The 3D printing comunity has debated extensively about the advantages and disadvantages of both resin and filament printers. The most usually discussed topics are related to the quality of the prints, the cost of the materials and the printing times of each technology.
It may also be the case that we need to print an object that requires some specific structural properties, such a tensile strength and resistance to impact, and we need to find out if resin parts are stronger or weaker than filament printed ones.
When it comes down to strength, FDM printed parts tend to be stronger than resin printed objects. This is both true in terms of resistance to impact and tensile strength. Almost all popular filaments like ABS, PLA, PETG, Nylon, and Polycarbonate outperform regular resin prints. It should nonetheless be mentioned that Tough Resin is stronger than ABS, PETG, and Nylon.
Resin vs Filament Tensile Strength Comparison
Tensile strength of different filaments and resins (mega Pascals)
Material | MPa |
Polycarbonate | 67 |
PLA | 64 |
Tough Resin | 55 |
PETG | 50 |
Nylon | 48 |
ABS | 38 |
Resin | 23 |
Tensile strength measures the amount of stress a specific material can take while being stretched to its breaking point. The tensile strength of the material is measured at the breaking point and will vary between different materials used to make an identical component.
This is a fairly common test conducted in most industries; however, in order to produce fairly accurate results, the actual build process must be considered and factored in as a variable.
The consensus is that 3D resin prints are not that impact resistant; besides, there is a big question mark about the ongoing curing of resin products periodically exposed to UV light. While on the other side of the scale, PLA is a relatively cheap low-temperature resistant material in a box labeled “last resort”.
These assumptions couldn’t be farther from the truth, and the truth is revealed in fair and precise testing. Here is a basic overview of tensile strength tests done on different FDM filament types, which were conducted by Airwolf 3D which conform with ISO 527* standards. A hook was made from different materials and put to the test.
*: These guidelines specify the general conditions for determining the tensile properties of thermoplastics under specified conditions.
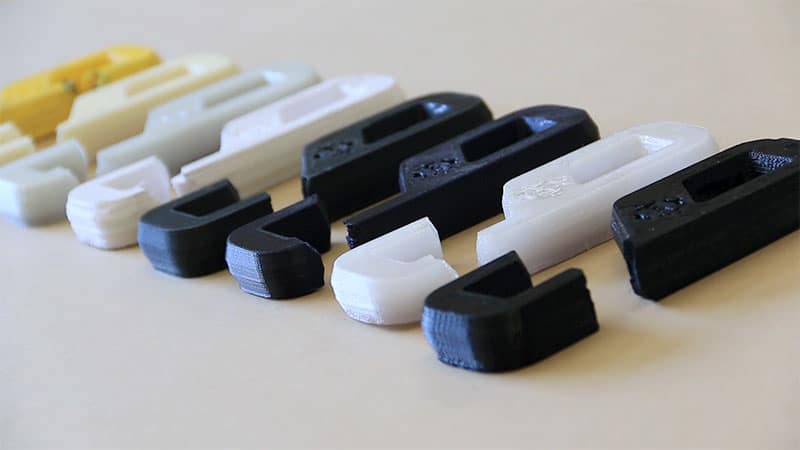
PLA
The print bed was set to 60°C and the hook was printed without an enclosure to keep the heat at a moderate level. The PLA hook managed to hold a weight of 285 pounds, which translates to a tensile strength of 64.4 MPa, but there is a catch as always.
PLA will lose its tensile strength over time and, as a result, should only be used for its designated purpose, which is to make toys and ornamental items, but not for purposes that require high tensile strength.
PETG
PETG measured at 50.0 MPa, which is surprising as one would expect it to be stronger than PLA. A different test conducted by toms3d.org put PLA up against PETG, but two test structures of each were printed to determine the effect of layer direction. The two samples were printed vertically and horizontally.
The test conducted was a bend test to determine the point where the sample snaps. The vertical printed samples were tested first, and this would also test layer adhesion. The PLA sample withstood just under 8kg while PTEG managed 5.9kg. The second sample tested material strength, and PLA measured 16.6kg, while the PETG sample did not fail since it didn’t break at all, but rather just bent.
Essentially, PETG is more flexible and won’t snap under certain forces like PLA would, but as far as tensile strength goes, PLA is stronger.
ABS
With the ISO 527 test, ABS was rated at 38.6 MPa, which is substantially weaker than both PLA and PETG. In the hook test, ABS did poorly and instantly snapped with the same 285 lb. load.
Although ABS is considered a real engineering material used in everyday applications, these applications do not require tensile strength. The tensile strength of ABS came in at 4700 psi (32.4 MPa).
