The demand for durable, protective gear during World War II ignited the production of polymer plastics. At that time, the goal was to develop bullet-proof copolymer plastic sheets.
The Borg-Warner corporation originally patented the idea of ABS plastic in 1948 but it took 6 more years for its commercial introduction. Their ABS plastic product was trademarked as Cycolac. The telephone company Bell first used ABS plastic for their household telephone parts.
Today, there are over 6000 grades of ABS plastic that are designed for more than just telephones. And some plastics can be recycled. Recycling programs have been established to decrease pollution in our air, water and reduce our energy consumption. Join me on learning all about ABS plastic and if it is a renewable material for preventing waste.
So, is ABS Recyclable?
Yes, ABS plastic is considered to be “recyclable” since it’s a thermoplastic, which means that you can heat the plastic and use it again as filament by extruding it.
However, the molecular linkages of ABS will break down with every heat cycle, making it less durable, and to prevent this you will need to add some pure ABS to the recycled one for durability.
What is ABS Plastic?
Acrylonitrile butadiene styrene is otherwise known as ABS.
ABS is a petroleum-based polymer plastic that can be remodeled at different temperatures. Thermoplastic polymers, like ABS, can become flexible or rubbery when heated. Once they cool down, they have the ability to solidify again.
ABS is categorized as an amorphous compound which means it does not follow the natural phase trend of other ordered materials. More precisely, when it reaches a specific temperature, it does not transform from a solid to a liquid. Accordingly, it does not have a genuine melting point. Instead, it has a glass transition temperature of 105℃.
The glass transition temperature is the temperature at which an amorphous substance transforms from a rigid state to a rubber-like state.
ABS is called a terpolymer because it is made from 3 different polymers. A polymer is a type of material that is made up of repeated, large subunits of molecules.
The chains are linked through chemical reactions called polymerization. As you can tell from its full name, the 3 polymers that make up ABS are acrylonitrile, styrene and polybutadiene. The molecular structure of ABS consists of a long chain of polybutadiene.
In a criss-cross manner, the smaller chains of styrene and acrylonitrile are attached to the long chain.
The unique molecular formation of ABS and the properties of each polymer contribute to its overall characteristics.
The adjacent nitrile groups in the chain are attracted to each other and increase the plastic’s strength. Acrylonitrile increases its rigidity, hardness and the temperature in which the material distorts. Plus, it gives ABS its resistance against some chemicals and mechanical stress.
Styrene contributes to ABS’ glossiness, its impermeability and also its hardness and rigidity.
Polybutadiene acts mainly to make the material tougher and malleable. The percentage of each component is usually 15-30% acrylonite, 5-30% butadiene and 40-60% styrene.
But, the percentages of each polymer vary with the grade of ABS plastic. It really depends on the purpose of the application.
For instance, if a rubbery and flexible plastic was needed for sports equipment, manufacturers would create a polymer blend with a higher content of polybutadiene.
How is ABS made?
There is a lot of science used in fabricating ABS. Initially, you will need to isolate all 3 polymers.
Acrylonitrile can be synthetically made by combining petroleum and ammonia. Since butadiene is a petroleum hydrocarbon, it can be made through the petrochemical process of thermal cracking.
And styrene is synthesized through the dehydrogenation of a compound called ethylbenzene. For your information, dehydrogenation is a chemical reaction that involves the removal of a hydrogen molecule from a compound.
Now that you have the polymers, ABS plastic can be manufactured in 2 ways: emulsion polymerization and continuous mass polymerization.
Emulsion polymerization of ABS is a multi-step process. Emulsion involves mixing 2 or more immiscible liquids together.
First, butadiene and water are emulsified. A catalyst is added to speed up the reaction and the resulting product is rubber latex. Next, styrene, acrylonitrile and the rubber latex are emulsified, again with a catalyst.
The final product is a mixture of ABS particles in water. A centrifuge is then used to isolate the ABS pellets and they are dried to extract excess water which gives you pure ABS.
The problem with emulsion polymerization is that there are many steps. This may lead to inconsistencies between each product in the sequence. Another factor is the added substances such as catalysts and emulsifiers. Since the substances are found in the product at the end of the process, they are considered to be impurities.
