist, warp, and sag within a few hours if you leave them in the sun on a hot day.
If you live in a region that tends not to have extremely hot temperatures, you might be inclined to think that these previous sentences do not apply to your specific scenario. Although you might be correct, keep in mind that it only takes a few days a year to deform, bend and ruin the structural integrity of your 3D print.
Another thing you should consider when printing an object that will be exposed to sunlight is its color. Due to the fact that darker objects absorb UV light and energy more efficiently, they have a tendency to also heat faster (and more) than white objects. Although the overall recommendation is to still avoid using PLA for this purpose, choose clearer colors if you have no other options available.
Will PLA melt inside a car?
Even if the ambient temperature is only 35-40C, it will still be enough to deform, warp or sag the PLA objects. If you own a digital thermometer, you will be able to verify that a car that is parked under direct sunlight will have a cabin temperature of around 10°C-20°C hotter than the outside temperature. This is mostly due to the greenhouse effect in the cabin, and the body and interior color of the car.
Objects placed on the dashboard will be the most prone to deformation and warping on a warm day, but placing an object on the backseat or the trunk won’t guarantee that the object preserves its shape and structural properties. Although placing an object inside of the trunk will technically protect it from the greenhouse effect, it will still be prone to deformation if it is placed there during prolonged periods.
In cases where the object only needs to be transported from one place to another in a car during a hot day, I recommend placing it inside a cooler. Although this may sound a little extreme, it is always in these cases to prevent than to react. Especially if our print took several hours to finnish.
Best filaments for heat resistance
Polycarbonate (resists 150°C)
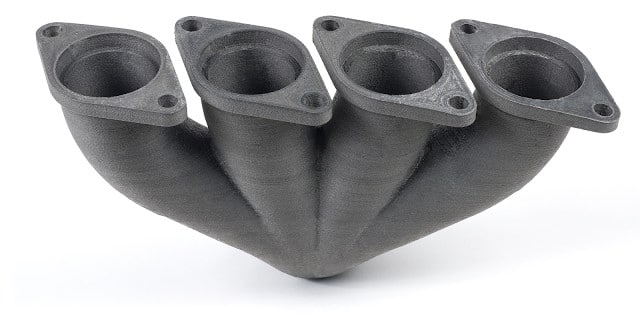
PC usually comes in two flavours: PC/PBT (Polybutylene terephthalate) and PC (straightforward polycarbonate). Their glass transition temperatures are 110C and 150C respectively.
Polycarbonate costs a bit more than other filaments, but it is one of the best thermoplastics when it comes down to heat resistance. This has lead to many industries preferring to use PC as their go-to thermoplastic. Apart from that, it is also a very tough and abrasion-resistant material, with good tensile strength and impact resistance.
Keep in mind that unless you have access to an industrial-grade 3d printer, you won’t be able to print pure polycarbonate and will have to compromise and use a polycarbonate blend, much like Prusa’s PC Blend or the Polymaker Polycarbonate filament.
ABS (resists 105°C)
With a glass transition temperature of 105C, ABS is also one of the best choices to print heat-resistant parts. It is also a cheap, widely available, and tough material. The downside is that it is difficult, messy to print, and creates toxic fumes that require us to really consider installing proper ventilation.
PETG (resists 80°C)
PETG has a glass transition temperature of 80C. It performs way better than PLA and holds itself up pretty well on a hot summer day even if the ambient temperature is above 45°C.
In my own anecdotal and less than scientific experience, even a black-colored PETG is a good filament to print outdoor functional objects. They can easily last for years before they fail.
Having said that, I still don’t recommend it for printing objects for your car. In warm regions, the cabin temperature of a car parked in the direct sunlight with cooling off can be as high as 70C. This can easily warp, deform or sag your PETG prints.
If you’re thinking about printing with PETG, then I’d recommend you read this article I wrote on what specific settings to use, and you should also get this PETG filament since there are some very cheap ones out there that print terrible!
Is PLA UV resistant?
