When I got started in 3D printing, I initially got a feeling of knowing almost everything there was to know in 3D printing. Shortly after, as can be explained by the Dunning-Kruger Effect, I learned that I actually only had a very superficial and weak grasp of the subject. The humbling experience occurred when I printed my first functional object that required multiple parts, each with its own requirements. That’s when I started reading about the different thermoplastics and their different characteristics.
So, in this article I’ll go through the common parts of a typical RC and their recommended filament types.
The recommended filament for an RC depends on the specific part of the object. When printing a chassis, it is best to print with ABS, whereas PETG is best for printing the body. Due to their inherent flexibility, TPU and Nylon are the most suited thermoplastic for printing wheels and bumpers respectively, and springs also yield the best results when printed with Nylon.
The following table summarizes the key concepts and recommendations that I lay out in the article.
RC Part | Characteristics | Recommended Filament |
Chassis | – Tensile Strength – Impact Resistance – UV Resistance | ABS |
Body | -Impact Resistance -UV Resistance | PETG |
Wheels | -Flexibility -Wear Resistance -Resistant to common chemicals | TPU |
Bumpers | -Impact Resistance -Some flexibility | Nylon |
Srpings | -Some Flexibility -Wear Resistance | Nylon |
Choosing the right filament for printing an RC Car’s Chassis
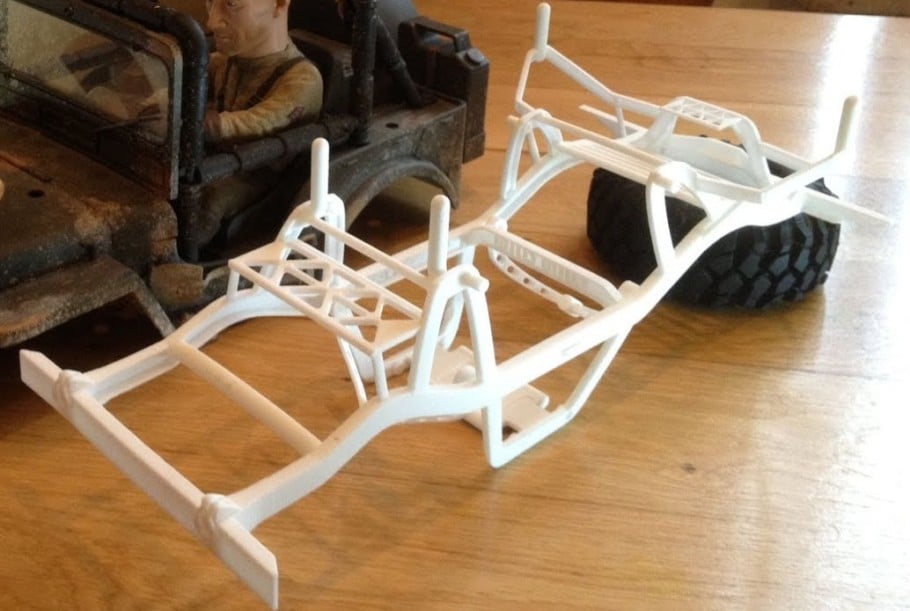
The biggest requirements for an RC car chassis are strength, impact resistance, and UV resistance. If one of these elements is not considered, then rest assured the car will have a short lifespan.
RC cars are constantly involved in collisions and are mostly used outdoors in varying weather conditions where they are exposed to both wet and dry conditions and UV rays. Strength must be looked at objectively as the chassis must be rigid but with a degree of flexibility as this will help greatly in absorbing impact.
Practical limitations of filament type should be strongly considered, and a selection made on this basis for the different parts that are each subjected to different stress levels. For example, exposed parts like body parts should be UV resistant, and components like bumpers and tires should have a higher flexibility level to absorb impact.
ABS
ABS is a very popular filament, mostly due to its strength and temperature resistance. It is also rigid and durable, but it does lack the UV resistance that will allow for a longer lifespan. Compared to PLA, ABS can withstand higher temperatures. As far as impact resistance goes, ABS is highly rated and is thus recommended for a number of different applications.