Polycarbonate
In the basic hook test, polycarbonate filament was printed at high temperatures where the bed temperature should not be less than 145° C and the extruder temperature not less than 290°C.
It’s important to keep in mind that normal hobbyist printers cannot reach these desired temperatures. 685 pounds were suspended from the hook, which measured 9800 psi (67.6MPa), making polycarbonate the undisputed winner for tensile strength.
Nylon
Nylon is not a uniform filament, and as a result, different types of nylon filament have varying tensile strength, but the estimated strength is set at 7000psi (48.3 MPa), which is substantially better than ABS but below PLA. In the hook test, nylon 910 was used and printed at 250°C with a bed temperature of between 70-100°C. The nylon began bending, and only after hundreds of pounds did it give way at 485 lbs.
Essentially, similar to PETG, Nylon will bend more than PLA.
Resin
Although the tensile strength tests were not performed by the same people that did the previous tests, the same conditions were recreated, meaning that the results are not only valid but also comparable.
Resin is commonly known as a very weak material when it boils down to tensile strength, and the results are somehow in agreement with this notion. Regular resin only measured 23.4MPa, a value that is well below all filaments measured.
Despite the poor results for regular resin, I should mention that there have been incredible advancements in SLA printing, and tensile strength is definitely one dimension that received a lot of attention.
All major resin manufacturers also offer their “tough” resins, and it is not only a marketing tactic: take eSun’s tough resin with a tensile strength of 55MPa as an example.
This goes to show that manufacturers are putting great efforts into satisfying the requirements that the 3D printing industry is demanding in an always-increasing way.
Difference between regular resin and tough resin
Regular resin types are considered too weak to handle stress and are not recommended for outdoor use due to the continued curing process from the sun’s UV rays. However, there are resins on the market that have been formulated to be really strong.
There is fast-paced technology being introduced into resin development, and different applications are being discovered on an ongoing basis. Castable resins are being used in the manufacture of jewelry and are widely used in dentistry.
The main difference between regular resin and tough resin is tensile strength, with a tough resin having about double the tensile strength of regular resin.
Anycubic’s colored UV resin was selected as the regular resin that was tested against some tough resins, namely, Formlab’s Tough 2000, eSun’s Hard-Tough, and Siraya Tech’s Blu. The results were not surprising at all because the standard resin measured 23.4MPa while the tough resins measured 46MPa for Foamlab, 55MPa for eSun, and 44MPa for Siraya Tech.
As you can see from the test results, tough resins really are much stronger than the regular resin, but the results of the tests will not automatically translate into your projects. The main reason is structural design and application, so although tough resins are stronger, they will not necessarily reflect these test results.
Resin vs Filament Impact Strength Comparison
Impact Strength for different materials and orientations (Joules/Meter)
Flat | Horizontal | Vertical | |
Polycarbonate | 354 | 515 | 42 |
Nylon | 325 | 249 | 60 |
Prusa Tough Resin | 280 | 280 | 280 |
PETG | 239 | 178 | 35 |
PLA | 153 | 113 | 77 |
ABS | 129 | 149 | 55 |
Impact strength is different from tensile strength in that it measures how much impact a standard model can take and how much impact energy is absorbed from the force. The method used to conduct the test is the IZOD impact strength test. The tests were conducted using three different orientations, Flat, vertical, and horizontal orientated test samples.
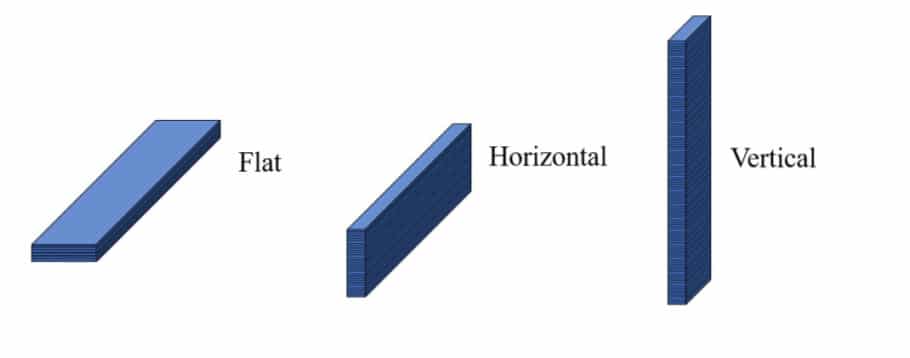
PLA
- Flat: 152.52 j/m
- Horizontal; 113.21 j/m
- Vertical: 77.42 j/m
PETG
- Flat: 238.98 j/m
- Horizontal; 178.09 j/m
- Vertical: 35.45 j/m
ABS
- Flat: 128.69 j/m
- Horizontal; 149.14 j/m
- Vertical: 55.14 j/m
Polycarbonate
- Flat: 354.15 j/m
- Horizontal; 514.90 j/m
- Vertical: 42.03 j/m
Nylon
- Flat: 324.90 j/m
- Horizontal; 248.86 j/m
- Vertical: 59.61 j/m
As you see from the results, there are mixed numbers among the filament types as well as the orientation of the test sample. PLA scored the highest on the vertical test with 77.42 j/m, with PETG scoring the lowest at 35.45 j/m. Polycarbonate and nylon test samples are pretty evenly matched, but polycarbonate scored 514.90j/m on the horizontal test, whereas nylon reached a score of 248.86 j/m.
