Having a well-tuned slicer profile is crucial for succeeding in 3D printing. Although the number of different slicing parameters can be daunting, the most important ones aren’t really all that many and getting a hang of what each of those settings does will help you produce much better prints over time.
If you don’t want to have to go through all the trial and error that we did in order to find the Ideal Settings for creating high-quality prints on your Ender 3, then definitely check out our own Cura Profiles tailored specifically for the Ender 3 Printer Series.
Different settings and their Importance
When starting with 3D printing you should only really focus on a few parameters. Once you master the main settings you can continue with the vast number of advanced features that the different slicers offer. Below you’ll find an explanation for each of the parameters that you shouldn’t ignore.
Use the Standard Cura Profiles as a starting-off point
Cura offers different profiles for most filament types (PLA, ABS, PETG, TPU, etc.) and these come with settings that generally work quite well. Then simply adapt the print settings of that profile to suit your needs.
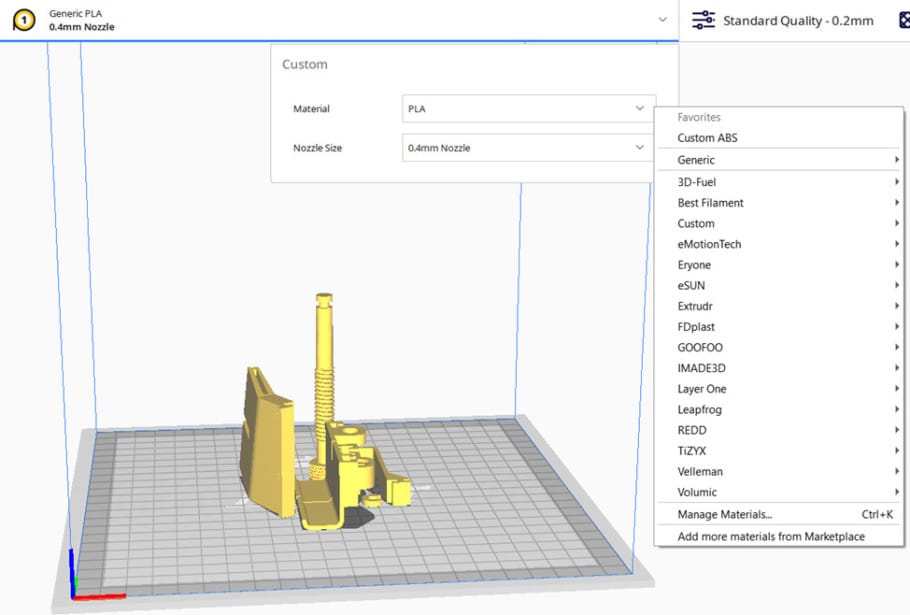
Printing Temperature
The most common 3D printing technology today is based on melting plastic filament and depositing in an organized manner. Filaments are made from different polymers that have different melting temperatures so extrusion temperature depends on what filament you choose. In thermoplastics melting temperature isn’t fixed as it is with water for example. With polymers, there is a temperature range where it starts to flow, and it becomes less viscous the higher the temperature is increased.
Getting the temperature just right lets you push plastic through the extruder but without uncontrolled dripping. Then there’s also the question of what happens once the material is deposited and how strongly it bonds with the previous layer. This depends on the extrusion temperature and the part cooling.
Ideal printing temperatures are a starting point as you should find out which one is the best for your combination of filament and printer. Every manufacturer has its own blend hence the different optimal extrusion temperatures. There can even be differences between spools from the same manufacturer if the fabrication process isn’t carefully controlled.
Ideal printing temperature for the most common materials:
- PLA: 200 – 210 ºC
- ABS: 230 – 240 ºC
- PETG: 220 – 230 ºC
- TPU: 220 – 240 ºC
Bed Temperature
A heated bed has become a staple in 3D printing. Getting the bed temperature right greatly increases your chances of success. There are many print surfaces available in the market that also help to get a good first layer, retain the part while printing and release it when cooled down.
As it is with extrusion temperatures, ideal bed temperatures should be only a starting point to test your specific setup and filament choice.
