A car contains literally hundreds of little plastic parts that can be very difficult to find online. Some of those have such low demand and are so specific that manufacturers do not even bother to produce and offer them.
This is where 3D printing shines since it is especially valuable when we need to create custom parts in low quantities.
3D printing allows us to create high quality, custom-designed replacement parts for our cars, and on top of that, at a lower cost and especially at a much faster pace.
Can you 3d print car parts?
Yes, it is possible to 3D print replacements for specific parts of your car that are sometimes difficult or impossible to find. You can 3D print cup-holders, knobs, clips, and other non-safety related parts.
Unless you are an engineer with access to a million-dollar state of the art machine, I would probably avoid printing parts that are going to be subject to pressure, tension, or higher temperatures.
It might be a redundant statement, but please do not replace a component of your safety belt with a coarse PLA print. You will be on the fast track to earning your own Darwin Award.
Major industry players like BMW, Volkswagen, Opel and Bentley also make heavy use of additive manufacturing but, before you get too excited and try to start your own 3D-TeslaXYZ, you should consider the following caveat: the price tag in Bentley’s state of the art Stratasys 3D printer has 3 or 4 more zeroes than the one on your Ender-3.
Popular 3D prints for your car
Experienced designers can always take a caliper and create their own replacements. It can also be the case that you are too lazy, do not love your car that much, or a combination of both (my case).
Lucky for us, there are diligent and industrious folks that not only designed many parts but also were kind enough to share them. There is always a non-zero probability that we will find what we need on our own 3D model finder!
If your car has no broken plastic parts that are in desperate need of a replacement, do not despair! You do not have to break something as an excuse to justify your 3D printer.
Just take a look at these beautiful examples!
- Visor clip for your sunglasses
- Trash bag hooks for your seatback
- Coin organizer for your cup holder
- Customizable smartphone holder
I printed most of these. Perhaps they did not radically change my life, but they are nice additions. My coins look better in the organizer than on the floor*.
*My car was full of orange gadgets because I was too lazy to change the filament spool. Do not be like me, you will eventually regret it and print everything again in black.
Filaments for car parts
The type of filament that you should use for printing your replacement parts is obviously dependent on the part but, as a rule of thumb, Acrylonitrile butadiene styrene (ABS) is a good choice. The main properties that make this thermoplastic suitable for your car are the following:
- It is both resistant to shock and flexible.
- It has a high glass transition temperature (105° C or 221° F).
- It can withstand temperatures ranges of -20° to 80° C for long periods of time.
On the downside, it can be tough to print ABS parts and I definitely recommend that you use a printer with a heated bed and an enclosure to avoid warping. You should also keep the room ventilated and avoid the inhalation of fumes.
If you are just getting started and do not have a printer with a heated bed and an enclosure, I should also tell you that it is perfectly OK to print your parts in PLA.
Just keep in mind that this thermoplastic has a lower (but still acceptable) glass transition temperature and is slightly less resistant. Just add a little more infill to your print and avoid parking your car in the Sahara desert during the summer.
However, if you want the ease of printing of PLA but a material that is much more heat- and shock resistant, try PETG!
PETG is a filament that is almost as easy to print as PLA (only suffers from poor bed adhesion at times) and it also costs the exact same.
How is 3D printing used in the automotive industry?
Due to the nature of the automotive industry, most manufacturers have been early adopters or at least testers of the technology.
It not only revolutionized the way that manufacturers can iterate and prototype faster and more efficiently, but also allows them to create highly specific tools and complex parts.
Revolutionizing the prototyping process
Smaller companies use 3D Printing for creating highly customized parts that would otherwise be impossible to produce due to scale inefficiencies.
Additive manufacturing proved once again to be vital when iterating and perfecting designs. The whole process would be otherwise prohibitive due to its costs.
On the other hand, larger companies are combining traditional manufacturing processes with additive manufacturing.
Allow for client customization
In the early days of the automotive industry, Henry Ford stated, “A customer can have a car painted any color he wants as long as it’s black”.
This could not be less true nowadays thanks to 3d Printers! The British manufacturer MINI pushed this to the limit, allowing clients to have full control over the major design aspects of their cars.
If you want to acquire a MINI and are willing to pay for the premium, you can choose from a wide range of colors, patterns, fonts, and images.