Difference between regular resin and tough resin
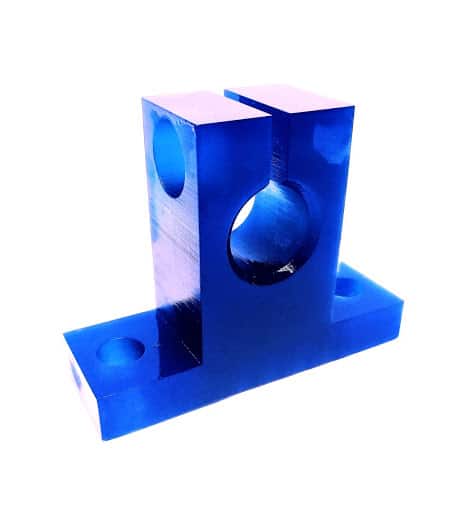
The impact strength of regular resin compared to tough resin was conducted using the IZOD impact strength test with Filaween scoring. In Tom’s test, he used Elegoo ABS-like clear red resin and the Prusa maroon “Tough” resin, and the results speak for themselves.
Being an isotropic material, the resin test samples only needed one sample each. The Prusa Tough resin result was 280mJ. This resin is comparable with PLA results.
What is the Strongest Filament?
I think it is a fairly common conclusion among manufactures, reviewers, and end-users that polycarbonate is rated as the strongest filament type.
When printed correctly and at the right temperatures, polycarbonate (or PC) can produce extremely strong and long-lasting components; however, printing with PC can be problematic as it doesn’t do well with overhangs and fine detail. PC has a high thermal resistance and is also fairly impact resistant, as shown by the test results above.
Nylon is also highly rated and compares favorably to PC. The nylon 910 filament tested by Airwolf showed great strength at 7000 psi, and a printed clip was able to hold 485 lb. MatterHackers did similar tests but used their own nylon filament called Nylon X filament. They printed a hook and could hold 364 pounds before it broke. Nylon has received great reviews, with many reviewers rating it much higher than PLA for strength and durability.
Because nylon is hygroscopic, meaning that it tends to absorb moisture, it does pose printing difficulties. It has to be 100% dry; otherwise, printing errors will occur. Another sore point is the printing temperature which must be between 220-270° C and is prone to warping. The good side of nylon is that it is impact resistant, fatigue resistant, heat resistant, and the cherry on the cake is that it is easier to print than PC.
Here are some recommended Nylon and Polycarbonate Filaments:
How to make an FDM part stronger?
A strong FDM print is a desirable print. There are several ways to increase the strength of your prints, including using rectilinear infill, reducing cooling, increasing extrusion width, increasing the number of perimeters, and using thinner layers. These pointers that will help you increase the strength of your FDM prints have been tried and tested by many 3D specialists and enthusiasts alike.