Ideal Bed temperature for the most common materials:
- PLA: 50 – 65 ºC
- ABS: 90 – 110 ºC
- PETG: 70 – 85 ºC
- TPU: 50 – 65 ºC
Layer Height
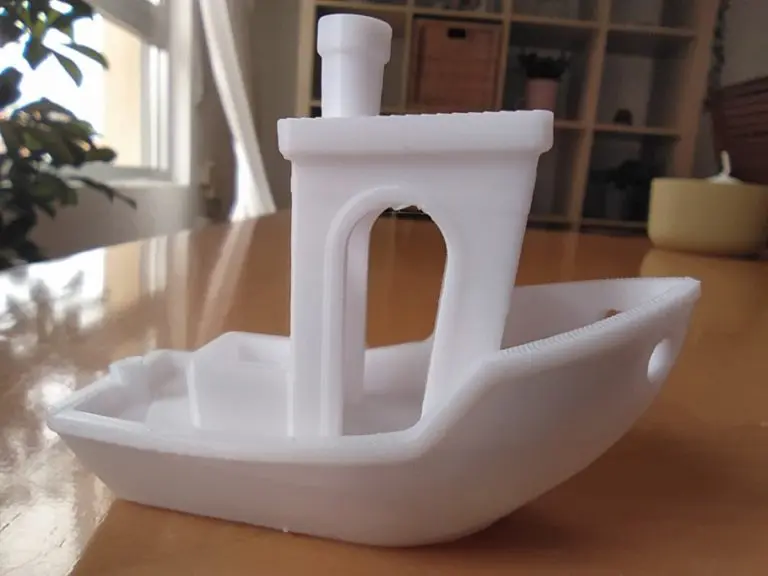
Layer height theoretically could be set to any thickness, but the mechanical construction of each printer makes some thicknesses better than others. The set of best layer heights are commonly known as “Magic numbers”. On Ender 3, for example, layer height goes up in multiples of 0.04 mm (0,08, 0,12, 0,18, etc.).
Layer height drastically influences print time, detail, and strength. With bigger layer heights print time decreases but detail and strength decrease as well. Choosing the right number for each print depends on what is the purpose of the print. Nozzle size also limits the layer height. It is recommended not to use layer height over 80% of the nozzle size. A sensible range would be 0.1 to 0.3 for a 0.4 nozzle.
For more information about layer heights, check out our article on the topic
Ideal layer heights for ender 3:
- 0.12 mm to 0.28 mm
Retraction
When the printer needs to stop extruding just stopping to advance the filament isn’t enough. Molten plastic would continue to drip because of the pressure build-up on the nozzle. To move the printhead without depositing any plastic the extruder must retract the filament. On Bowden printers like stock Ender 3 this phenomenon is more pronounced. When retraction isn’t finely tuned, stringing appears. If retraction settings are too aggressive the filament can become chafed and generate another set of problems.
There are a few parameters to modify to tweak retraction.
- Retraction distance is how much filament is pulled. In Bowden setups, this distance tends to be higher (3 mm – 6 mm).
- Retraction speed is mostly limited by the extruder, it is best to start low (20 mm/s) and move up testing it with a stringing test.
- Maximum retraction count specifies the number of retractions that can be made along a segment of filament. 5 to 10 would be best.
There are also a few features that can help with stringing or other artifacts that come from oozing:
- Combing: Turns off retraction and modifies travel moves to go over the infill to deposit any plastic that oozes out. May not always be recommended for every print.
- Wiping: Makes a short travel move inwards before traveling to another place.
- Coasting: Turns of extrusion for the last millimeters of a print line.
For more information about retraction and calibration models, we wrote this article.
Ideal retraction settings for the most common materials (PLA, ABS, PETG):
- Retraction Distance: 6 mm
- Retraction Speed: 20 mm/s
- Maximum Retraction Count: 5
The retraction distance should be set to 0mm when printing with TPU.
Infill
Each layer of a printed part is composed of outer walls and infill.
Different infill patterns and densities affect mostly printing times and, in certain situations, strength too. Slicers now have a lot of different patterns to choose from but the differences they bring are tied to the purpose of the print. Infill is mostly there to support the upper layers so unless the part is subject to compression forces, the best way to get stronger parts is to increase wall thickness, not infill density.
The general recommendation is to stick to simple patterns and 5% to 20% density.
If the part will be withstanding compression or crushing forces, you should consider 50% or more but for other cases, strength won’t increase a lot with density over 25%.