If you want to find out more about mass customization in the automotive industry, you might be interested in reading about Twikit*, a startup based in Belgium that provides an end-to-end platform that allows users to personalize cars and tailor vehicles to each client’s own individual preferences.
*I find it necessary to say that I am by no means related to Twikit. I just find the company fascinating!
The output requires little to none technical operations since the software already outputs all files required for that specific order.
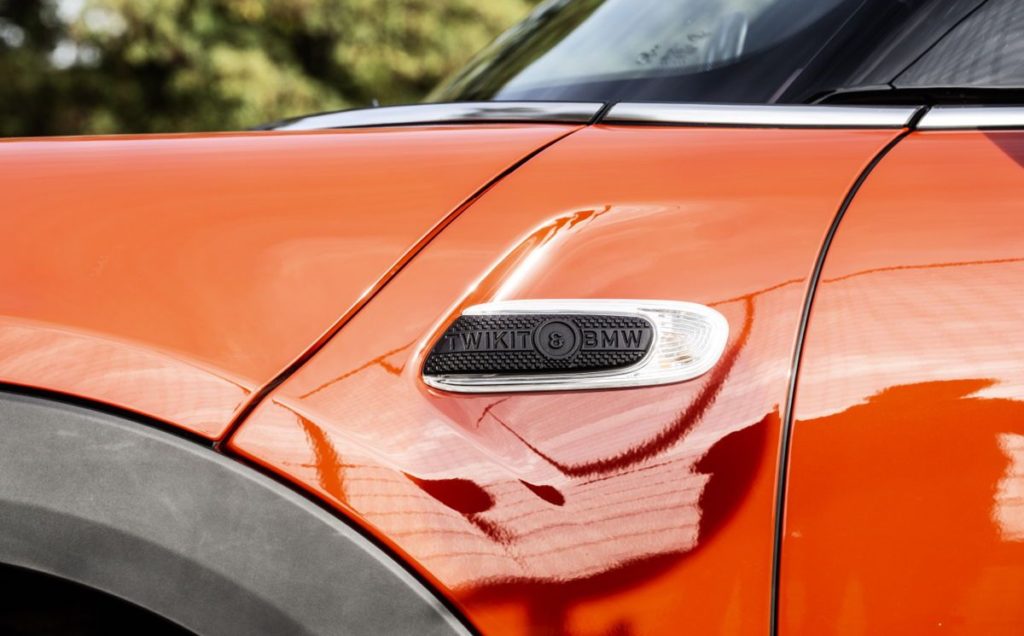
Complex Parts
Bentley, the luxury car manufacturer, is famous for heavily using Stratasys* printers. They first start with a 1/10 scale prototype that is taken to full size once it is validated by the design and engineering teams.
Stratasys industrial-grade printers allow Bentley to produce multi-material objects that were previously unimaginable. This is not a trivial feature, since it opens new design paradigms that allow for lighter, more efficient, and reliable parts by combining different elements.
They not only use it in the prototyping process but also incorporate it into the final cars that we see on the street.
Grills, headlamps, moldings and door mirrors are just a few example parts that Bentley 3d prints for most of its current models. Additive manufacturing allows to design difficult, weird and complex geometries that simply where impossible to create with injection molding.
*If you watched the Netflix documentary “Print the Legend”, you might remember Stratasys as the large company that sued and finally acquired MakerBot. In case you did not, close this tab and open Netflix right now!
3D-Printed for the car manufacturing process
Automotive factories are leveraging 3d-printing technology to create hundreds of high quality, tailor-made, and highly customized tools for their day-to-day operations.
The fact that Volkswagen, BMW, and Opel, three major players in the industry are using the technology clearly vouches for additive manufacturing and its reliability.
Below is a simple example of a wheel protecting jig. Despite its simplicity, it reduces operational time, cost, and error rate.
