Infill patterns conform to the interior structure of a 3D printed part and they have a significant effect on your part’s print time, filament consumption, flexibility, strength, weight, and what it can be used for.
Most people make the mistake of assuming that these factors are only dependent on the number of shells/perimeters and the infill density, however, there is a good reason that Cura offers 13 different infill patterns since there is much to consider when choosing an infill pattern for a particular part.
Infill patterns have benefits, but also drawbacks. There are important factors to consider when choosing a pattern for your parts, such as strength, print duration, and flexibility of the finished product. These different properties can make one pattern more desirable than another depending on what you intend to do with the part afterward.
In this article, I will go over the different infill patterns that are available, when to use them (depending on the strength that the print requires), how to make a 3d print stronger, and more!
In Short; The combination of a rectilinear pattern with a 100% infill shows the highest tensile strength with a value of 36.4 Mpa. This is only true, however, if the forces applied follow the same direction as the infill layers. For most prints, the overall strongest pattern is honeycomb with an infill of about 50%.
The source for this information can be found in this 2016 study here.
Now, without any further ado, let’s get started!
- Different infill patterns and their use
- What infill pattern is the strongest?
- How do infill patterns and density affect printing time?
- Additional factors that can affect a prints' strength
- How to increase the Strength of a 3D Print?
- Summary: Infill for different print types
- Conclusion
- Check out our recommended products section
Different infill patterns and their use
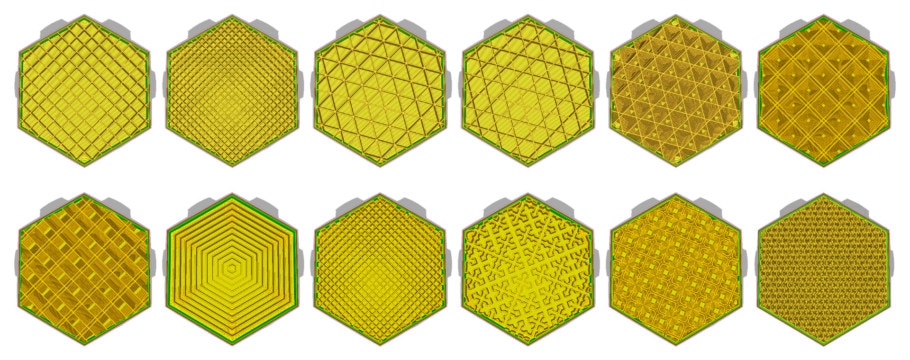
What sort of pattern you choose should depend on the needs of a particular part. So, here are the 13 infill patterns that are currently being offered by Cura and we will briefly discuss their advantages, and disadvantages and the rationale for using each of them.
Low Strength infill patterns (Lines, Zig-Zag)
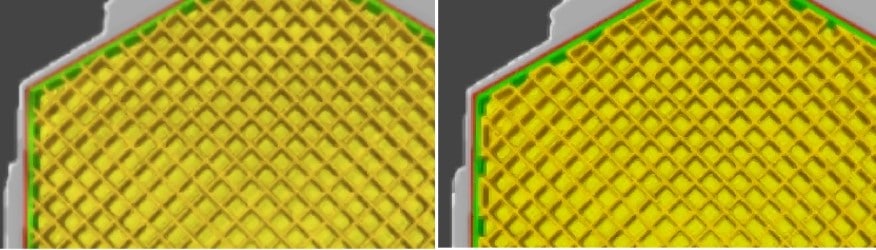
The difference can only be spotted by looking at the edges of both infill patterns.
Typical infill density: 0-15%
Lines: The lines infill pattern is a 2D infill pattern and as the name suggests, it consists of layers of horizontal lines. All the lines in the same layer have the same direction, but the angle between the lines of the successive layers is 90 degrees. In other words, these horizontal lines are printed along the X-axis and Y-axis of a 2D plane.
The lines infill pattern is recommended for printing test objects and prototypes because it consumes less material and has a quicker print time than most other patterns. This means that the parts are lightweight and can be buoyant on water. It is also suitable for printing decorative objects like figurines, and models.
The prints are moderately strong when compressed from the sides but because there is no structural support along the Z-axis, they don’t support much force in a vertical manner. This makes this pattern unsuitable for parts that are meant to experience even moderate mechanical forces.
Zig-Zag: The zig-zag infill pattern is quite similar to the lines infill pattern and has the same advantages and disadvantages, as well as use cases.