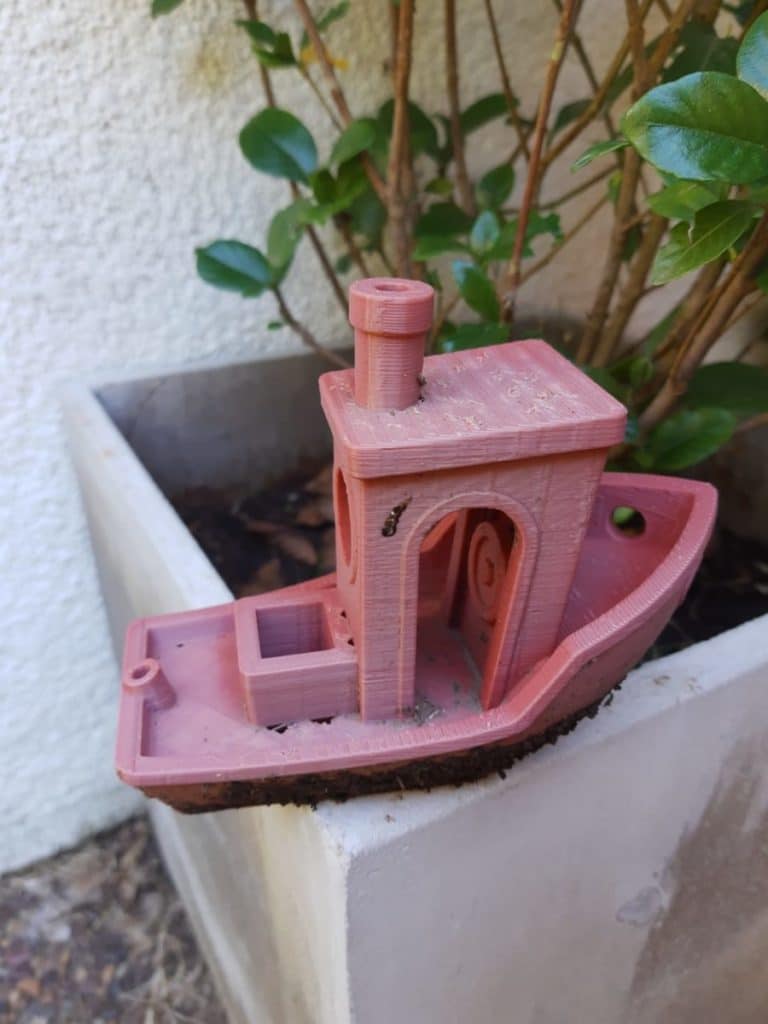
PLA is by no means a UV-resistant thermoplastic. It can be permanently damaged if exposed to sunlight for a prolonged period of time.
PLA is made from organic compounds obtained from plants and is biodegradable and UV rays trigger photochemical effects in the structure of its polymer molecules. This accelerates the degradation process and PLA quickly becomes brittle and prone to breaking easily. In summary, like mentioned previously, it is not recommended at all to print functional PLA parts if there is a risk of UV exposure.
Is sunlight going to impact the looks of a PLA printed object?
PLA is perfectly fine to print aesthetic models. UV rays exposure at normal temperatures won’t deform, warp or sag them, but make no mistake, they will become brittle and weak. The only issue is that the photochemical effect triggered by UV rays also triggers the degradation of the coloring pigments. This means that the color of the PLA models will fade fairly quickly upon exposure to UV light.
Best UV resistant filaments for 3D printing
Altough we previously went through the most heat resistant filaments and this sections seems redundant, it is important to make a distinction between UV light exposure and heat resistance. Although they tend to go hand in hand when dealing with the outdoors, this is not always the case.
PETG
PETG in its purest form (without colors and additives) performs decently outdoors and is rather resistant to direct sunlight exposure, even for prolonged periods of time. As a side note, it is also resistant to corrosive chemicals and water, which makes it a compatible thermoplastic for most outdoor use-cases.
Why does PETG perform better than ABS and PLA in sunlight
Due to its smooth surface, PETG is able to simply reflect most of the radiation that lands on its surface. Hence, UV radiation doesn’t trigger the photochemical reactions that can make it brittle and fade its color.
Natural PETG is transparent. This means that it doesn’t trap heat energy inside the polymer structure. Hence, it’s more resistant to an increase in the ambient temperature.
Unlike ABS, which is stiff, the polymer structure of PETG is quite flexible, making it expand and contract. As a consequence, it expands and contracts with temperature changes, mitigating the negative effects of climatical variability.
ASA (Acrylic Styrene Acrylonitrile)
ASA is a very lightweight thermoplastic that was developed as an alternative to ABS. It is the best choice for printing heat and UV-resistant functional parts, as it is also fairly strong and has a high impact and high wear resistance.
ASA is the most recommended filament for printing objects that experience harsh and extreme weather. Due to its characteristics, It is already used by manufacturers to make outdoor weather resistance house for LED lighting and solar lights. Vehicle dashboards are also commonly made from ASA.
Although it is structurally similar to ABS, ASA is more weather and UV-resistant (by a factor of 10).
The downside of ASA is that it is expensive when compared to its alternatives. This thermoplastic is also difficult to print with a regular printer, leading to failed prints and wasted material.
How to make PLA more heat-resistant
Due to the low difficulty of the process and the good results that we can obtain, annealing a PLA object is one of the best ways to significantly increase the strength and heat resistance of PLA objects.