More information about infill settings:
Printing Speed
Printing speed is the maximum speed at which the printer moves for each type of movement. It is important to note that maximum print speeds aren’t achieved when prints are small or with high levels of details. This is because the printer spends the first and last part of the move accelerating and decelerating so unless accelerations are really high, the peak speed isn’t achieved.
Higher print speeds correlate to lower print quality and other problems. The recommendation if you want to increase the speed, is to do it on infill or inner walls that impact less on print quality. Travel moves can also benefit from higher speeds up to a point.
More information here: https://3dsolved.com/3d-printing-speed-vs-quality/
- ASA: 20 – 50mm/s
- ABS: 40 – 80 mm/s
- PETG: 40 – 90 mm/s
- PLA: 30 – 90 mm/s
- NYLON: 40 – 60 mm/s
- HIPS: 25 – 55 mm/s
- TPU: 10 – 30 mm/s
Initial Layer
The first layer is arguably the most important one and its success determines the success of the whole print.
The first layer must compensate for slight misalignments or unevenness so my recommendation would be not to go below 0.2 mm unless you know your printer is calibrated far beyond that.
To get the first layer right speed must be reduced and fans turned off. This ensures a good bonding to the bed.
The next two or three layers should be slow and without fan too to be sure that no stresses are added to the first layer.
- Initial layer speed: 20 mm/s
- First layer fan: 0%
- Number of layers without fan: 3 – 5
Support Overhang Angle
Each layer needs something underneath to stick to, it may be either the bed or a previous layer. On overhangs what happens is that the printer tries to deposit plastic in midair, and it curls back. Most printers can get away with 45º angle overhangs, but some can do even 60º. You can test your printer with an overhang test like this one.
To prevent printing without something underneath, the slicer generates a structure below that is called support. These structures must be then removed from the part in post-processing. The extra hassle is
- Support overhang angle: 45º
Bed Adhesion
Bed adhesion can be a problem for some models even if your fist layer is perfect. Long or pointy fist layers tend to curl up for example. Unless you have a print surface that is prepared to print without a separation layer of glue, hairspray, or specially formulated lacquers you should definitely use one. These products help the plastic bond to the surface and after printing can also act as a release agent when cooled down.
Activating brim can be a good solution. It creates a one-layer thick border that increases contact with the bed. It must be removed in post-processing so if you don’t need it, it’s easier to avoid it.
Raft acts in the same way but is composed of at least two or three layers and it can also help compensate any unevenness of the bed. You can find more information about bed adhesion here
Flow Rate
Flow rate is the speed at which the printer extrudes plastic. This speed is calculated by the slicer for each movement and generally must be set at 100%. It can be tweaked if you notice over or under extrusion, but my recommendation is not to test it in increments of more than 5%.
Flow rate can be helpful in finely tuning extrusion rates for different spools. As each polymer has a different hardness, the gears in the extruder engage differently. A good practice is to print a calibration cube and adjust the flow rate for each new spool of filament until you don´t see any over or under-extrusion. Then you must remember to save your settings or enter them every time you use each spool.
Ideal Ender 3 Printing settings for each filament type
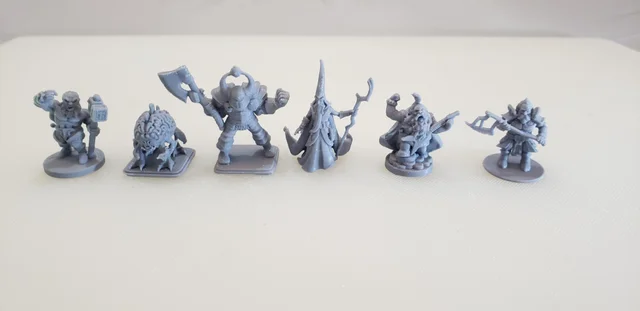
Here are some settings that are good starting points for Ender 3.
