Did you know that you can print images with your 3d printer? Yes, like a regular printer but fancier and with a three-dimensional look. These images are called lithophanes and can be printed on a regular cheap 3d printer.
In this article, we will learn about 3D printed lithophanes: what they are, what the best way to print them is, which material we should use, and the steps to follow to create our own lithophane. Concisely, how can you create your own lithophane?
In order to create a custom lithophane, you need to select a high-resolution image with high contrast features. By means of free online tools, you can create an .STL file containing the lithophane, which you can then import to the slicer of your choosing. Before starting the print, it is very important to set the infill percentage at 100% in order to successfully print a lithophane.
Now that you already know the basics of a lithopane, you may be asking yourself what type of filament to use.
Due to the nature of lithophanes, white polylactic acid (PLA) stands out as the best filament type for this type of print. Nonetheless, it is important to state that PLA has a low glass transition temperature (about 60°C), so it is recommended to light the lithophane with an LED. They are more energy-efficient and waste less energy in the form of heat.
In cases where this is not an option, you should print the lithophane with PETG, which is more heat resistant but also more difficult to print.
What is a lithophane?
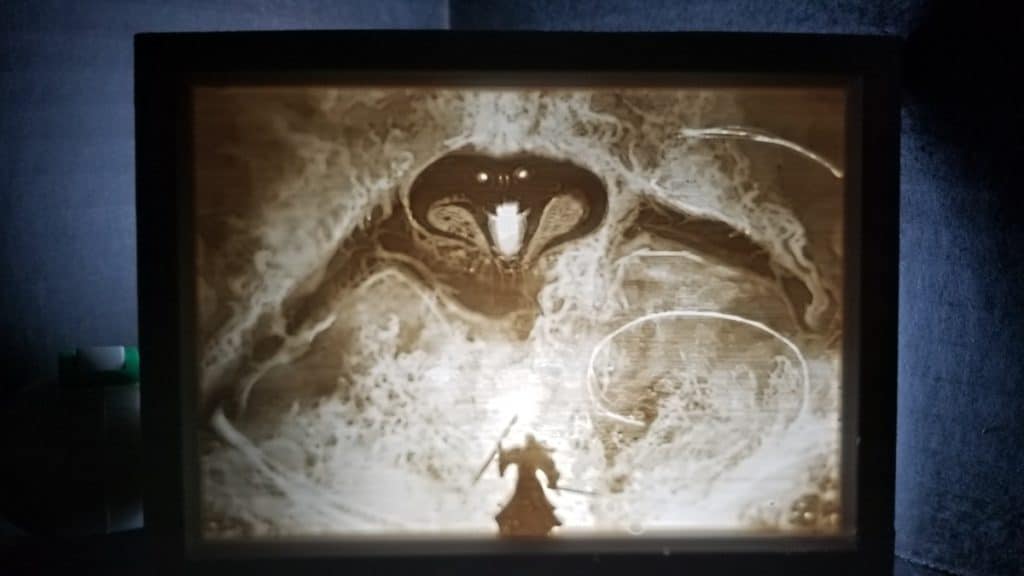
Lithophanes are images that can be seen passing light through a thin, translucent sheet. Because of the different levels of thickness in the sheet, light cannot pass through it in the same way at every point of the surface.
Thicker parts will seem dark while thinner parts will allow light to pass, making these areas seem more clear. The final result is an image, similar to a photograph.
In the past, lithophanes were carved in wax, but today we can use our 3D printers for that. If we think about it, these images are the results of different variations of thickness on a surface.
These variations can be done on a 3D printer, adding layers on the Z-Axis or increasing the quantity or thickness of lines in our design. Then, with backlighting or a lamp, we could see the image just like a normal photograph.
In other words, you can easily create an image of your family, friends, or pet for your home, using free tools. A lithophane is a great gift for special occasions. You can take a selfie and send it as a present to a friend after a special day together. Or you can make a lamp using lithophanes: when you turn it on, the images will be projected.