By annealing a PLA object, I mean slowly heating it up to 60°C (140°F) or slightly above, but below 160°C (320°F). In other words, you should expose said object slightly above the glass transition temperature but definitely below its melting temperature. I recommend exposing the printed object to this temperature for roughly 30 to 45 minutes.
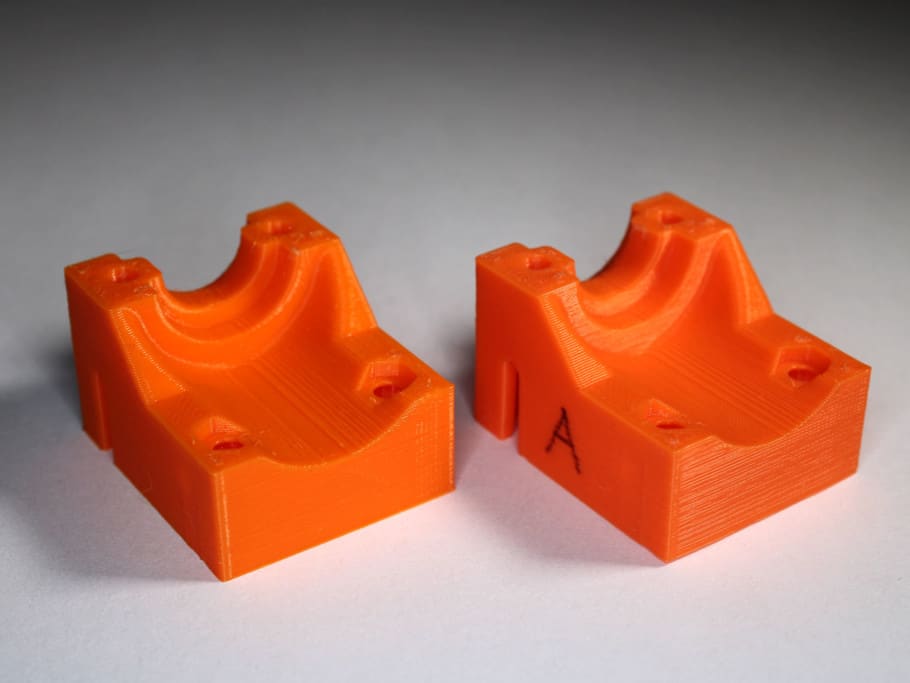
How does annealing improve the strength and heat resistance of a 3d printed object?
Annealing allows printed parts to be stronger and more durable by increasing the number of large crystal structures in the plastic, which helps to redistribute the stresses and heat energy more evenly.
Plastics at a microscopic level typically appear disorganized and amorphous. They are likely to cause a phenomenon called “banding” when printed, which is when the plastic cools quickly in some areas forming small crystals and slowly in other areas where large crystals are formed. The annealing process relaxes the structure of the part and the molded stress is thus reduced.
Annealing also makes post-processing easier and saves time and cost for finishing processes due to the fact that it also smoothes the surfaces of the object, fills missing holes. Annealing tends to make the part injection molded, which is usually seen as more professional and industrial-grade.
Check out our recommended products section
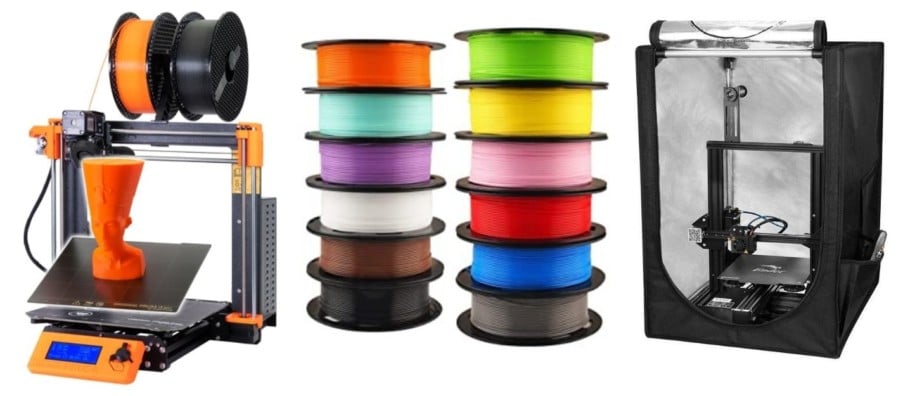
We created a recommended products section that will allow you to remove the guesswork and reduce the time spent researching what printer, filament, or upgrades to get, since we know that this can be a very daunting task and which generally leads to a lot of confusion.
We have selected just a handful of 3D printers that we consider to be good for beginners as well as intermediates, and even experts, making the decision easier, and the filaments, as well as the upgrades listed, were all tested by us and carefully selected, so you know that whichever one you choose will work as intended.
Error processing API data.