3D printers create objects in an additive way, making the part as strong as its weakest layer. They are usually weaker than most other technologies, such as milling techniques, injection molding or resin pouring techniques.
There are many applications for which we have to take structural strength into account. Due to the way in which Fused Deposition Modelling (FDM) technology works, the parts that we obtain are not as strong as their respective injection molding counterparts.
However, do not despair, there are a number of considerations that we can incorporate to our designs and configurations in order to mitigate this drawback.
We can reduce these weaknesses by setting the right extrusion temperature, setting a higher infill percentage, building thicker walls, choosing the right material, and properly orienting the part on the build plate.
Why are 3D printed parts weaker?
The additive technique by which a 3D printer creates objects has an inherent tendency to output weaker parts when compared to other manufacturing processes because it deposits one layer of plastic on top of the other which bond together.
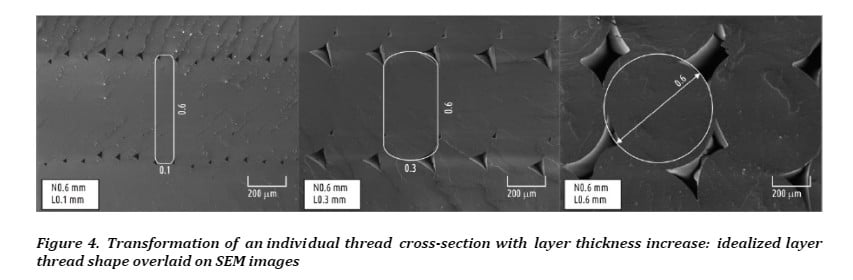
If we do not take the time to properly configure the settings of our print, we are willingly exposing ourselves to creating parts with weak layer adhesion.
Low temperatures, highly different temperatures between each layer and the previous one and other factors, may lead to very poor adhesion and overall weak parts.
Subtractive manufacturing, like milling, for example, does not have this problem since they start with a solid raw material that is carved into the desired 3D shape.
We can also create an object via injection molding. Using this technique, a molten material is injected into a mold where it cools and hardens taking the shape of the cavity. This process outputs solid and strong parts.
Now that you know about the inherent weakness of a 3D printer, you may feel the urge to toss your newly acquired appliance into the trash. Before you do that, I would highly recommend reading the rest of the article and learning some easy ways to make your parts stronger.
We should also consider that most of our parts won’t be used to build SpaceX’s newest rocket. We can afford to print a somewhat weaker Baby Yoda though.
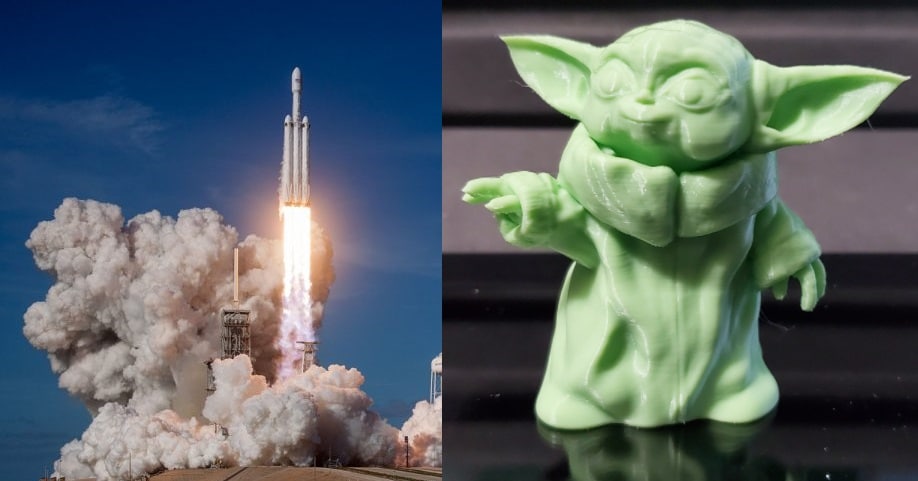
On the right: A Baby Yoda. Although cute, it may or may not be up to international quality standards.
How can we improve the strength of a 3D printed part?