Ender 3 Settings for printing PLA
- Printing Temperature: 200 – 210 ºC
- Bed Temperature: 50 – 65 ºC
- Layer height: 0.12 mm (fine) – 0.28 (draft)
- Retraction: 6 mm
- Infill: 5% – 25%
- Speed: 30 – 90 mm/s
- Initial Layer Speed: 20 mm/s
- Initial Layer Height: 0.2 mm
- Initial Fan speed: 0%
- Fan speed (after the initial layers): 100%
- Support overhang Angle: 45º
Ender 3 Settings for printing ABS
- Printing Temperature: 230 – 240 ºC
- Bed Temperature: 90 – 110 ºC
- Layer height: 0.12 mm (fine) – 0.28 (draft)
- Retraction: 6 mm
- Infill: 5% – 25%
- Speed: 40 – 80 mm/s
- Initial Layer Speed: 20 mm/s
- Initial Layer Height: 0.2 mm
- Initial Fan speed: 0%
- Fan speed (after the initial layers): 0 – 30%
- Support overhang Angle: 45º
Ender 3 Settings for printing PETG
- Printing Temperature: 220 – 230 ºC
- Bed Temperature: 70 – 85 ºC
- Layer height: 0.12 mm (fine) – 0.28 (draft)
- Retraction: 6 mm
- Infill: 5% – 25%
- Speed: 40 – 90 mm/s
- Initial Layer Speed: 20 mm/s
- Initial Layer Height: 0.2 mm
- Initial Fan speed: 0%
- Fan speed (after the initial layers): 30% – 100%
- Support overhang Angle: 45º
Ender 3 Settings for printing TPU
Regular TPU can be printed without modifying the printer, but to print really flexible TPU such as NinjaFlex, you will either need to convert the Ender 3 into a direct drive printer or install something like the EZRStruder.
- Printing Temperature: 220 – 240 ºC
- Bed Temperature: 50 – 65 ºC
- Layer height: 0.12 mm (fine) – 0.28 (draft)
- Retraction: 0 mm
- Infill: 5% – 25%
- Speed: 10 – 30 mm/s
- Initial Layer Speed: 20 mm/s
- Initial Layer Height: 0.2 mm
- Initial Fan speed: 0%
- Fan speed (after the initial layers): 0% – 30%
- Support overhang Angle: 55º
If you don’t want to have to go through all the trial and error that we did in order to find the Ideal Settings for creating high-quality prints on your Ender 3, then definitely check out our own Cura Profiles tailored specifically for the Ender 3 Printer Series.
What about Nylon and Polycarbonate?
Ender 3 can print nylon and polycarbonate if you make a few upgrades. Check out our article for more information.
Conclusion
Having a well-calibrated slicer profile is key in 3D printing. Although you should always test which are better for your particular setup, if your machine is a widely used one such as Ender 3, you can get exceptionally good starting points from other users and manufacturers that will make the process easier.
Check out our recommended products section
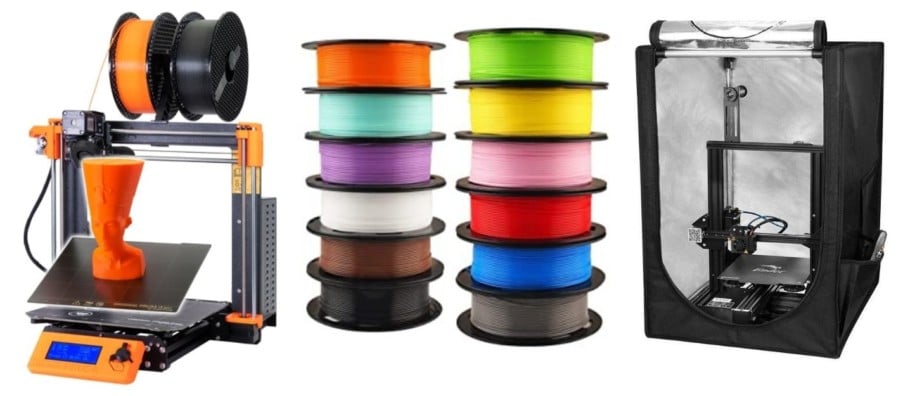
We created a recommended products section that will allow you to remove the guesswork and reduce the time spent researching what printer, filament, or upgrades to get, since we know that this can be a very daunting task and which generally leads to a lot of confusion.
We have selected just a handful of 3D printers that we consider to be good for beginners as well as intermediates, and even experts, making the decision easier, and the filaments, as well as the upgrades listed, were all tested by us and carefully selected, so you know that whichever one you choose will work as intended.
Error processing API data.