ABS printing has its share of speed bumps (no pun intended) and is not considered an easy filament to work with. The changing temperatures during the printing phase can cause parts to warp, so care must be taken to avoid this common issue. ABS also produces bad odours and is toxic during printing, so adequate ventilation is required in the printing area.
The extrusion temperature is between 220°C and 250°C with a bed temperature of between 90°C and 115°C. As we also remind our readers, ABS definitely requires a heated bed and an enclosure!
Having mentioned the difficulties of printing with ABS, it remains a popular filament and can provide acceptable results with the correct calibrations. ABS is best used for RC car parts that do not get exposed to a great deal of sunlight, such as the internal parts and possibly the chassis or undercarriage.
Polycarbonate
Polycarbonate is the ideal filament for strength. However, it is not practical to print with. Its tensile strength is in the region of 9.800 PSI* and can withstand weights of up to 685 pounds, but it requires an extrusion temperature of 260°C and a heated bed of approximately 110°C.
Greenhouse polycarbonate filament can withstand UV radiation from 5 to 15 years before degradation begins setting in. Due to the printing challenges, polycarbonate remains out of the scope of the 3D hobbyist.
*ABS has a similar tensile strength, whereas PLA only resists around 7.000PSI.
Why I prefer ABS for printing an RC Chassis
ABS is preferred over polycarbonate despite its lack of UV resistance. This recommendation is mostly due to hobbyist printers not being able to maintain polycarbonate printing temperatures.
You will note that the temperature scales do not differ much, but most entry-level 3D printers have a threshold of what maximum temperatures can be maintained. Polycarbonate is the ideal filament to use as it has a high UV resistance level and its strength and impact resistance are more than adequate for RC car requirements.
Choosing the right filament for printing a RC Car’s Body
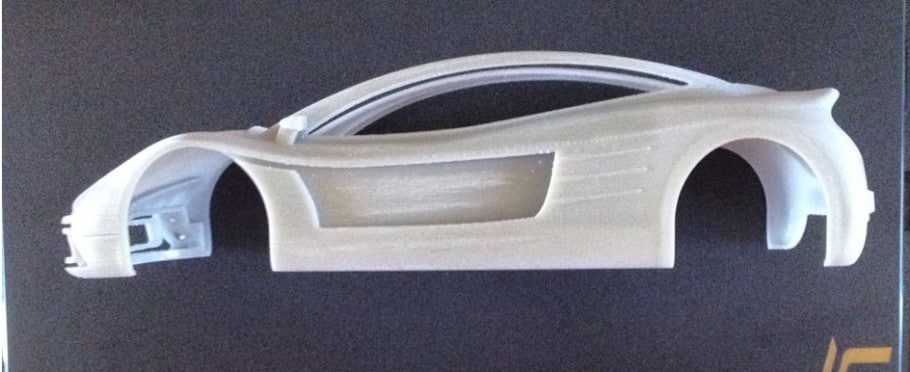
The most important criteria for RC body parts are UV resistance and impact resistance, as these two standards will determine the lifespan of the components.
Filament types are a personal choice, and each choice will either benefit or hinder the lifespan of the RC car. You may find yourself having to reprint certain parts like bumpers that keep breaking, so it’s best to follow guidelines on filament choices. As always, nothing is stopping you from experimenting with different or new filaments in the market.
ASA
ASA has a very high level of impact resistance and can withstand high temperatures as well as being highly resistant to UV rays. This puts ASA at the forefront of filament choices for RC body parts. Included is the ability of ASA to withstand harsh weather conditions.
The downside to printing with ASA is that high temperatures are required; 220°C to 245°C for the extruder and 90°C to 110°C for the bed. Another negative is that it produces hazardous fumes, and ventilation is required.
PETG
PETG has about 70% the strength of polycarbonate but is still a highly rated filament choice. The print temperature is between 230°C – 250°C with a bed temperature of between 70°C – 85°C. PETG has high tensile strength and is impact resistant as well as being resistant to UV rays.
This combination has made PETG a sought-after filament for RC car parts and is often chosen above ABS and other filament types.
Nonetheless, ASA is the preferred filament for UV resistance. The printing of both filament types is fairly easy, and both serve their purpose well. You may be swayed by availability at the time of purchase or by the price itself.