Use the Rectilinear or Honeycomb Infill Pattern
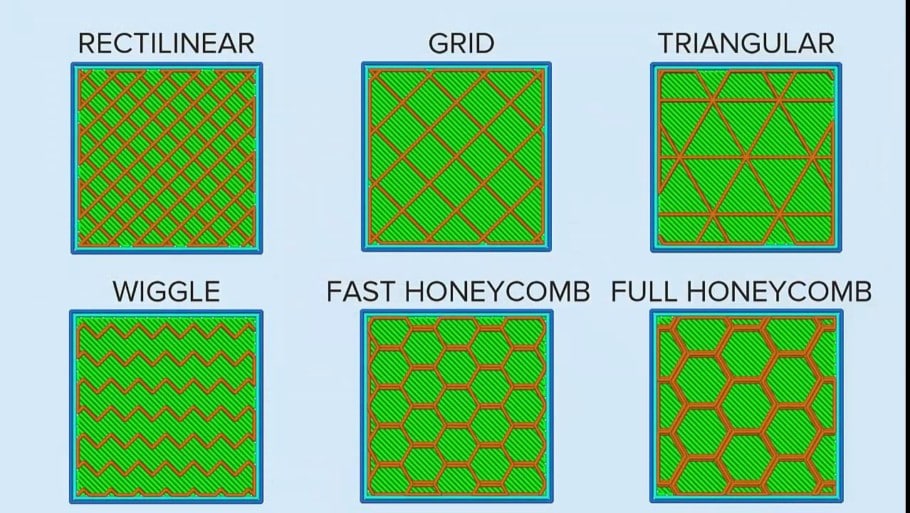
Infill patterns are a definite plus point to strengthening prints, but unfortunately, not one size fits all. The honeycomb structure is renowned for its strength and is even used in run-on flat car tires. From a technical point of view, the rectilinear pattern is the strongest pattern, but only when the direction of force is taken into consideration, as it will be weak in the opposite direction.
Using a rectilinear infill pattern saves on plastic use and prints faster as a result. It prints up to 30% faster than the honeycomb pattern. Where the rectilinear pattern is the strongest from one direction, the honeycomb is equally strong from all directions making it an all-round dependable pattern to use.
Anneal your 3D prints
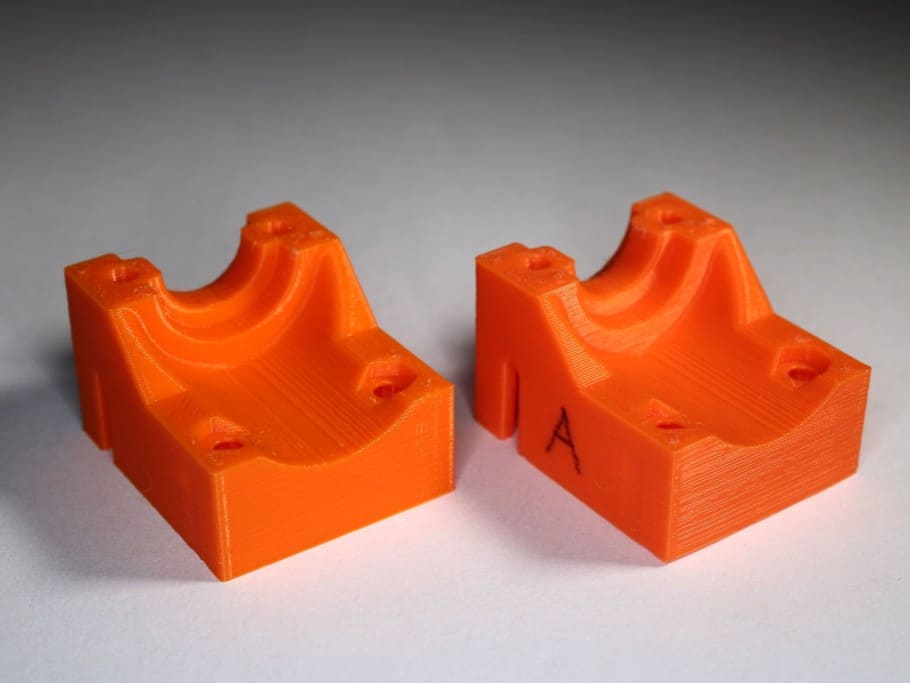
Annealing is a common process in the creation of metal or injected plastic parts. Simply put, it is a process of increasing temperature to improve firmness, tensile strength, and heat resistance. Although not so popular in the 3D printing world, the process is still applicable but will require a degree of experimentation to get the optimal temperature.
At home, you can place your prints in the oven, but you will have to monitor the temperature closely and make sure that there is an even heat distribution around the print.
Annealing is basically heating plastic to its glass transition temperature because, at this point, the object will still retain its form, but the molecules will be rearranged into a more fluid state, thus reducing inner tension and strengthening the structure in the process.
Polymers have long, repetitive molecular chains that are composed of amorphous and semi-crystalline molecular structures. These molecular structures make up the polymer and are randomly distributed with no definitive dividing lines. The crystalline structures are hard and rigid, while the amorphous structures are more elastic and flexible.
When the filament is heated up in the nozzle, it will likely be amorphous and will retain this structure through the rapid cooling process. What annealing achieves is changing the characteristics of the amorphous plastic into crystalline plastic.