The only difference is the way a layer of lines is printed. In the lines infill pattern, a layer has more than one line and these are not connected with each other while in the zig-zag infill pattern, a layer consists of only a single continuous line. The difference can only be spotted by looking at the edges of both infill patterns.
Medium Strength infill Patterns (Grid, Triangles, Tri-hexagon)
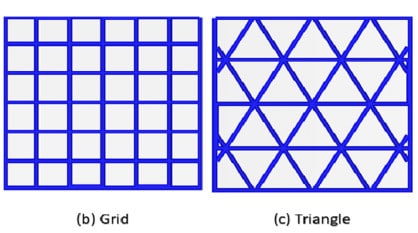
Typical infill density: 15-50%
Gird: The grid infill pattern is similar to the lines infill pattern, however, each layer consists of lines printed along the X-axis and Y-axis. This means that the lines on the same layer appear to have an angle of 90 degrees between them. This makes the layers look like a grid, and because of this, unlike the lines infill pattern, a single layer can have strength in two dimensions.
The gird infill pattern is stronger but consumes more material and has slower print times compared to the lines and zig-zag infill patterns.
Triangles: The triangles infill pattern consists of triangles that are fused together to form layers which are then stacked vertically. Unlike the former three patterns, where lines are only printed in two directions along the XY plane, the triangle pattern contains lines printed in three directions. This gives a uniform strength in every direction and is more resistant to outside forces.
Note that if you need a smooth surface, you will have to increase the number of outside layers or shells.
Tri-hexagon: The tri-hexagon infill pattern is a strong 2D pattern that is similar to the triangles pattern. The lines in each layer are also printed in three directions along the XY plane but in such a way that six triangles appear to be fused together to form hexagons that connect to form a layer.
High Strength Infill Patterns (Cubic, Cubic subdivision, Octet, quarter cubic, gyroid)
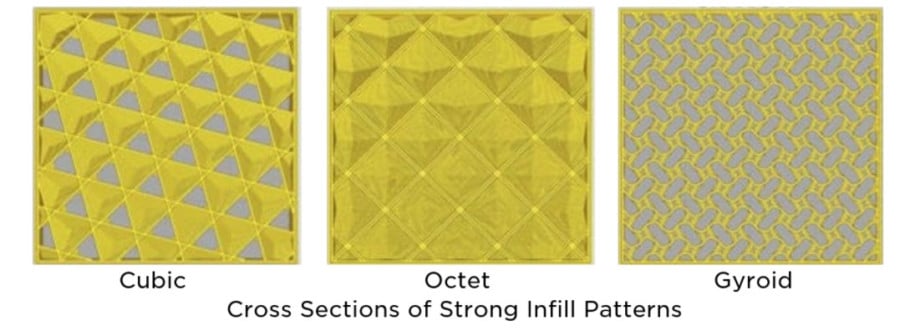
Typical infill density: >50%
Cubic: The cubic infill pattern is a strong 3D infill pattern that is made up of stacked cubes that are tilted in a 45-degree angle around the X-axis and Y-axis. This gives them the illusion of looking like triangles.
The cubic infill pattern is quite strong as it can handle pressure applied to the object from all directions, but it requires more material and has a slower print time. It can be used to print functional mechanical parts.
Cubic (Subdivision): The Cubic Subdivision pattern is quite similar to the Cubic pattern and has the same strength and use cases, but it requires less material to be printed. This is achieved by creating bigger cubes towards the middle of the print, and this way material is saved where infill does not experience a significant amount of external pressure.
However, this infill pattern is more time-consuming to slice than other infill patterns.
Octet: The octet infill pattern is similar to the cubic pattern except that instead of looking like triangles of increasing slopes, it looks like squares. Objects having the octet infill pattern are quite strong, can survive pressure from all sides, and have the ability to perform mechanical functions.
Quarter Cubic: The quarter cubic infill pattern is similar to other 3D patterns like the cubic and the octet and has similar strength and use cases. You can use it on 3D models even when the perimeter is very thin.
Gyroid: The gyroid infill pattern looks absolutely fantastic and it also has the highest strength to weight ratio. Its perforated structure makes it a permeable solid (can allow liquids or gas to pass through). Its print time and material usage are optimal, but be sure to do some testing if you ever want to print with a low infill density because the Gyroid structure needs support and has to be printed with a relatively high infill density.