How to create a custom lithophane
Before we get started creating our own lithopane, lets do a quick checklist of the things we will need to get this job done!
–A 3D printer: we’ll assume you have a perfectly calibrated printer and you are an expert user (or so). In case you do not have one, you will still be introduced to a new application of 3D printing that you didn’t know. Just make sure your axis’ steps are properly calibrated, otherwise, your image will look distorted. Also, retraction settings must be set properly, or the stringing in your object will affect the print quality.
–A photograph or an image: it can be anything that comes to your mind. To get started, you can choose simple images (for example cartoon characters) or some high-contrast designs. If you do this, your first samples will be faster to print and you’ll be able to fix any mistake that shows up.
JPG format is best used for images in this case because of its size and high image quality.
–A slicing software: use your favorite. You won’t need any complex tools. With the sole exception of infill percentage, we will mainly be using regular settings. If you are proficient in obtaining good prints from your machine, keep most of the settings you regularly use.
Just remember to set the infill percentage at 100%. Otherwise, you will end up with a lithophane of a translucent grid (or honeycomb, or the pattern you use for infill). I use Cura as my go-to slicer, but, again, any slicer will be fine.
–An online tool to convert images into STL files: although you can use advanced design software like Adobe Fusion 360 to create a lithophane, we can skip the learning curve and go straight to online tools that are designed for this sole purpose.
In this article, we will be using a free online tool that does not require registration, offers lots of customization options, and yields awesome results. It is developed by 3dp.rocks and you can check it out here.
Creating your lithophane
Once you’re on the website, click the “IMAGES” button and then upload the image that you choose from your computer.
To make your first try easier, choose the “FLAT” type on the bottom menu. Once you’re done with your first lithophane and happy with the results, you could try more complex shapes.
Click “Refresh” and then “Settings”. This will open a menu with multiple options.
The first one is “MODEL” and it allows us to adjust the size and resolution of the lithophane. I recommend you start with a Maximum Size of 150 mm, a thickness of 3 mm, and 0 for the border.
“Thinnest Layer” allows us to choose the smaller width of the image. Here, I advise you to set the width of your nozzle. I usually use 0,4 mm. A smaller nozzle size will improve the image quality but it will increase the printing time.
You can modify the rest of the settings once you master this awesome tutorial.
The second option in the menu is “IMAGE” Settings, and it contains different effects to apply to your lithophane. For now, we’ll let everything as default except “Negative Image”: we will change it to “Positive Image”. Click on Refresh after that.
The last option menu is “Download Settings”, and it allows us to change the format of our 3D file. Select binary and manual to continue. Now that you are ready to download your lithophane, click on download and import your 3D model into your goto slicer.
Slicing your lithophane
It’s very important that you decide in which position you’ll print the 3D model. You can either print it vertically or horizontally. If you choose the first one, the layer height can be less than the nozzle width, and that improves the resolution of the image. I recommend you to use 0,1 mm as layer height.
The disadvantage of printing a lithophane vertically is that printing time will increase drastically. This can be reduced by adjusting jerk and speed settings, but this time let’s focus on getting a nice print instead of making it fast.
If for some reason you prefer to print horizontally, you’ll have to change the “thinnest layer” setting into the chosen layer height. Because of the lower resolution, the smallest details in your lithophane may disappear, so I don’t recommend you print it this way.
Printing speed is another key parameter in this project: to maintain a high resolution in your image, you’ll have to slow down the speed to 30-40 mm/s. Small differences in your object’s perimeter will result in ugly marks, so start slowly and increase speed later when you are comfy.