PLA and PETG filaments showed promising results when annealed, while ASA and ABS showed no real change other than warping during the process. PLA filament showed great improvement in tensile strength while PETG scored big points for impact durability.
The bottom line is that annealing is an effective tool but may cause complications when using the technique with detailed prints.
Additional Considerations
You should consider the application of a print to determine its strengths and weaknesses. Besides the right filament or resin, several other considerations will impact the usefulness of your print.
Anisotropic vs Isotropic
Anisotropic is basically arriving at different values when a material’s properties are measured from different directions, which is the case with rectilinear infills. On the other hand, isotropic means consistent values no matter the direction of the measurement, and in this case, we can use the honeycomb structure as a good example.
With FDM 3D printing, the print or build direction will contribute to anisotropic results. This becomes more obvious with lower adhesion between layers in the Z-axis, which causes a lower pull strength compared to the X and Y-axis. So, if anisotropy is not considered, then the printed product will not last when pressure is applied to its weakness.
With SLA printing, there is no need to worry about structural weaknesses from certain directions because the resin is isotropic, meaning that the object has the same strength from all directions. For added strength resin model should not be hollow to save on resin.
Slicer Settings
A strong print begins with a good design that focuses on structural integrity by allocating more material to areas with concentrated stress. Topology optimization allows the process to be automated and is frequently used in creating functional designs.
The fabrication process also has a strong influence on the strength of the final product, and this is determined by the printing setting during slicing. For example, the layer height being higher will account for greater print strength, both in FDM and SLA prints. The infill structure and settings also contribute to the print strength, as do the speed, thickness of the extrusion, and optimum temperatures.
With SLA resin, printers usually print with 100% infill, but some slicers allow you to drain excess resin from interior pockets as a resin-saving option; however, in order not to compromise the integrity of the print, the design should not be hollow.
How the objects are printed
Layer thickness and adhesion play a dominant role in the overall strength of a printed object. In a test conducted to point out the effects of layer thickness and print orientation, several hooks were printed with different layer thickness as well as being printed vertically and laying down.
The results of the test were unanimously in favor of the hooks printed laying down, which indicates that structural integrity is influenced if the print layers are in the same line as the force applied to the object.
A 0.4mm nozzle was used for the printing, and the hooks were printed from 0.05 to 0.4mm. In both print orientations, the hooks that were printed with between 0.1mm and 0.2mm performed the best, whereas the 0.3mm and 0,4mm hooks performed the worst.
From this test, we can conclude that the layer thickness should not exceed half the diameter of the nozzle being if part strength is relevant for our application. For details on the test, check out the video from CNCKitchen
Check out our recommended products section
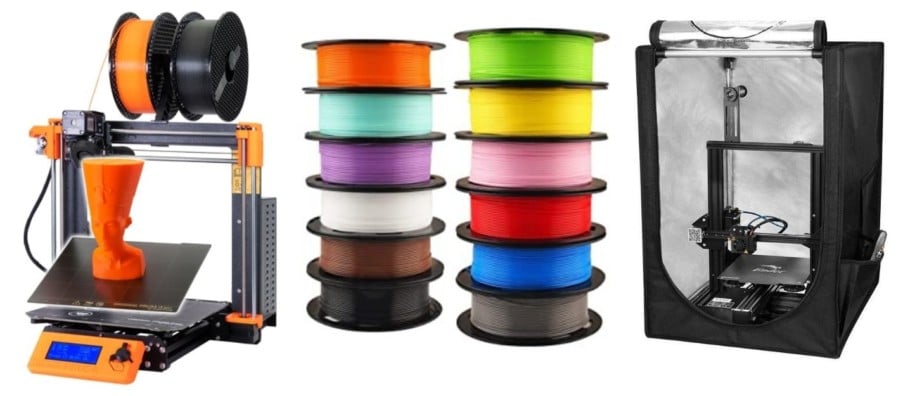
We created a recommended products section that will allow you to remove the guesswork and reduce the time spent researching what printer, filament, or upgrades to get, since we know that this can be a very daunting task and which generally leads to a lot of confusion.
We have selected just a handful of 3D printers that we consider to be good for beginners as well as intermediates, and even experts, making the decision easier, and the filaments, as well as the upgrades listed, were all tested by us and carefully selected, so you know that whichever one you choose will work as intended.
Error processing API data.
Hi Martin,
This was a very informative article. I’m totally new to 3D printer and I’m trying to decide on which printer would be ideal for printing jewelry.
Would you recommend resin for making jewelry? I think strength and tensile strength is important.
Can you recommend a printer. I need to make prototypes.
Thanks
Greg