So, with this product, you are left with a low-quality, yellowish ABS resin.
On the other hand, continuous mass polymerization is one long step and it doesn’t have many extra substances added.
You begin with polymerized butadiene rubber pellets that are then broken down into smaller pieces. Those pieces are dissolved into a mixture of styrene and acrylonitrile. Later the whole solution is placed in a reactor where styrene and acrylonitrile are polymerized.
While polymerization is occurring, the solution is continuously mixed which breaks down the particles into even smaller pieces. The leftover monomers are isolated and can be recycled to start the process again.
Continuous mass polymerization is a more effective method for producing pure ABS because it makes consistent, high-quality and opaque ABS plastics.
What is ABS used for?
Aside from being a material used for fused-deposition modeling in 3d printing, ABS has numerous applications. ABS’ properties and blend of polymers makes it an ideal and versatile plastic that is used in a variety of industries.
ABS is a lightweight plastic that is an integral part of the modernization of the automotive industry. Car manufacturers are moving away from using heavy metals for materials and parts. Instead of metal, ABS is used for panels, door handles, seat belts, dashboards and much more.
In your home, I bet you can find ABS plastic just about everywhere. It is used in many appliances for control panels, wall sockets and in other appliances like vacuums, food processors, fridges and even furniture and luggage.
ABS is now used in plumbing as a substitute for metal in pipes and fittings. This is because it does not corrode.
For electronics, ABS plastics is made into caps for keyboards and computer cases. We are all familiar with LEGO toys, which is ABS. And it is found in some plastic instruments like recorders, oboes, clarinets and pianos.
One of the most fascinating uses for ABS plastic is in the medical industry. It is used to make non-absorbable sutures, artificial tendons, attachments for drug delivery through tracheal tubes, inhalers and nebulizers.
How to recycle ABS
ABS plastic has been assigned the resin code #7, which is the category for “other plastics”. Most of the time, ABS is not accepted at recycling plants but I suggest checking with your municipality just in case. Some companies have developed curbside pickup programs for #7 plastics.
If they are accepted at your local material-recovery plant, they are broken down like other normal plastics. The collection stage is accomplished via froth flotation.
ABS is separated from other forms of plastic particles in a water-oil mixture. Then, it is ground up into smaller granules. The granules are then fed through extruder machines that can mold the resin into various shapes. The shapes can be ABS plastic sheets, filaments or the resin can be directly inserted to injection molding units.
Furthermore, ABS printed material can be recycled and transformed into filament again using a machine like the Filastruder.
The Filastruder can create filament of your desired color and size for your 3d printing project. However, I recommend checking the tolerances for the Filastruder or any extruder machine as they vary.
There are a few considerations you must take into account when using recycled ABS plastic with the Filastruder: The size of the pellets must be 5mm in dimensions or smaller. Otherwise, they could block or damage the machine or make non-uniform filament.
To add to that, if you have impurities in the recycled pellets, you will have them in your finished product. Make sure you are grinding the pellets carefully and using the right equipment for the job.
Lastly, because you have repeatedly heated the ABS plastic, it will eventually lose its ability to resist heat. This is because the molecular linkages will break down with every heat cycle. To prevent this, you will need to add some pure ABS pellets to the recycled pellets for durability.
Is ABS a toxic material?
Thankfully, when ABS plastic is in its final form, like appliances or toys, it is considered to be non-toxic.
It is stable, non-leaching and so far, it is not a known carcinogenic. Although, it has not been regulated for use in the food industry or for medical devices within the body.
The issue is that ABS becomes toxic after undergoing different processing methods. If exposed to extreme temperatures, ABS plastic is flammable. Obviously this causes a fire hazard but there are also toxic fumes that are produced like carbon monoxide and hydrogen cyanide.
In fact, any “melting process” that ABS plastic undergoes is hazardous because the terpolymer is broken down into each polymer, such as styrene and acrylonitrile. This applies to the use of solvents for smoothing down the designs on 3d printed pieces.
Thirdly, these problems pose ecological threats.