Flexible Infill Patterns (Concentric, Cross, Cross 3D)
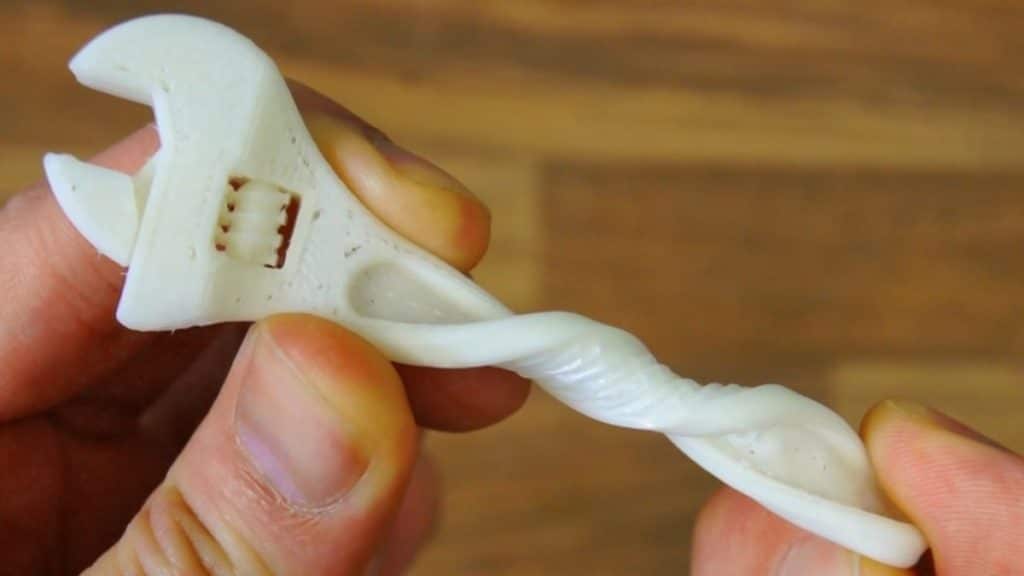
Typical infill density: 0-100% (Depending on how squishy you want the print to be).
Concentric: The concentric infill pattern contains concentric lines that are similar to the object’s shape (outline). The objects are flexible and can be twisted without experiencing any significant damage or deformation to the overall shape. This pattern consumes a relatively low amount of filament and has quick print time.
However, it is only suitable to print flexible objects and lacks horizontal strength.
Cross: The cross infill pattern is printed in such a way that it looks to be made out of fancy crosses and which have empty spaces that allow the prints to survive significant twisting and bending.
The disadvantage is that there is no structural support to counter forces that are exerted horizontally on the object.
Cross 3D: The cross 3D infill pattern is similar to the Cross pattern but is printed in such a way that as the print grows the lines move at inclines. It is easier to print and is ideal to print soft and flexible objects. The disadvantage is that it is weak and requires more time to slice.
What infill pattern is the strongest?

Source: Thingiverse.
Many people who have used 3D printers tend to recommend Honeycomb (Cubic) as the strongest infill pattern since-, while weaker in the direction of the forces being applied, it’s actually stronger than other patterns because it is equally strong in every direction as every little cell of honeycomb is as strong as the entire structure.
The hexagonal mechanisms in honeycomb cells are structured to diffuse and distribute force, and instead of having its force concentrated on just one or two points, the honeycomb pattern spreads out that force over a larger area. By re-distributing the force to all the parts of the structure, honeycomb is better able to handle general mechanical forces than any other pattern.
The honeycomb (Cubic) infill pattern makes prints strong and rigid, even in big, solid prints. The increased strength allows you to create parts with big structures and that have many advantageous mechanical properties when compared to other infill patterns.
From a theoretical perspective, the rectilinear infill is the strongest pattern, if the applied force is in the direction of the lines of the infill layers, that is. Otherwise, it is a relatively weak pattern, but it is also remarkably efficient in terms of plastic use, and therefore prints roughly 30% faster than honeycomb.
In short; The strongest infill pattern for most situations is the honeycomb (Cubic) pattern since it’s able to distribute the forces coming from any direction through the whole structure. The Rectilinear pattern is the absolute strongest, but only if the forces are applied in the same direction as the infill.
How does infill density affect strength and what is a good density range?