Why I prefer PETG for printing an RC Car’s Body
Both ASA and PETG are UV resistant and maintain high impact resistance, making them ideal for the body or outer components of RC cars. Due to its ease of printing, I personally recommend choosing to print the parts with PETG.
Although t could be argued that ASA is actually better suited for this use case, we should keep in mind that that thermoplastic comes with important disadvantages, namely its difficulty to print and its high price tag.
Filament for RC Car Wheels
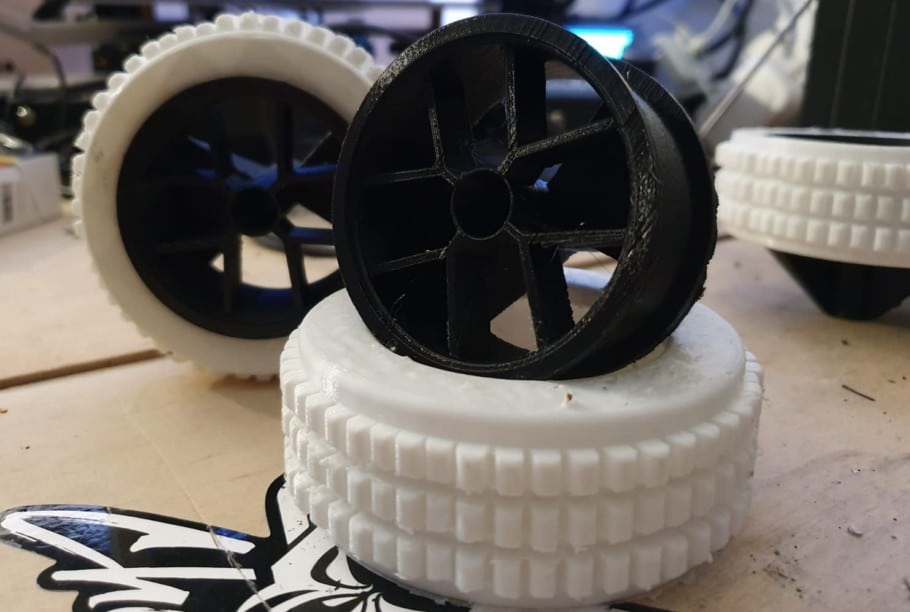
RC car tires create a slight problem for realists as they would like the tires to compare with real tires where there is a degree of softness and grip, but it’s not that easily achieved with 3D filaments. The best option is to use a filament that produces flexible prints as this will absorb vibrations and add to the wheels gripping on the terrain. TPU has been strongly recommended.
TPU
Thermoplastic Polyurethane (TPU) is flexible, soft, and wear-resistant, and it comes in different grades which offer varying degrees of flexibility. Road surfaces can become very hot, but TPU can withstand temperatures of up to 80°C (high glass transition temperature), so it will perform well in almost all conditions. TPU is also not affected by most chemicals, making it ideal for outdoor use.
When printing wheels, your focus should be to maximize the flexibility of the part, which you can further increase by simply reducing the infill percentage. The lower the percentage, the higher the flexibility you will achieve. Printing with the filament is relatively easy but may prove problematic when using a Bowden tube, plus the filament is prone to stringing due to its elasticity.
TPU’s properties make it unsuitable for most RC car parts, but it is ideal when printing bumpers and tires due to its high impact absorption qualities.
Choosing the right filament for printing an RC Car’s Bumpers
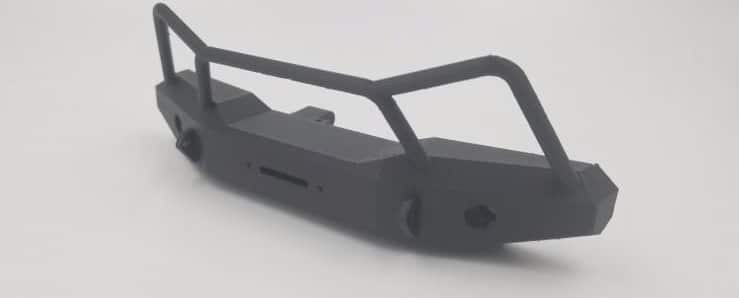
Bumpers take a lot of direct impacts and therefore need to be able to absorb the impact but still be strong enough to resist breaking or snapping on impact. Flexibility is key to functional bumpers, and Nylon or TPU with a high percentage of infill will offer both strength and flexibility.