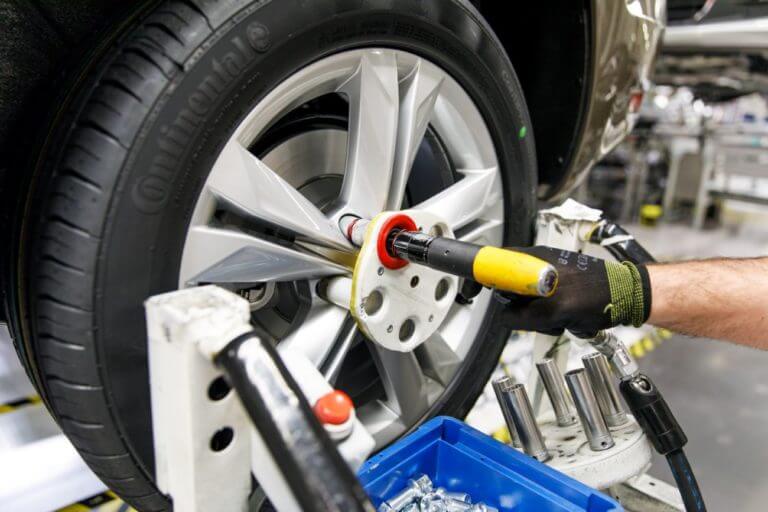
For a regular person that only performs this task when changing a flat tire, this tool may not seem very valuable. On the other hand, if you had to do this a thousand times, you would be willing to pay a bucket full of cash*.
*Right now, I’m writing this from Argentina. It might surprise you how cheap it is to fill a bucket with cash.
Bonus: An (almost) totally 3d-printed Car
During the International Manufacturing Technology Show held in 2014, and after only 44 hours of printing, the first electric car that heavily utilized 3d-printing was born. It was build using a big area additive manufacturing machine (BAAM) or, in simpler terms, a big FDM printer.
Although it clearly does not meet the required safety test requirements of any country, I definitely would not mind having my own Strati!
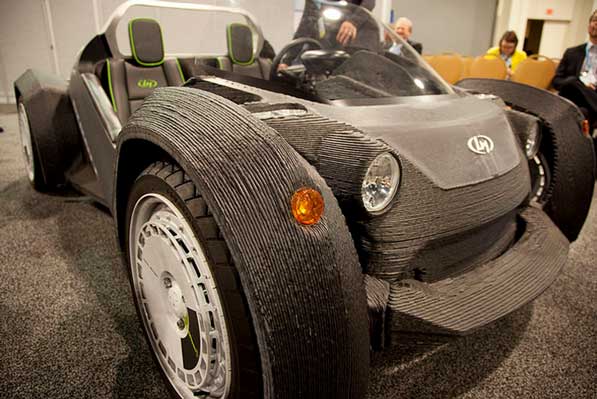
Check out our recommended products section
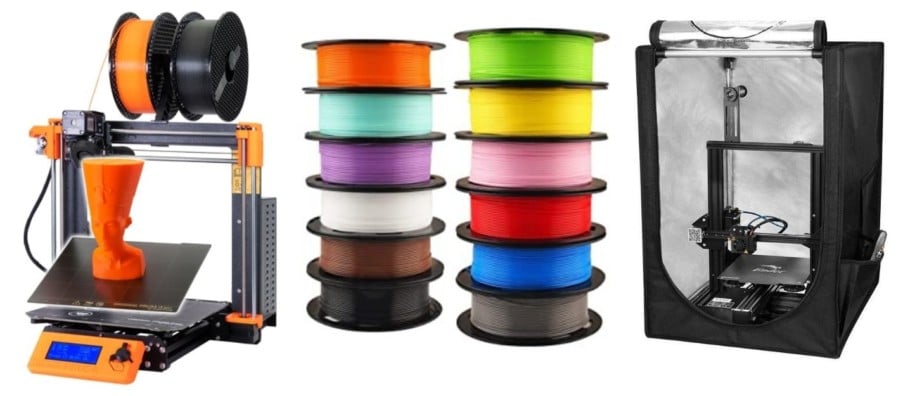
We created a recommended products section that will allow you to remove the guesswork and reduce the time spent researching what printer, filament, or upgrades to get, since we know that this can be a very daunting task and which generally leads to a lot of confusion.
We have selected just a handful of 3D printers that we consider to be good for beginners as well as intermediates, and even experts, making the decision easier, and the filaments, as well as the upgrades listed, were all tested by us and carefully selected, so you know that whichever one you choose will work as intended.
Error processing API data.
Hi there
My name is Adam, I’m working a project for my car. I was wondering if you could 3d print the part. I’m sure it has high temperature during cold and hot weather. I’m need some light sockets which aren’t made at all. I’ve searched everywhere for these and have no luck, maybe you would have some luck here. they are headlight turn signal sockets. I don’t know the measurement of these sockets. but if you can make them how much.
Thank you
Adam