The importance of movement speed when printing lithophanes can not be overstated. Take a look at the following example of the same file printed in different settings:
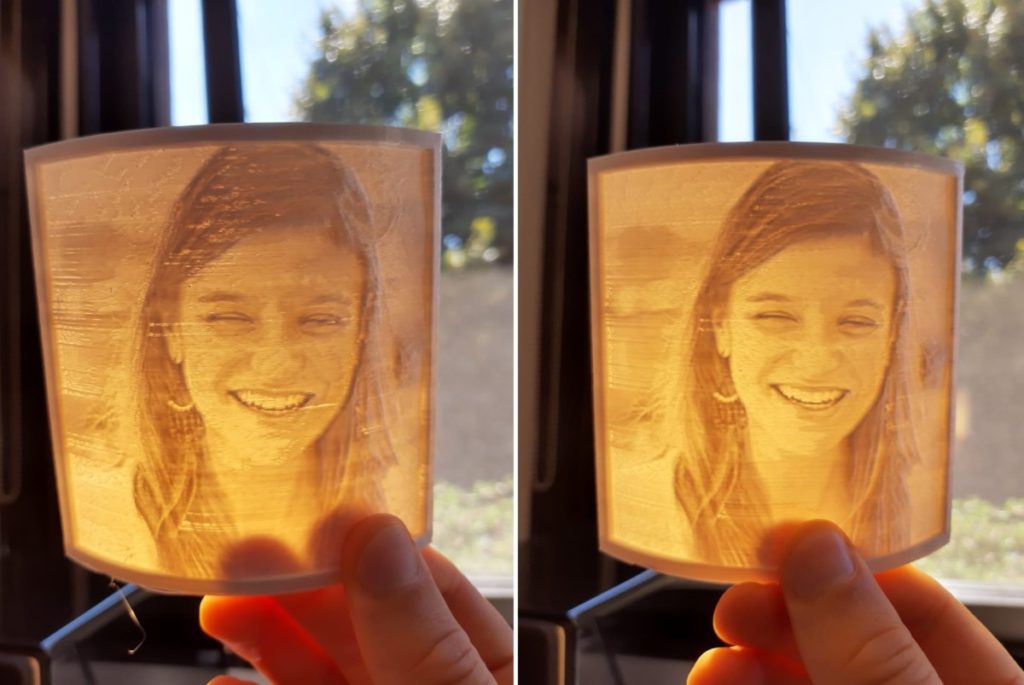
There are only two differences between both prints, but they greatly improved the outcome. The movement speed was reduced from 45mm/s to 30mms/s, while the layer height was taken from 0.3mm to 0.2mm. The filament used in both cases was a generic white PLA that I had laying around (properly preserved and in good condition).
The increase in printing time was noticeable, but in the broader scheme of 3d printing, lithophanes don’t require that much filament or time.
The infill percentage in your print must be at 100%. Otherwise, the slicer won’t fill the thicker spaces and the “darker areas” effect won’t come out.
Best materials for printing lithophanes
As you know, PLA is the friendliest material to use, so it is a great option to print lithophanes. When the thinnest parts are printed, it seems translucent, and it becomes darker when the thickness increases. This effect becomes even more notorious when a white PLA is used.
Although you can use any light color, white is the best option for this because it achieves the best results even with low power lamps. Dark colors don’t let the light pass through the lithophane, so these are not suited for this.
The disadvantage of 3D printing lithophanes with PLA is the limited thermal resistance of this material. At 60°, PLA starts to lose its shape and becomes soft. Many people make lithophane lamps, and if the lightbulb gets too hot, PLA could melt and ruin the object. A great solution for this is to change the lamp for one with LED lights. These are brighter and don’t heat up too much.
Another great option to print lithophanes is PETG, which is even more translucent than PLA (soda bottles are made of this material). It can withstand higher temperatures and doesn’t break so easily. As a negative part, this material is not that easy to print. It can cause more warping, low adherence between layers, and delamination. Besides, it requires a heated bed to be used.
Nylon can withstand up to 90ºC and it’s even more translucent than PLA so it can be used for this kind of print. If you are very skilled in 3d printing you can try a Nylon lithophane, but in my opinion, it’s not worth it.
This material is more expensive and really difficult to print. It must be dry or it will start clogging. Also, you will need a special hot-end: Nylon needs nearly 250ºC to be printed. If your extruder has 3d printed parts, forget about Nylon.
I don’t recommend using ABS for this. It’s true that it can resist higher temperatures, but the opacity of this material is too high. Thin ABS layers can block all of the light from the lamp, so you won’t be able to see any image in your lithophane.