Nylon
Nylon is a great filament for RC car bumpers as it is extremely strong, second only to polycarbonate. It also has a degree of flexibility that makes it ideal for the purpose. NylonX is a great filament for strength as it has carbon fibers that reinforce the nylon and is said to be impact resistant. Printing is easy, but due to carbon fiber’s abrasive nature, it is advisable to use a steel or hardened nozzle when printing.
The extrusion temperature of nylon is between 250°C to 265°C with a bed temperature between 60°C and 70°C. Extrusion temperatures on the high side of the scale may restrict printing for some printers, but printing is relatively easy nonetheless.
Filament for 3D Printed Springs
Printing springs can be very tricky but not impossible. The process largely depends on the size of the springs and, in most cases, will cause more headaches than anything else. However, if you are determined to overcome the challenge of printing your own springs, then the guys at MakeFast Workshop have come up with a solution that defies all the logic about 3D printing. They print single strand springs in thin air using a method to get the curves and angles right while cooling sufficiently to maintain the desired structure.
Conventional spring printing will require support material and possibly more than one layer to form the actual spring. The fact of the matter is that between conventional 3D printing and printing into thin air, springs can be printed, and I know from first hand that both printing methods will each present their own set of challenges.
Nylon
Nylon is my filament of choice for springs. It will stand up to strength tests and will offer the degree of flexibility required by the spring. Being fairly rigid, the spring will hold its purposed position, and the flexibility will allow the spring to expand and contract within the allocated limits. This is the same characteristic that makes nylon a great choice for RC car bumpers.
Conclusion
As we can see, when we make the transition from printing simple miniatures to creating functional parts, we must consider the specific needs of each element that will end up composing the final object. If we agree that a chain is as strong as its weakest link, we can also conclude that an RC Car is as functional as the suitable filament chosen.
In short, use ABS for the Chassis, PETG for the body, TPU for the tires and Nylon for both the springs and the bumpers. Of course, you could simply buy some metal springs as well and don’t go through the trouble of printing them yourself!
Also, PETG should work really well for the bumpers since it’s a fairly flexible filament.
Check out our recommended products section
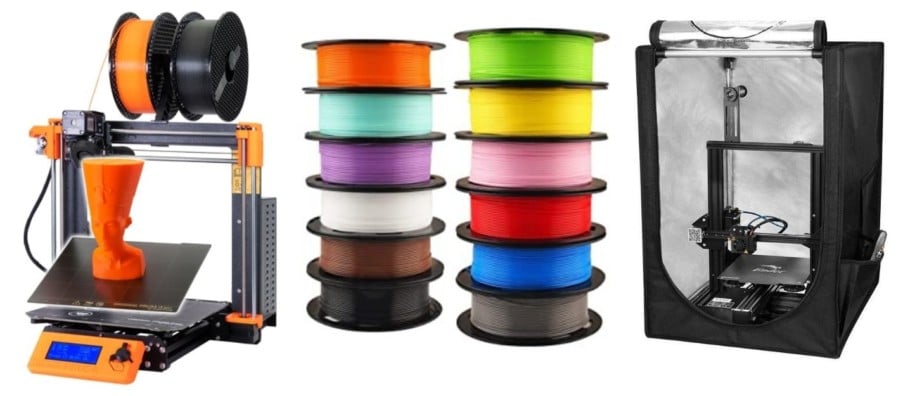
We created a recommended products section that will allow you to remove the guesswork and reduce the time spent researching what printer, filament, or upgrades to get, since we know that this can be a very daunting task and which generally leads to a lot of confusion.
We have selected just a handful of 3D printers that we consider to be good for beginners as well as intermediates, and even experts, making the decision easier, and the filaments, as well as the upgrades listed, were all tested by us and carefully selected, so you know that whichever one you choose will work as intended.
Error processing API data.