As mentioned before, there are plenty of small configuration tweaks that we can use to make our part stronger in general. Among them, the most important ones are infill percentage, extrusion temperature, outer wall thickness, choosing the correct filament type and setting the properly orienting our design.
Let us briefly discuss each one of them and see how and why they affect our print!
Infill percentage
Infill consists of a regular pattern that is printed inside the object and replaces what would otherwise be an empty space. It works as internal support for the print, not only preventing the top from collapsing, but also holding the outer shell together.
Before we adventure into this soul-stirring topic, look at what different infill percentages look like:
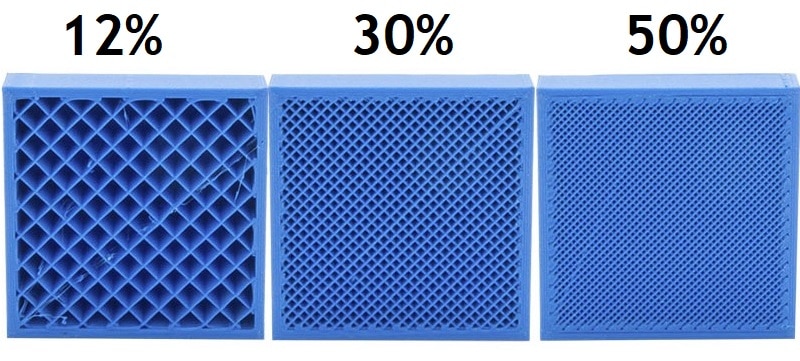
As a rule of thumb, an infill of 50% will greatly increase your print quality and strength. Higher infill percentages only show marginal strength increases, but greatly increase filament consumption and printing time.
You should also know we could configure our infill to follow different patterns, such as rectilinear, grid, triangular, wiggle*, fast honeycomb, full honeycomb and other experimental. The pros and cons of each pattern is out of the scope of this article, but you will mostly be fine with using rectilinear or grid infills.
*Up to date, I still cannot think of an advantage of the wiggle pattern. I guess there once existed a developer with some spare time and a taste for suboptimal shapes.
Wall Thickness
Wall thickness is the width of the outermost shell of our print and mostly determines the overall strength of it
Many filament manufacturers state that it is enough to print with 0.8mm outer shells to have a strong print, but I found that such thin walls usually produce weak prints. In order to obtain a resistant Baby Yoda, I highly recommend doubling the width to 1.6mm. The improvement in overall quality will be very noticeable.
Regardless of the wall thickness you choose to use, you should always go with a multiple of your nozzle diameter. I mentioned 0.8mm and 1.6mm because most printers come with a 0.4mm nozzle. An acute and sharp PhD in Mathematics will be aware of the incredible calculation I performed above!
Setting the right temperature
Although most filaments used in 3D printing are some kind of a thermoplastic, they have a different chemical composition. Therefore, they each have different optimal temperatures.
As a rule of thumb, PLA should be set to anywhere between 180 C° to 220 C°, ABS between 210C° and 250C°, PETG between 220C° and 250C° and Nylon between 240C° to 260C°.
If you bought another filament, look at its packaging and you will probably find the recommended temperature according to the manufacturer. In fact, forget the ranges I told you and always look at the manufacturers recommended range just in case.
You should always thrive to find the perfect temperature for your 3D printer and filament, since it will determine the quality of the layer adhesion.
Low extrusion temperatures lead to bad adhesion between layers. You may be tempted to go the other way and heat your filament as hot as possible, but that will get you into all sorts of new problems that you can google! Spoiler alert: messy prints, poor overhangs, and overall low quality.
But in general, if you’re looking to improve the strength of your print, setting the temperature slightly higher will make it so that the new layer of extruded plastic bonds much better with the previous one.
Part Orientation
It is always important to keep in mind that 3D printed parts are going to be strongest in the plane parallel to the printing bed and weaker on the vertical plane. When positioning your design within the slicer, always ask yourself in which directions it will be contacted and what forces it will be subjected to.
If you are not sure about the answer, consider the case of a boring and probably useless hollow cylinder*.
If you print it in the vertical orientation, the object will be a sequence of circles layered on top of each other. If you grab it at each extreme and try to bend it, it will be quite easy to break the cylinder.