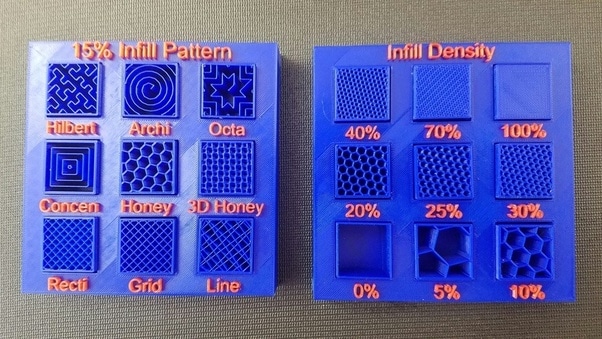
Source: Quora.
Another factor of strength is infill density, because the denser the infill percentage, the stronger the part.
If you consider the strength of an object, it is directly related to its structure: The greater the infill percentage the more material there is in the middle of a part for outside forces to deal with, and therefore, the stronger its resistance to breaking.
Because it provides the most sturdy, reliable structure, 100% infill is the best. However, printing will take much longer due to the amount of material being used, and it will also cost more since it takes more filament than lower infill alternatives.
Many people are satisfied in most cases with an infill density of 20-50%, which gives the best results with most infill patterns and you will be surprised to know that a filament percentage of 50% may already give you the same strength as 100%, or very close to it, in some cases.
Don’t expect a drastic increase in strength after increasing the infill density beyond 50% since this is where you will start to get significant diminishing returns. The higher the filament percentage, the less and less effective the increase becomes.
It’s probably not necessary to print your parts above 75% infill density as it just wastes extra filament and makes the parts heavier, unless you’re printing gears.
Pro tip: Optimize infill line orientation to make the print more resistant: The default orientation of infill lines is 45°, and you can make significant improvements in strength with the same percentage and pattern of the infill by just adjusting the infill lines orientation in a specific way (depending.
How do infill patterns and density affect printing time?
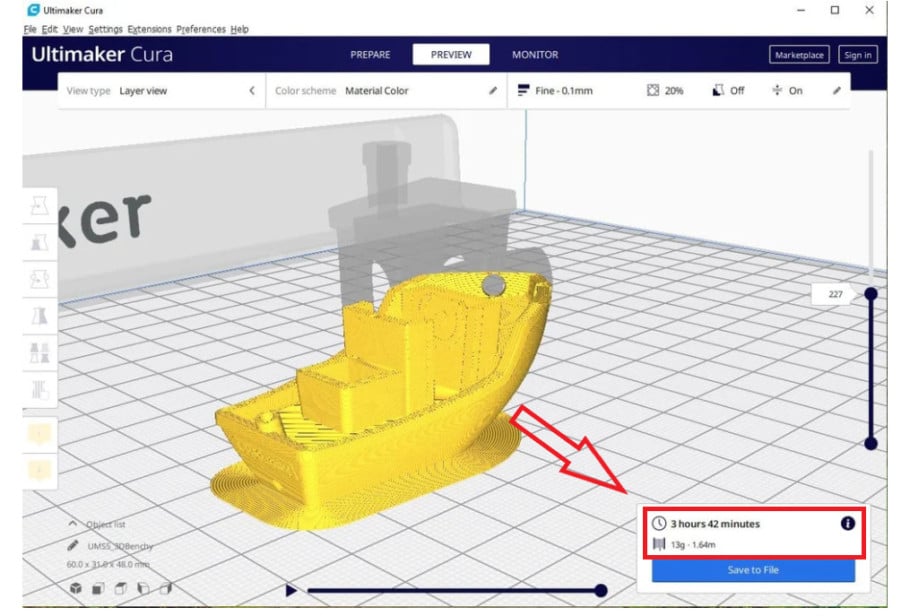
Varying the infill percentage and the pattern can affect strength, material usage, print time, and other aspects of your object’s performance. Every increase in strength usually means you have to sacrifice cost and print times.
The key to using infill percentage and pattern successfully is finding the sweet spot that lies somewhere between too weak and too expensive. This is the only way to minimize cost and print times and maximize strength.
It can be tough to customize infill settings from different densities, patterns, styles, and orientations, but when you use the right one for your job, printing can become a cakewalk.
What is the fastest Infill to print with?
The simplest infill pattern to print, and therefore the fastest one, is the “lines” infill. It’s also the most popular one for the sole reason that it cuts down print time significantly when compared to other patterns and that it still provides some decent strength to the objects.
Additional factors that can affect a prints’ strength
While this article may be mainly focused on infill patterns, there are a couple of additional factors that can affect a prints’ quality, such as filament type, filament quality, how the part is actually printed, the number of the perimeters, layer height, and more.