Another point is that 3d printing causes ABS dust and fine particles to be dispersed in the air. This has already been known to cause adverse health effects. The dust particles are eye, skin and lung irritants.
Finally, ABS undergoes degradation with UV exposure which could cause some of the chemicals to leach out over time.
Is ABS Biodegradable?
Biodegradable materials are those that decompose through microorganisms like bacteria and fungi, and unfortunately, ABS plastic is not biodegradable.
Most of it ends up in landfills because some recycling plants do not take them. It is a common misconception that “biodegradable plastic” can be recycled when facilities still do not accept them.
They claim that the final compost product will be inferior or low quality. And, it actually takes a very long time for materials labeled as biodegradable plastic to decompose naturally in the environment.
Final Thoughts
So, yes ABS plastic is considered to be “recyclable”, in the sense that you can heat the plastic and use it again. Along with its advantageous properties, it has several disadvantages. ABS plastic degrades and scratches easily.
I have discussed how solvents are used to smooth out ABS designs but if you use too much, you could dissolve the essential parts of your piece.
And, ABS plastic can be susceptible to cracking if you are using certain oils or grease as lubricants. For improvement, manufactures have developed ABS plastic alloys with polycarbonate. Polycarbonate further increases ABS’ strength, stiffness and heat resistance.
But, there are other alternatives to using ABS plastic for 3d printing that may be more suitable for you.
PLA or Polylactic acid plastic is another thermoplastic option.
PLA is a polyester polymer which means it contains ester bonds to link the chains together. It is a favorable material because it is made from renewable resources such as fermented plants. It is a stronger and stiffer material than ABS and it becomes flexible at a lower temperature without warping.
The downside is at moderate temperatures, the plastic loses its durability, making it crack easily.
Nylon polymer was actually the first thermoplastic polymer created artificially. It is a polyamide polymer that is composed of amide bond linkages.
As a printing material, it is less strong and less stiff than PLA and ABS. It has a stronger ability to withstand force or shock than ABS and is resistant to chemicals.
This allows it to be used for more industrial applications. However, it requires a high temperature for extrusion. Recently, manufacturers have developed fiber alloys with nylon to increase its strength.
In my opinion, when it comes to your health, plastics and high heat are never a good combination. I advise you to research thoroughly the plastic material you have chosen for printing.
There are always greener options out there. If you do decide to use ABS plastic for printing, try to avoid inhaling those vapors and fine particles. I suggest building an enclosure around your printer. And, always make sure you are working in a well-ventilated area.
Check out our recommended products section
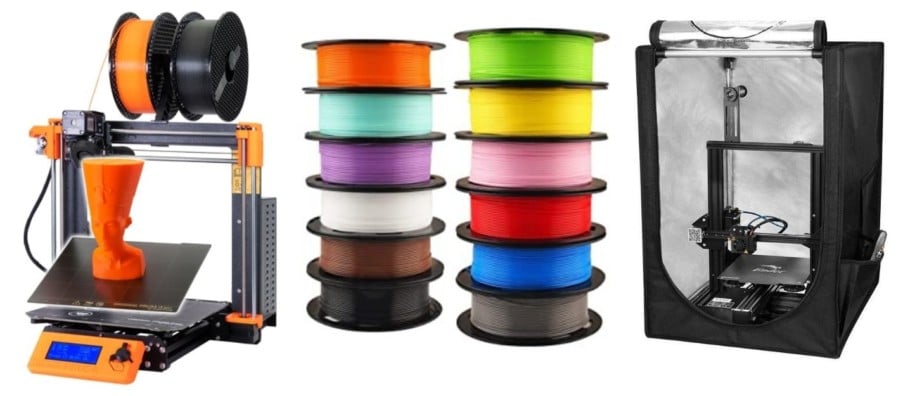
We created a recommended products section that will allow you to remove the guesswork and reduce the time spent researching what printer, filament, or upgrades to get, since we know that this can be a very daunting task and which generally leads to a lot of confusion.
We have selected just a handful of 3D printers that we consider to be good for beginners as well as intermediates, and even experts, making the decision easier, and the filaments, as well as the upgrades listed, were all tested by us and carefully selected, so you know that whichever one you choose will work as intended.
Error processing API data.