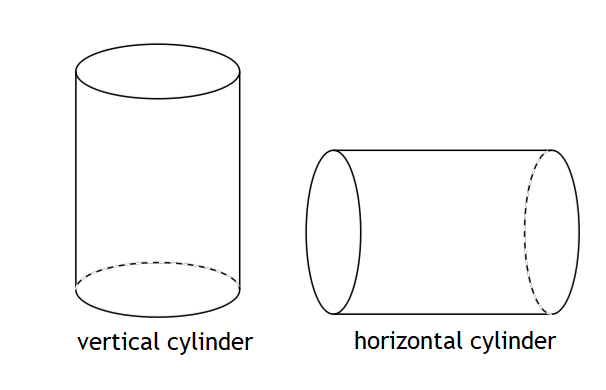
*I probably should mention that throughout history, cylinders have clearly proven to be useful. This is clearly out of the scope of today’s article, so I will leave the proof to the reader.
You may be tempted to think that you are incredibly strong, and maybe you are, but you should also be aware of the fact that you printed a very weak cylinder.
If you still have some spare filament and choose to print it in a horizontal orientation, you will notice that the part is harder to break because of how the lines of filament are extruded.
The disadvantage of this positioning is that you may have to add supports to the print because of the angles that this orientation created.
Why does everything have to be a trade-off in 3D printing? There is no free lunch in this hobby!
Use stronger filament
While this one may seem obvious, utilizing a different type of filament can do wonders in terms of overall strength.
However, not all printers are capable of printing with all the filaments that are out there, but there’s definitely some alternatives that you can use even on affordable printers, such as the Ender 3.
Polycarbonate and Nylon are regarded as the strongest filaments currently available, and if your printer can handle those and you need an extremely strong print, then print your object with those.
If you’re printing with PLA, try PETG since it’s easy to work with and is also a bit more flexible as well as much more heat resistant.
How to make 3D printed parts stronger
Here’s a quick summary on how to print your model in such a way that it’s strength will be increased:
- Choose a strong infill pattern (generally honeycomb).
- Increase the infill percentage (going over 50% will start yielding significant diminishing returns).
- Increase the wall or outer shell thickness.
- Increase the printing temperature in 5°C increments until you find the best one.
- Change the orientation of the print so that the layer lines are parallel to the forces that will be exerted on it.
Conclusion
As you can see, there are plenty of things we can do in order to improve our objects’ overall strength and overcome an inherent weakness of the technology we chose.
If the future of the world depends on you being able to print a strong Benchy but you do not have time to read the full article, just do the following.
Happy printing!
Check out our recommended products section
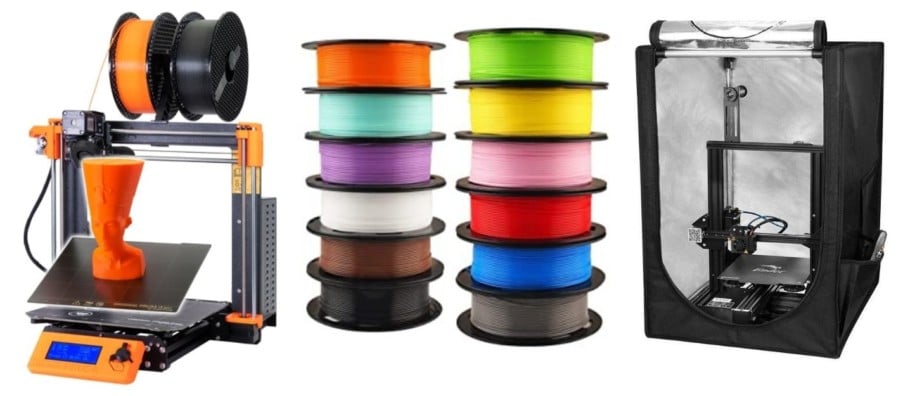
We created a recommended products section that will allow you to remove the guesswork and reduce the time spent researching what printer, filament, or upgrades to get, since we know that this can be a very daunting task and which generally leads to a lot of confusion.
We have selected just a handful of 3D printers that we consider to be good for beginners as well as intermediates, and even experts, making the decision easier, and the filaments, as well as the upgrades listed, were all tested by us and carefully selected, so you know that whichever one you choose will work as intended.
Error processing API data.