Filament type
There are dozens of different filaments (PLA, ABS, PETG, HIPS, Polycarbonate, Nylon, and many others) and they all have their advantages as well as disadvantages.
PLA, for example, is very easy to print with but can’t withstand high temperatures and should not be used to make prints that you’ll be leaving outdoors.
Nylon is known for being a fantastic filament to print gears with since it’s extremely resistant, and polycarbonate is the strongest filament of all, as far as tensile strength goes.
Essentially, you will need to choose the material according to it’s intended use.
Filament Quality
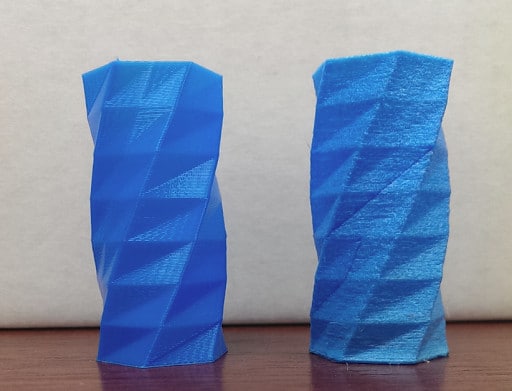
Right: Wet Nylon.
While most types of filament are nowadays made more than decently, making sure to get a filament spool from a reputable brand will increase your chances of printing successfully and having a print that will be functional without failing too soon.
Just note one thing: Filament can get easily damaged, especially if it absorbs humidity, which most of the filaments will do and in no time, so you should learn how to store them and to take care of them properly.
To learn more, check this post we wrote about how to tell if filament has gone bad, how to store it, and how to dry filament that has absorbed humidity.
Print Orientation
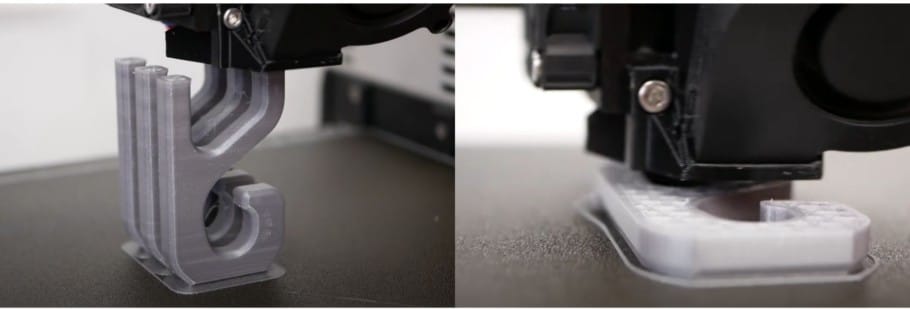
Right: Hooks printed Horizontally = Stronger layer adhesion and therefore more resistant.
When I first found out about this, I have to say that I was surprised… even though it’s really obvious once you think about it!
The weak points of a 3D print are always its layer lines, which means that printing an object vertically (which essentially means that the layers will be printed in a horizontal manner) will yield a much different result in strength than if you printed the model horizontally, or on its side.
CNC Kitchen did a comparison between printing hooks in a standing orientation as well as in a horizontal orientation and the results in overall strength difference were quite fascinating:
Since printing a hook vertically means that the layers are printed horizontally, and that layer adhesion ends up being much weaker when exerting a pulling force the hook, it ends up breaking far easier than the one printed horizontally (with only have as much force being applied).
This doesn’t mean that you should always print your models on their side, but rather think about what the use of the model is going to be and print it in such a way that the forces applied to it will be in the same direction as the filament.
Number of perimeters
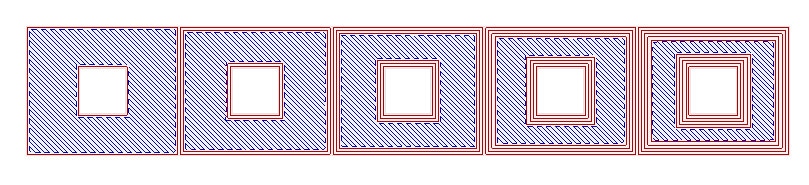
Perimeters are the outer part of the print, the part that we see, while infill is on the inside to keep the print from collapsing.
Perimeters, also known as shells, have a major impact on strength, in fact they are a lot more important than infill in most cases; Just adding an additional perimeter can increase the strength of the print by the same amount as adding 10%-15% infill would do.