In a nutshell, PLA stands as the best option. Now choose an image, turn your printer on, and get into the lithophanes’ world!
Recommended Materials: White PLA Filament and white PETG filament.
Can you print a lithopane with an SLA printer?
It is absolutely possible to print a lithophane using a resin-based SLA printer. In fact, the level of detail and precision that can be obtained by using this type of printer is going to be much higher in comparison to an FDM printer. Nonetheless, lithophanes are commonly not printed using SLA technology because of the rather small build surface that these printers usually have.
Best Slicer settings for printing Lithophanes
No matter what Slicer you use, the settings won’t be any different. In fact, some slicers may already include a specific profile for printing Lithophanes, so you could try those ones out first.
Since PLA will probably be your filament of choice, here are the ideal settings for achieving high-quality lithophanes.
Ideal Slicer settings for printing Lithophanes (PLA):
- Printing Temperature: 200 – 210 ºC
- Bed Temperature: 50 – 65 ºC
- Layer height: 0.12 mm up to 0.2mm for greater detail
- Retraction: 6 mm
- Infill: 100%
- Speed: 50 mm/s
- Initial Layer Speed: 20 mm/s
- Initial Layer Height: 0.2 mm
- Initial Fan speed: 0%
- Fan speed (after the initial layers): 100%
If you decide to give it a try using PETG, then simply adjust the print and bed temperatures accordingly: Print temperature 230ºC and Bed temperature 80ºC.
Conclusion
Printing lithophanes is much easier than most people think, since you only need to upload the image to the software which will convert it into a file that can be sliced by the slicer, set the infill to 100% and that’s about it.
So, I hope that you give it a shot and print your first lithophane soon!
Check out our recommended products section
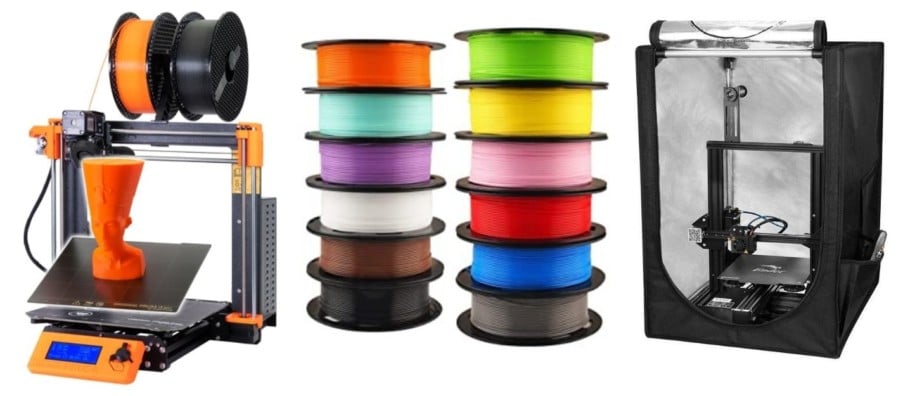
We created a recommended products section that will allow you to remove the guesswork and reduce the time spent researching what printer, filament, or upgrades to get, since we know that this can be a very daunting task and which generally leads to a lot of confusion.
We have selected just a handful of 3D printers that we consider to be good for beginners as well as intermediates, and even experts, making the decision easier, and the filaments, as well as the upgrades listed, were all tested by us and carefully selected, so you know that whichever one you choose will work as intended.
Error processing API data.
That was a very nice read. Spot on with all of the facts. I am looking at filaments and which one exactly should be used. From your article I am going to try a PLA Plus as it has all of the qualities you say is lacking in regular PLA. Thank you so much for your insite and please do not stop with this website. Awesome name and awesome logo. I have an Ender 3 with Micro Swiss Hot End. Chose to stay with an upgraded extruder. It is also in an Enclosure so when I print I get what the settings print. That is why I wanted to really thank you as you saved me money and time brother. God Bless. If you need some input just let me know what your working on and would be gald to help out.