Layer Height
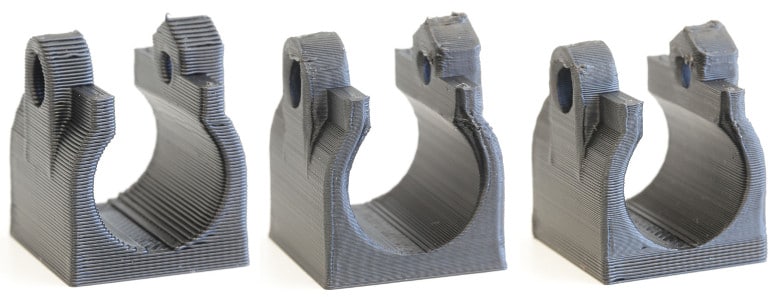
Generally, the lower the layer height, the more adhesion there will be. If you cut open a print perpendicular to the layer lines, if it was printed with a really thick layer height, there would be visible gaps between the filament layers, which will weaken the part.
On the other hand, a lower layer thickness will ensure that all the different layers are adhering properly. However, this is only up to a point, since going below 0.1mm will lower a print’s strength.
Essentially, the strongest layer height is 0.1mm or 0.12mm, going above or below this value will lower the print’s strength.
How to increase the Strength of a 3D Print?
Aside from adjusting the layer height, infill percentage, printing the object with a different orientation, and all the steps I just mentioned, you can also anneal the print, which consists in heating the entire printed object to its glass transition temperature so that it slightly “melts”, which changes the molecular structure of the filament and also helps the layers adhere even better.
If you want to learn more about how the annealing process works, then check out this article.
Summary: Infill for different print types
I already mentioned all of this information earlier, but here’s just a quick rundown of what infill- percentage and pattern you should use depending on the type of object you’ll be printing.
Parts that need to be strong and resistant
- Infill Patterns: Cubic, cubic subdivision, octet, quarter cubic, gyroid
- Infill Percentages: 50-75%
Regular prints
- Infill Patterns: Grid, triangles, tri-hexagon
- Infill Percentages: 15-50%
Models, figures, and miniatures
- Infill Patterns: Lines, zig-zag
- Infill Percentages: 0-15%
Flexible prints
- Infill Patterns: Concentric, cross, cross 3D
- Infill Percentages: 0-100% (depending on your preference for squishiness)
Conclusion
As I mentioned, the strongest infill patterns are rectilinear and honeycomb, with the latter one not being as strong in terms of tensile strength but stronger in every other regard.
Don’t forget that there are many other factors influencing the strength and resistance of your print, so keep those in mind as well!
I hope this information was useful!
Have a great day!
Check out our recommended products section
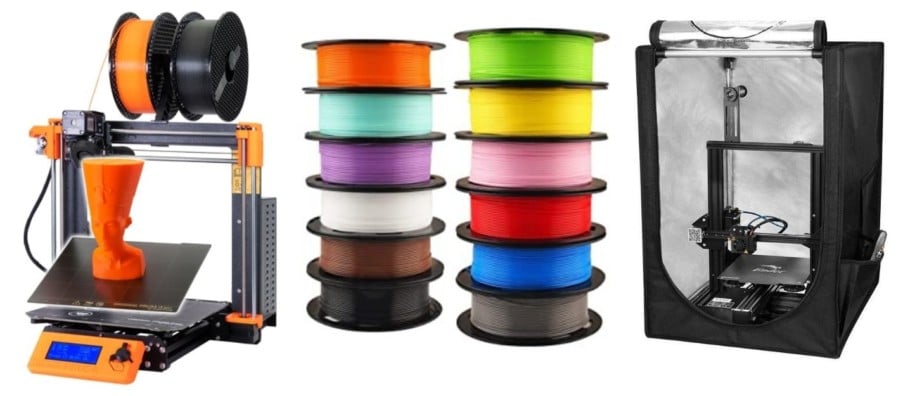
We created a recommended products section that will allow you to remove the guesswork and reduce the time spent researching what printer, filament, or upgrades to get, since we know that this can be a very daunting task and which generally leads to a lot of confusion.
We have selected just a handful of 3D printers that we consider to be good for beginners as well as intermediates, and even experts, making the decision easier, and the filaments, as well as the upgrades listed, were all tested by us and carefully selected, so you know that whichever one you choose will work as intended.
Error processing API data.
There is a lot of good information here. I am new to 3d printing and really appreciate all of the good information that has been provided.